Editor
- FMA
- The Fabricator
- FABTECH
- Canadian Metalworking
Accelerating change at Brunswick Steel
Winnipeg service centre extends shop to add technology, production flow
- By Rob Colman
- January 18, 2024
- Article
- Fabricating
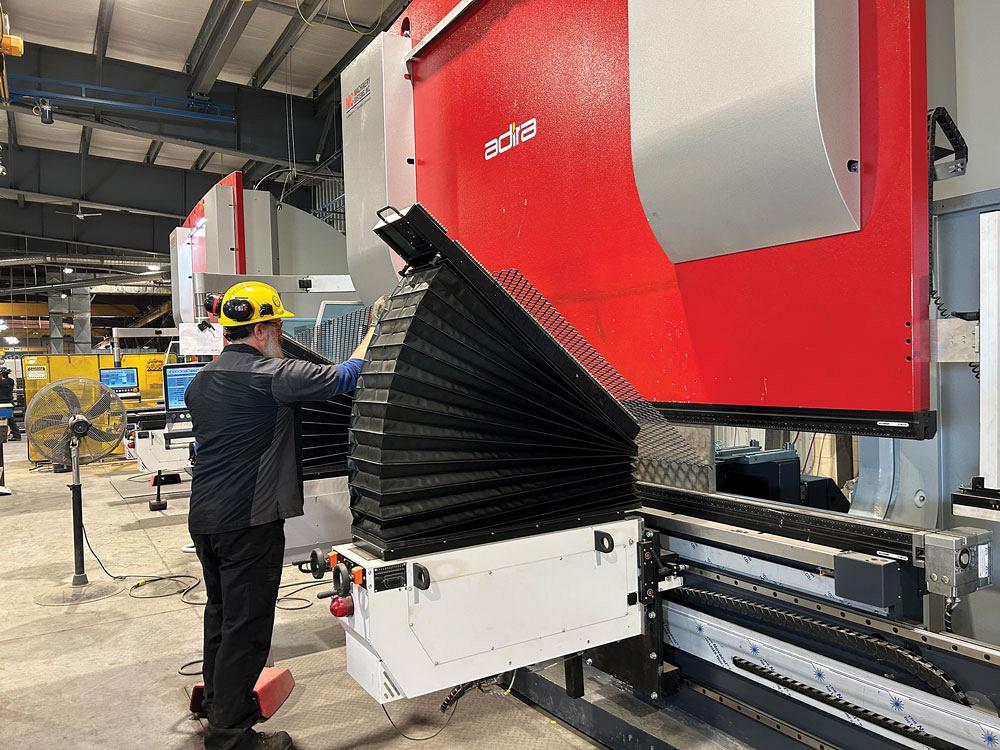
Brunswick invested in three Adira 400-ton hydraulic brakes that sit side by side on the shop floor. Each brake is equipped with a lift assist device and its own crane so that most bending operations at each station can be handled wholly by one individual. A roller table also is used to move parts between each brake when multiple setups are used in production. Brunswick has added various tools like this on the shop floor to ease workflow and improve safety. Photos: Brunswick Steel
Adding new machinery in a well-established shop can be a huge challenge. Not only do you want to add the best machinery to meet your needs, you also want to ensure those machines increase productivity and improve the flow of parts on the shop floor.
All of this was top of mind at Winnipeg’s Brunswick Steel as they were planning their building expansion—a 32,000-sq.-ft. workspace that the company opened up to customers and suppliers for the first time during a grand opening in October.
The metal service centre’s management team understands that efficiencies can be found in many forms—from new equipment investments to rethinking how a shop floor flows. Often, it’s a combination of the two that pays the greatest dividends. With its addition of a new tube laser, a new 12-kW fibre laser for sheet cutting, and three new press brakes, the company has armed itself for expansion. But it’s the people, processes, and peripheral tools as much as the machines themselves that are likely to make a big impact on Brunswick’s productivity.
Diversified Processing
“Essentially what we are working towards is our vision of being the fastest and easiest supplier in the marketplace to work with,” said Justin Copp, president and co-owner of the company. “We are reinvesting in the company for the future, with an eye on more processing capabilities.
“While we have upgraded some equipment, we’ve also added new technologies that expand our capabilities,” he continued. “The tube laser is a prime example of that.”
Brunswick invested in a BLM Lasertube LT8.20 that can handle tubes and profiles up to 40 kg/m in weight and tube diameter ranges from 12 to 240 mm. It is equipped with a bundle loader and a single-piece step loader, depending on how materials are loaded. In addition to laser capabilities, the machine also is equipped with drilling, tapping, and flow drill systems.
