- FMA
- The Fabricator
- FABTECH
- Canadian Metalworking
Every second counts with automotive Tier 1 supplier Sodecia
London, Ont., operations see benefits in robot start/stop reaction time
- April 27, 2023
- Article
- Automation and Software
The need for speed is still alive and well in the automotive Tier 1 supplier world. Just ask Rob Remillard, engineering manager at Sodecia’s Global Technology and Automation Center (GTAC) facility in London, Ont. He and his team provide all the part assembly and part handling automation equipment for the company’s 48 worldwide plants that produce assemblies for all the major automobile OEMs.
But speed is not always about shorter cycle times. In Remillard’s world, speed often concerns robot acceleration/deceleration reaction time: basically, how fast a robot starts and stops. In fact, that start/stop reaction played a critical role in one of GTAC’s recent projects, and it was a deciding factor in the company’s robot selection process.
Calculating Robot Needs
Sodecia's core competencies include its Safety and Mobility Group, which produces such components as seat belt height adjustors and cross car beam assemblies and the BIW Group, which produce frame rails, rockers, floor pans, and more. The company now produces these complete vehicle floor pan assemblies for body-in-white assemblies and performs all the necessary processing, from stamping and welding to sealing and finishing.
For such projects, GTAC starts with necessary volumes/yearly quantities and all other part data. GTAC then determines how best to automate all the processes to produce the parts as quickly and efficiently as possible. For example, a part may have a volume of 196,000 units per year, so the shop will then work backward from that production number to determine how many parts it must produce during a three-shift operation.
“We then determine how many robots are needed to do all the processes on the part in that amount of time,” explained Remillard. “How many will it take to do the welding and apply all the sealant, how many parts can an operator load in that amount of time, and so on. We will engineer a process with the minimum number of robots, operating stations, and other systems and run the automation as fast as needed to meet the target cycle time.”
Testing Robot Options
GTAC’s current automotive floor pans project is quite large and is divided into four stages and six main cells. Each cell uses eight robots, two unload robot cells, and nine robots to perform sub assembly and other miscellaneous tasks. The most recent stage of the project involves two main cells and eight robots to do spot welding, sealant, and stud welding. Each pan requires about 700 welds.
According to Remillard, reaction time, positioning accuracy, and speed are the key reasons that GTAC chose the robots they are using. In fact, he conducted a study of several robot OEMs based on documentation and then brought the three finalist robots in-house for side-by-side brand comparisons. They chose robots from KUKA Robotics for the floor pan project.
“In our business, when we do weld after weld after weld with small moves in between, the KUKA acceleration/deceleration reaction time is exceptionally fast, within milliseconds, as are their positioners. This saves us a significant amount of time per part just in signal reaction time, and the robot’s signal processing time is one-fiftieth of the competition.”
Remillard went on to note that the problem with slim, less-robust robots has to do with payload. In the floor pan cell, GTAC moves loads up to 210 kg, so its robots must be built to move that much weight around easily without being affected by the involved inertia forces that result from fast, abrupt stops and starts. “With KUKA, there is little if any ramping-up-to-speed time or coming-to-a-stop time. They do it practically instantaneously,” he said.
Controls
The robots’ control system was another factor in Remillard’s decision-making process. Its wide-open design meshes with GTAC’s needs. It allows GTAC to take advantage of all available functionality and perform a lot of operations on its own without assistance from the vendor. Additionally, plug-and-play packages like spot-ready [KUKA ready2_spot] and arc-ready [KUKA ready2_arc] systems enable the shop to incorporate the robots into their automated cells without having to mount their own welding guns or integrate other components.
Within the floor pan cell, the KUKA robots include KR 30 IONTEC and KR 210 QUANTECs, along with KP1 and KP3 positioners. The production process starts when operators load the KUKA KP3 positioner with floor pan sections. The positioners bring the parts into the cell, where multiple robots spot weld and apply adhesive. After welding is complete, a robot moves the assembly to a pedestal station for drawn arc stud welding. In a unique operation within the cell, one KUKA robot hands off an assembly to another robot.
Ag Expansion
GTAC's customers are all of Sodecia’s automotive production facilities, but it is now also offering its engineering and integration services to other non-automotive customers in different markets as well. One such sector is the agriculture industry.
“For us at GTAC, and because we are starting out and basically still doing a lot of internal work, our goal at the end of the day is not just to develop a process that works, but to make our customers better, more efficient, and more cost-effective,” said Remillard. “Whether that’s Sodecia or a new outside customer, they come to us with a need to make a part, and while some integrators will offer the bare minimum when it comes to a process to produce that part, we aren’t like that. GTAC has set standards across the board and applies all that we’ve learned from past projects.”
KUKA Robotics, www.kuka.com
Sodecia, www.sodecia.com
subscribe now
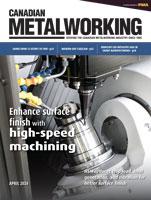
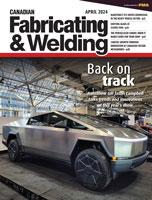
Keep up to date with the latest news, events, and technology for all things metal from our pair of monthly magazines written specifically for Canadian manufacturers!
Start Your Free Subscription- Trending Articles
Aluminum MIG welding wire upgraded with a proprietary and patented surface treatment technology
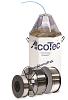
Achieving success with mechanized plasma cutting
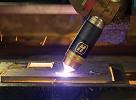
Hypertherm Associates partners with Rapyuta Robotics
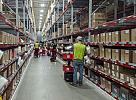
Brushless copper tubing cutter adjusts to ODs up to 2-1/8 in.
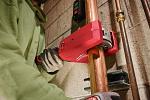
Gema welcomes controller

- Industry Events
MME Winnipeg
- April 30, 2024
- Winnipeg, ON Canada
CTMA Economic Uncertainty: Helping You Navigate Windsor Seminar
- April 30, 2024
- Windsor, ON Canada
CTMA Economic Uncertainty: Helping You Navigate Kitchener Seminar
- May 2, 2024
- Kitchener, ON Canada
Automate 2024
- May 6 - 9, 2024
- Chicago, IL
ANCA Open House
- May 7 - 8, 2024
- Wixom, MI