Editor
- FMA
- The Fabricator
- FABTECH
- Canadian Metalworking
The time is now for automation, say MM Expo panelists
Supply chain upheavals a challenge and an opportunity
- By Rob Colman
- April 22, 2022
- Article
- Automation and Software
If you are not automating during this time of supply chain upheavals, you are already falling behind. That was one of the messages conveyed by the panel of experts who spoke at the Abbotsford Metalworking & Manufacturing Expo (MM Expo) on March 29.
The topic of the keynote panel discussion was “Resiliency, Agility, and Pivoting: Changes COVID has brought to manufacturers in B.C.” Panelists Leigh Christie, Udo Jahn, and Jason Zanatta discussed the importance of innovation, people, and how the two relate in terms of automation.
“The supply chain issues we’re seeing around the world are a massive opportunity for Canadian manufacturers,” said Christie, founder of MistyWest, a Vancouver-based engineering design company focused on intelligent and connected devices.
“My whole business right now was created based on that supply disruption,” said Zanatta, owner and CEO of Novo Textiles (Novoshield PPE), who essentially reinvented his company as a PPE supplier during the pandemic.
Succeeding and thriving into the future requires automation.
“If we didn’t have automation, with the need to reshore production during the pandemic, the business pressures would have killed us,” said Jahn, general manager of Modern Engineering, which specializes in producing advanced machined components. “I think that the pandemic was an opportunity for manufacturers to accelerate their automation investments. These disruptions aren’t over. The challenge in Canada is that we are afraid to invest in ourselves.”
“I was in the textile business for 20 years before the pandemic,” said Zanatta. “All my orders started drying up before the first U.S. case was reported. I had staff who had been with me for 10 to 15 years and the idea of laying them off was not sitting well with me. On a flight home from the U.S., I reached out to a machine manufacturer in China, the only place you could buy mask-making machinery at the time. They said they already had orders for 180 machines so mine would take 3 to 6 months to arrive. Instead of waiting, I paid a premium to get a machine expedited and worked with the B.C. government to get it on a plane. By the following Wednesday the first machine arrived in Coquitlam, we started making masks about a week later. I hired two BCIT mechatronics grads to get those machines running, and literally a week later Trudeau made his announcement about having manufacturers pivot into a PPE space.”
By that summer, the company was producing 30,000 masks a day. Zanatta has since replaced all his Chinese equipment with European and Canadian-made machines. In half a day his shop produces about 300,000 masks.
Both Jahn and Zanatta have further invested in cobots to improve operations.
“Scaling as we did so quickly, we went from 10 employees to about 50 that summer, and there was a constant churn of about 10 to 20 per cent,” said Zanatta. “We very quickly learned we needed to automate a lot of those positions. We brought in five UR cobots. Anytime there’s a repetitive task like erecting cartons and sealing cartons, we automated it. Any dollars we have we are investing in automation. We have to be ready to compete with cheaper imports that will come as supply chains improve again. My staff are easily operating cobots day in, day out. They’re going home happier, they’re not sore anymore, their jobs are more rewarding, they are more into their jobs than they were before, and quality is consistent coming off the line.”
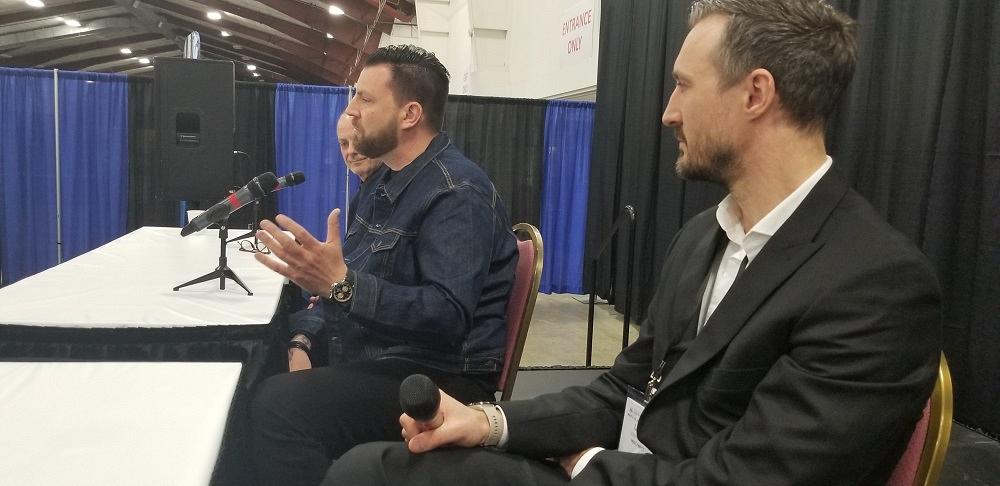
Jason Zanatta (centre) addresses the crowd during the morning panel discussion with Leigh Christie (right) and Udo Jahn.