“We have wanted to expand into laser tube cutting for some time but just didn’t have the physical space,” said Copp. “This matches perfectly with our No. 1 selling product line, which is structural tubing, married up with parts production, which we already do a fair bit of.”
Copp considers the BLM to be the best choice for Brunswick. That doesn’t mean there wasn’t a learning curve for the Brunswick team.
“We are more used to cutting 2D parts, so working with a three-dimensional shape, learning how to use and manage files related to cutting in 3D, and the controls on a new machine—there was definitely a learning curve there,” he explained. “But it has been about six months since we installed the machine and we’re getting more proficient every day and starting to see real productivity come from it.”
AI-Enhanced Cutting
The flatbed laser the company purchased is a 12-kW Mitsubishi, which works next to Brunswick’s older Mitsubishi 8-kW laser. Both are attached to the same tower system, creating one larger cell for sheet cutting.
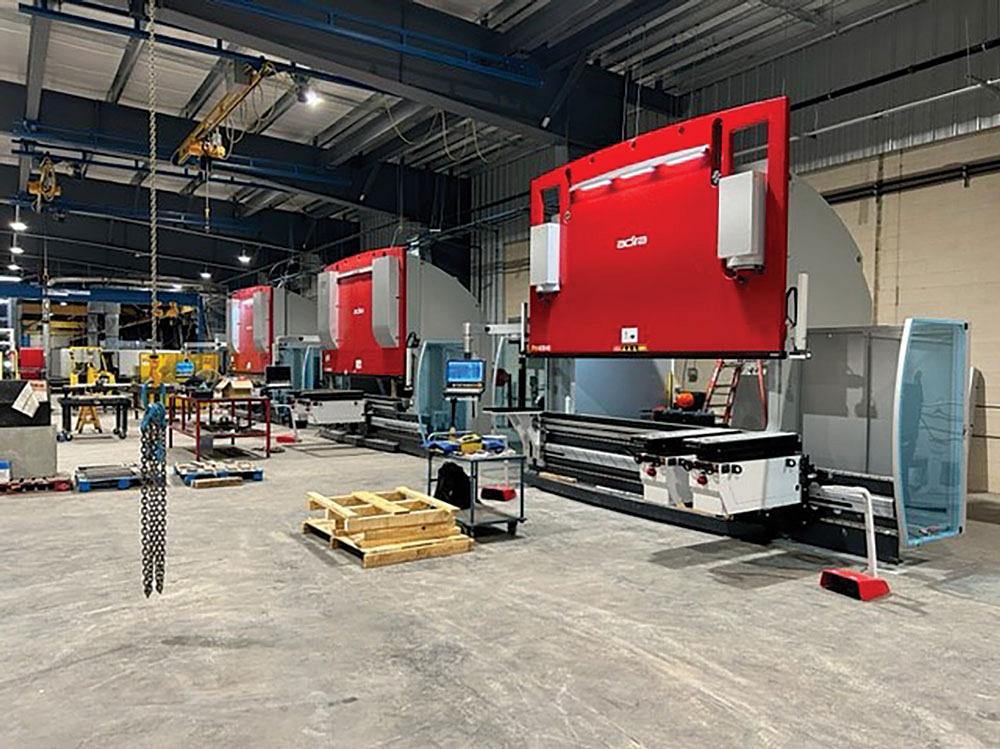
With the same operating system on each machine, the company can train people quickly to run any of the machines. It also makes it possible for the team to program jobs in a more creative manner.
“The 12-kW machine has some added functionality that is very interesting, such as AI that is actively listening to and watching the cut and adapting to conditions as it cuts,” said Copp. “It will also monitor the nozzle and change it out if needed, without any operator intervention.”
Given its power, Copp says the 12-kW laser will be geared toward cutting thicker materials. The company cuts a lot of ¼- to ½-in. material, so Copp expects to see time savings using the new machine.
“It’s roughly 40 per cent faster than the 8 kW,” said Copp.
Press Brake Part Flow
Part of the decision to go with another Mitsubishi laser was because the operating system is one that the team is comfortable with, so it’s easy to adapt to the new machinery.
The company’s press brake investment for the building expansion was similar. Brunswick invested in three Adira 400-ton hydraulic brakes that sit side by side on the shop floor. With the same operating system on each machine, it’s easier to train people quickly to run any of the machines.
