- FMA
- The Fabricator
- FABTECH
- Canadian Metalworking
A guide to tooth pitch
Go with a coarser pitch than a fine pitch when cutting soft materials
- March 6, 2024
- Article
- Fabricating
Sawing experts outlined a rule of thumb that should be followed when determining tooth pitch of a blade.
According to Russell Chibe, territory manager, Midwest, at Cosen Saws, Charlotte, N.C., there are four numbers to remember: three, six, 12, 24.
Three is the fewest number of teeth that you should have in the workpiece at any given time. You never want more than 24 teeth in the workpiece at a time either. The best cutting situation is to have six to 12 teeth in the workpiece.
One of the myths of working with soft materials is that they are easy to cut and that any blade will work, but a lot of operators are working with the wrong pitch for their material.
Learn more about the myths of sawing soft materials
For example, if an operator is cutting a 4-in. cross-section of aluminum and he wants to go with a 4/6 TPI pitch, he would have to multiply that by the 4-in. cross-section, and then he would end up with a 16 to 24 teeth in the workpiece at one time.
“However, in that situation, you’d want closer to six to 12 teeth, so a coarse pitch, like a 3/4 TPI, will get you to 12 to 16 teeth in the workpiece at one time,” said Chibe. “An optimum pitch would probably be a 2/3 TPI, which gets you around eight to 12 teeth.”
It is almost always advisable to go with a coarser pitch than a fine pitch when cutting soft materials.
“With softer materials, you don’t necessarily need to worry about teeth penetration by nature of the softness of the material,” said Jay Gordon, North American sales manager, saws and hand tools at The L.S. Starrett Co., Athol, Mass. “However, the issue to worry about is filling up the gullets before the blade gets out of the material, where the chips can be washed away or wiped out using a chip brush.”
According to Gordon, choosing a coarser blade will solve a lot of issues with gullet loading as it has bigger gullets. He also noted that increasing the blade speed with help clear out the chips and limit the blade’s ability to take a deep bite.
“It really depends on the size of materials being cut,” said Jens Thieme, chief technology officer, WIKUS Canada Ltd., Mississauga, Ont. “With smaller materials, you generally want more teeth per inch, and larger materials, less teeth per inch. If you are working with structural steel, H- beam, round tubing, square tubing, angle iron, there are some options available that offer a different shape of tooth that will create different rake angles.”
When getting into higher positive rake angles, the blade becomes more aggressive. When cutting soft materials, an extremely aggressive cut isn’t required like it is for nickel alloy or INCONEL. For the most part, it’s best to use a smaller positive or zero rake angle.
subscribe now
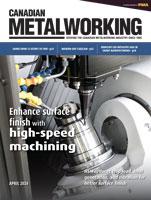
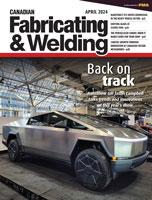
Keep up to date with the latest news, events, and technology for all things metal from our pair of monthly magazines written specifically for Canadian manufacturers!
Start Your Free Subscription- Trending Articles
Aluminum MIG welding wire upgraded with a proprietary and patented surface treatment technology
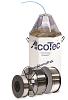
Achieving success with mechanized plasma cutting
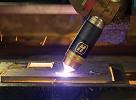
Hypertherm Associates partners with Rapyuta Robotics
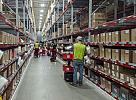
Gema welcomes controller

Brushless copper tubing cutter adjusts to ODs up to 2-1/8 in.
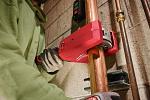
- Industry Events
MME Winnipeg
- April 30, 2024
- Winnipeg, ON Canada
CTMA Economic Uncertainty: Helping You Navigate Windsor Seminar
- April 30, 2024
- Windsor, ON Canada
CTMA Economic Uncertainty: Helping You Navigate Kitchener Seminar
- May 2, 2024
- Kitchener, ON Canada
Automate 2024
- May 6 - 9, 2024
- Chicago, IL
ANCA Open House
- May 7 - 8, 2024
- Wixom, MI