Jahn has four cobots and two robots on his shop floor now.
“You could see the fear in the eyes of employees when these first arrived,” said Jahn. “They thought of it in terms of the old philosophy of robotics, which was ‘Robot in, human out.’ Now it’s more like human augmentation.”
Jahn uses his cobots strictly for loading and unloading machines.
“The secret to using robots is to keep it simple,” he said. “Give it one thing to do and make sure it does it well. If you make it do two things, programming becomes more complex and there’s the potential of having to scrap parts. The simpler you make it, the more productive it will be.”
Both Jahn and Zanatta are finding that having the technology on the floor encourages staff members to come up with new ways in which to use it to improve processes.
“When the person is observing the technology, you can double or triple your productivity because that person is now relaxed, observing, and can see how to make the process better,” said Jahn. “The biggest side effect of robots is improved quality.”
The problem for Jahn isn’t that technology will replace people, it’s that there are not enough young people pursuing the trades to fill the needs of manufacturers. Jahn puts some of the blame squarely on the shoulders of manufacturers.
“One of the issues I see right now is a lack of apprenticeships in industry, people willing to focus on young people,” he said. “What’s the common argument we hear? If we train them, they’re going to leave. But you’ve got to treat your businesses like a sports franchise. You’ve got your draft choices—you’ve got your entry level, you’ve got your journeymen, your free agents. What happens to free agents? They leave. But if you have good training processes in your facilities, you won’t have that problem because there’s always people coming through.”
The other challenge is encouraging students to join the trades, and in support of that Jahn has worked with BC Metal Manufacturing Advisory Group to put CNC machines into 10 high schools in B.C., so that young students can get an introduction to modern machining practices.
Christie pointed out that his whole business is basically built on the skills gap issue. His company is called upon to develop what companies can’t themselves because they don’t have the know-how. The work his company is increasingly focused on today are many of the technologies that are gradually making their way onto shop floors.
“People used to come to us for innovations, whatever that might look like,” he said. “Now it’s very specifically for intelligent and connected devices—wireless communications and associated chip sets, computer vision technology, and custom sensors.”
All the panelists encouraged attendees to think towards the future.
“What we really want to see here in B.C. and across Canada is for companies to be much more aggressive in their spending on innovation and engineering,” said Christie. “There’s a reason MistyWest has to go to the U.S. to find customers, and that’s because that’s where the risk takers are.”
The key is to work towards adapting to survive and thrive.
“People say, ‘Automation doesn’t fit my process.’ Well, change your process,” said Jahn. “Everyone thinks they’re special. You’re not special. Refine your processes so that you don’t need that special tool or that other workaround and you can find a way towards automation.”
About the Author
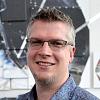
Rob Colman
1154 Warden Avenue
Toronto, M1R 0A1 Canada
905-235-0471
Robert Colman has worked as a writer and editor for more than 25 years, covering the needs of a variety of trades. He has been dedicated to the metalworking industry for the past 13 years, serving as editor for Metalworking Production & Purchasing (MP&P) and, since January 2016, the editor of Canadian Fabricating & Welding. He graduated with a B.A. degree from McGill University and a Master’s degree from UBC.
subscribe now
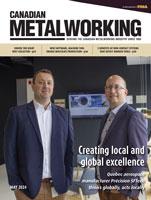
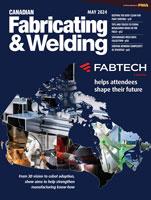
Keep up to date with the latest news, events, and technology for all things metal from our pair of monthly magazines written specifically for Canadian manufacturers!
Start Your Free Subscription- Trending Articles
Aluminum MIG welding wire upgraded with a proprietary and patented surface treatment technology
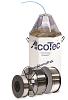
Hypertherm Associates partners with Rapyuta Robotics
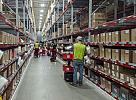
Protected and productive: welding helmet tech
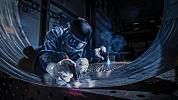
HGG Profiling Equipment BV names Western Canada area sales manager
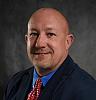
Compact weld camera monitors TIG, plasma processes
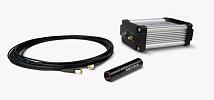
- Industry Events
Automate 2024
- May 6 - 9, 2024
- Chicago, IL
ANCA Open House
- May 7 - 8, 2024
- Wixom, MI
17th annual Joint Open House
- May 8 - 9, 2024
- Oakville and Mississauga, ON Canada
MME Saskatoon
- May 28, 2024
- Saskatoon, SK Canada
CME's Health & Safety Symposium for Manufacturers
- May 29, 2024
- Mississauga, ON Canada