“We’re hiring more for cultural fit rather than skills knowledge, so being able to on-board people quickly and scale up is easier if all machines we’re working with are similar,” he noted.
Copp also said it’s easy for the team to program jobs in a more creative manner.
“We are moving to off-line programming and in some cases we may spread the same job across the three machines, to avoid tooling changes and keep part flow elevated,” Copp explained. “For instance, we have one particular part that is fairly complicated and has 23 bends on it, some of which are very complex and cannot be backgauged easily. It would typically take us 24 hours to process an order for this particular customer. However, using the three brakes in sequence, without tooling changes, we can break that production job out to flow parts through that department more quickly. This has resulted in a total time of six hours to complete the job, a savings of 18 hours of press brake time.”
Each brake is equipped with a lift assist device and its own crane so that most bending operations at each station can be handled wholly by one individual. “With individual cranes dedicated to the brakes, these cranes are not shared resources and are available at any time for our brake operators,” said Copp.
“We are really trying to cut back on shared resources,” he continued. “When you’ve got two or three pieces of equipment sharing a crane or forklift, inevitably someone is always waiting, so we’ve tried to eliminate those bottlenecks as much as possible.”
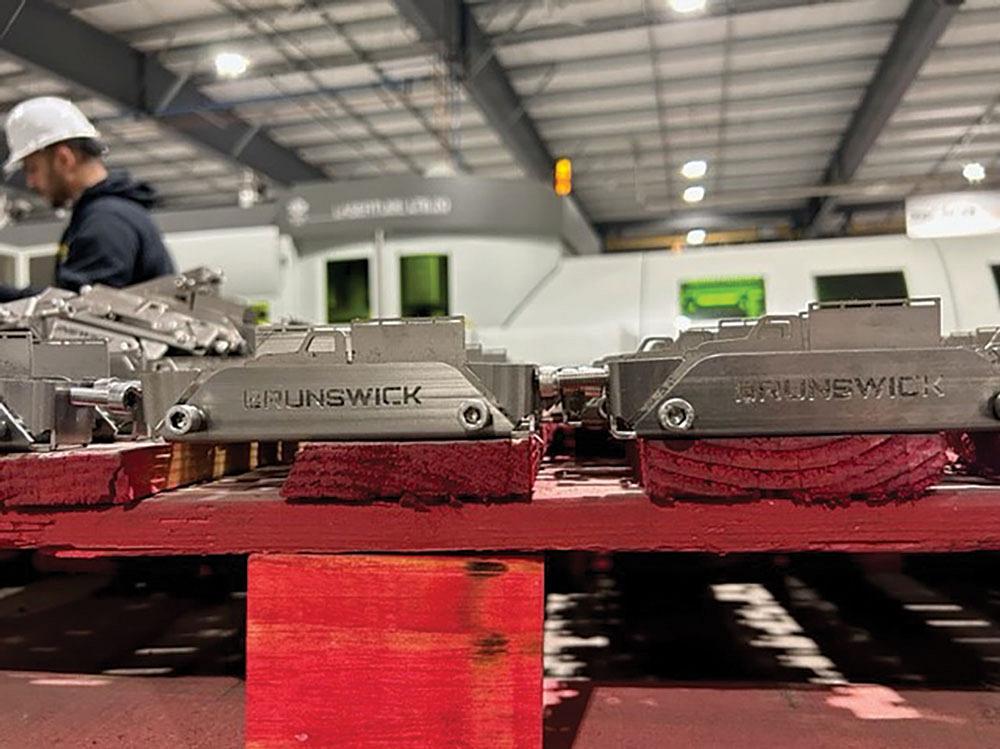
During the Brunswick Steel’s grand opening celebration for its new 32,000-sq.-ft. building expansion, the company produced sample parts to show off the capabilities of its new BLM tube laser.
Production Flow Investment
As mentioned earlier, the machines themselves are only part of the investment Brunswick has made. Before investing in the machines, the company received a grant from the National Research Council’s Industrial Research Assistance Program (IRAP) to invest in some skilled people who could help them figure out better ways of working through production flow.
“And by better, it could be more cost-effective, it could be faster, it could be higher quality—any one of those things or all of them,” said Copp. “This funding allows you to work towards some project goals. It’s allowed us to streamline our operations in many different areas.”
Brunswick is pursuing a concept called “velocity manufacturing,” which is an approach to streamline operations based on the Theory of Constraints and work towards simplicity in operations.
“The IRAP program helped us learn new ways to be more efficient,” said Copp. “And those don’t have to be complicated, and they don’t have to be expensive or the latest tech. One of the easiest ways in our facility to simplify product flow and improve safety is the introduction of roller tables to move parts or raw materials from one place to another. So, for instance, we have rollers that move parts from one press brake to another along our line of Adira machines. We also have a roller system that feeds product from our bar picking area down a conveyor to our tube laser and loads material onto the tube laser without human intervention. The key is to add scale without adding labour.”
People Power
Copp sees the key to the company’s success as having the right mix of people, technology, and automation. Having the right people in the right seats makes a big difference because they are typically the ones who solve issues when the technology doesn’t fit the bill.
For instance, Brunswick has considered investing in sorting technology for its 2D laser cutting tables but hasn’t yet found any cost-effective options on the market. However, a machine designer on staff developed a pneumatic table with pins that rise up out of the table to help the team separate parts from a skeleton.
“It’s a faster, easier way to separate parts than pounding a mallet all day,” said Copp. “It makes the job more ergonomically friendly and speeds up the process. Having people with the mindset to see a problem and solve it is critical for growth.”
Copp considers people the key to the company’s growth over the past 52 years.
“Change like our new 32,000-sq.-ft. expansion isn’t possible without the right team around you,” he said. “It starts with hiring the right individuals, and that starts right at the top. You need the right leaders. I’ve been fortunate enough to surround myself with people who have skill sets in areas that I don’t, such as Adam Plouffe, our general manager. Adam has a strong understanding of Six Sigma and continuous improvement and has been instrumental in our success. The key is to hire good leaders, make sure that the team is aligned, and then allow them to make the decisions they need to make. Mistakes may be made, but everyone learns from that. It’s never about pointing blame; it’s about learning together. Our leaders share the same philosophy, and they pass the same message along to their team members, so everyone takes responsibility for their workcells. Bringing new people in who fit that culture has made us stronger year over year.
“We are extremely proud of how the company continues to grow, and I think our employees are very proud of that as well,” Copp continued. “It's hard to fathom that we've come as far as we have come, but we're so excited to go that next step. Because it's not a finish line, there's not a finite measurement of success. Our goal is to evolve through continuous improvement and build on what we're doing today for the future. And when you look at the investment that we've made now, it's really an investment in the future. We see so many great things within our staff and the opportunities that we have surrounding us, if we just continue to work on our customer service, the sky's the limit with what we can achieve here.”
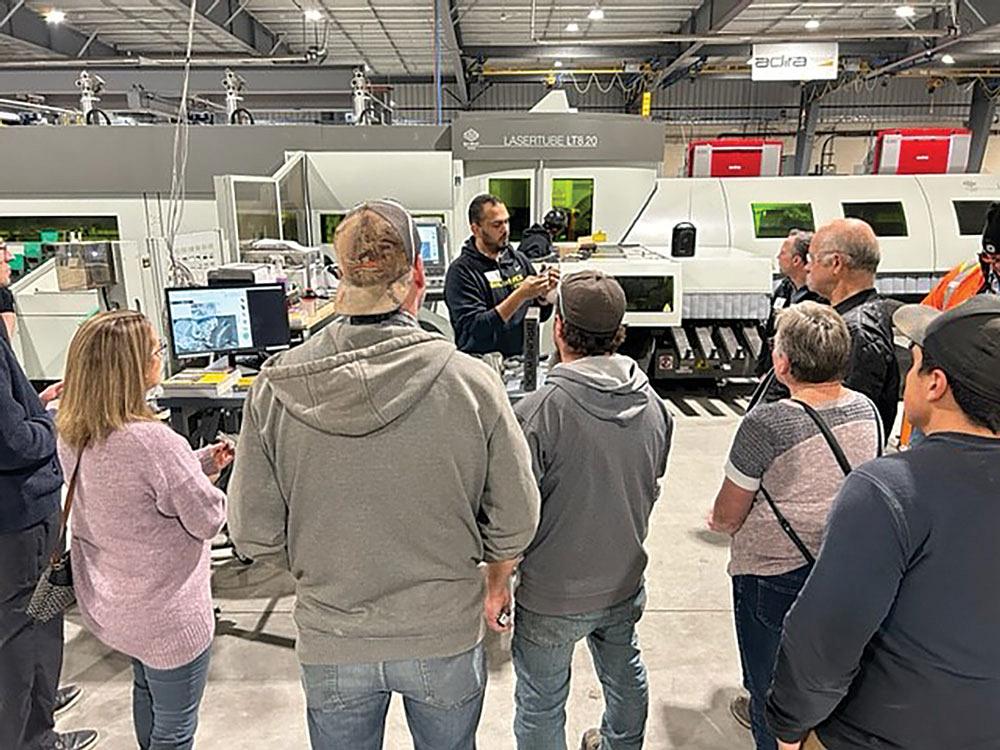
The grand opening of the facility expansion gave Brunswick the chance to introduce suppliers and customers to their new capabilities, which include laser tube cutting and a 12-kW flatbed laser.
Editor Robert Colman can be reached at rcolman@fmamfg.org.
Brunswick Steel, brunswicksteel.com
Giving Back to the Community
Being a community leader provides the opportunity to give back. That is certainly a philosophy that the team at Brunswick Steel believes in. For this reason, they established the Walter Copp Memorial Fund Bursary in 2022 honouring its founder’s legacy for years to come.
Brunswick offers four annual bursaries of $2,500 each to any current Brunswick employee or immediate family member who is enrolled in a post-secondary education program (including the trades). President Justin Copp and Vice-President Christine Dockter presented the 2023 awards to Catherine Ranopa and Lucas de Sousa.
Training Within Industry
People are the key to Brunswick Steel’s success, according to President Justin Copp. But given the challenging employment market, the company has focused its hiring on cultural fit rather than skill set. This necessitates a further investment in training, but Copp sees that as a worthwhile tradeoff in terms of employment longevity and long-term growth.
The company uses the Training Within Industry method for hands-on training, learning, and coaching for its team. The concept was developed in the 1940s to meet the high demand for wartime materials from a smaller and less experienced workforce, according to the TWI Institute.
“Steven Craig, our training and safety manager, facilitates training at our facility. Steven’s focus is to empower leaders at the supervisor and lead-hand levels. It would be naïve for us to think one employee alone could train every person and task in our facility, so we are pushing training responsibilities down to supervisors and lead hands as opposed to creating a one-size-fits-all training environment,” said Copp. “Our front-line people who are dealing with challenges daily are the ones who know how to improve things. As much as we revisit our approach regularly, this is at the heart of what we do.”
Copp believes the on-boarding process when hiring is key to making this approach run smoothly. Processes and machines can be learned, so the company looks for character and work ethic.
“It’s certainly not perfect, but part of continuous improvement is constantly looking at what is and isn’t working and adjusting it as necessary.”
About the Author
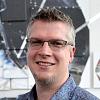
Rob Colman
1154 Warden Avenue
Toronto, M1R 0A1 Canada
905-235-0471
Robert Colman has worked as a writer and editor for more than 25 years, covering the needs of a variety of trades. He has been dedicated to the metalworking industry for the past 13 years, serving as editor for Metalworking Production & Purchasing (MP&P) and, since January 2016, the editor of Canadian Fabricating & Welding. He graduated with a B.A. degree from McGill University and a Master’s degree from UBC.
subscribe now
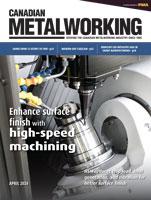
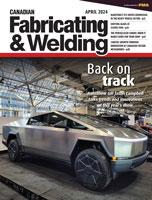
Keep up to date with the latest news, events, and technology for all things metal from our pair of monthly magazines written specifically for Canadian manufacturers!
Start Your Free Subscription- Trending Articles
Aluminum MIG welding wire upgraded with a proprietary and patented surface treatment technology
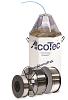
Achieving success with mechanized plasma cutting
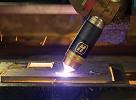
Hypertherm Associates partners with Rapyuta Robotics
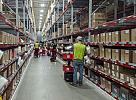
Gema welcomes controller

Brushless copper tubing cutter adjusts to ODs up to 2-1/8 in.
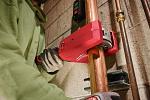
- Industry Events
MME Winnipeg
- April 30, 2024
- Winnipeg, ON Canada
CTMA Economic Uncertainty: Helping You Navigate Windsor Seminar
- April 30, 2024
- Windsor, ON Canada
CTMA Economic Uncertainty: Helping You Navigate Kitchener Seminar
- May 2, 2024
- Kitchener, ON Canada
Automate 2024
- May 6 - 9, 2024
- Chicago, IL
ANCA Open House
- May 7 - 8, 2024
- Wixom, MI