- FMA
- The Fabricator
- FABTECH
- Canadian Metalworking
Automation eliminates secondary operations at Systemair Bouctouche
Ventilation manufacturer’s automation approach keeps production up 24 hours a day
- October 25, 2023
- Article
- Fabricating
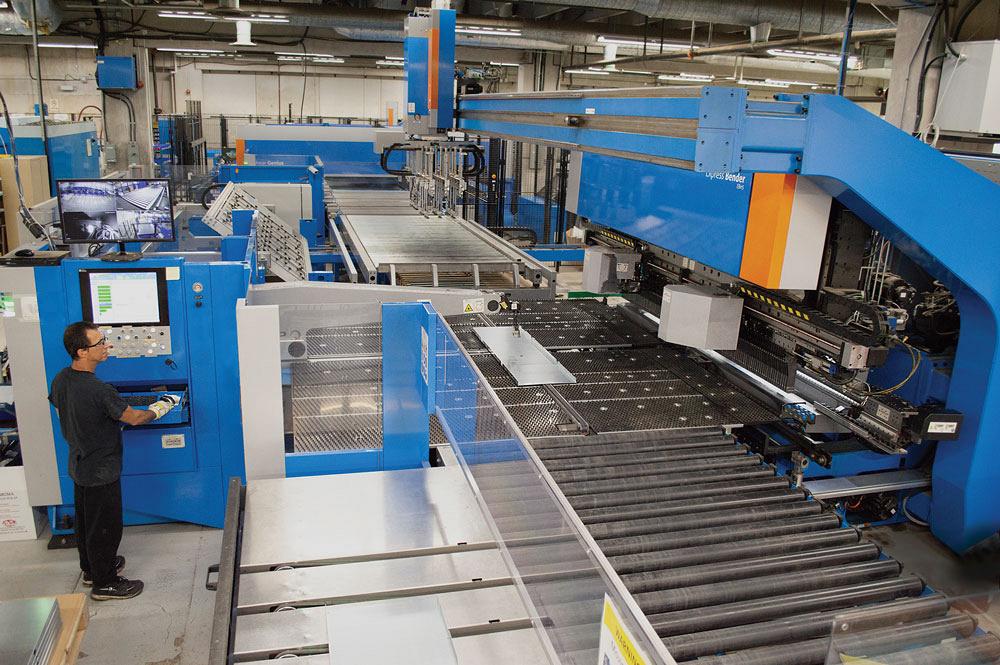
A part that used to require a 10- to 15-minute setup on a press brake now takes the company 30 seconds to set up on the servo-electric panel bender.
Systemair is a global supplier of ventilation, heating, and cooling products and systems. Headquartered in Sweden, the company has operations in 51 countries in Europe, North America, the Middle East, Asia, Australia, and Africa. The company has two factories in Canada: Tillsonburg, Ont., and Bouctouche, N.B. Its extensive product range is a key element in its success story.
Systemair Bouctouche has invested regularly in new equipment to keep it agile and to manage its production capacity needs. Most recently, this involved the purchase of automated cutting and forming and automated bending technology. Through the investment, the company has achieved faster turnaround times on parts and added capabilities previously unavailable to the shop.
“A strong demand for additional production capacity led the company to purchase a new Prima Power servo-electric Shear Genius and add an EBe automated bender in 2018,” said Ron Gallant, fabrication and maintenance manager at Systemair Bouctouche. “We also added Prima Power servo-electric press brakes in 2012, 2014, and two more this year.”
The international company’s relationship with Prima Power can be traced to 1994, when the first punching/shearing Shear Genius cell with automatic stacking was delivered to Systemair Denmark (previously Danvent A/S). Over the following years, close cooperation continued with new investments, machine transfers, service, and training. Today, Prima Power equipment can be found in many of the company’s 26 factories throughout 18 counties.
The New Brunswick facility purchased its first Shear Genius in 2007. Both Canadian facilities have identical Prima Power Shear Genius (SGe) cells and EBe automated benders.
Servo-Electric Cutting and Forming
With the Shear Genius system, the objective is to provide a machine capable of transforming a full-size sheet into finished parts. These parts can be moved to the final production stages for immediate integration directly into the final product assembly.
The Shear Genius (SGe) operates with minimal setup times and allows for lights-out operations. The system automates loading, punching, forming and upforming, unloading, sorting, and stacking.
“Because our parts are fairly square and rectangular, the Shear Genius is ideal for our product line,” explained Sylvie LeBlanc, production manager at Systemair Bouctouche. “We have different products that require many different tools, and having the three Multi-Tools and the auto-index stations allow us to produce a variety of different designs. From an engineering standpoint, we don’t feel limited. Today, we are challenging engineering a little bit more to increase our throughput.”
The SGe eliminates wasteful skeletons and costly secondary operations such as deburring. Nibble edges on the part exteriors are eliminated through the use of an integrated right-angle shear. In the SGe, the sheet is loaded and squared automatically, without human interference. The same clamps that hold the sheet for punching also hold it for shearing.
“The Shear Genius is a big advantage,” continued LeBlanc. “It has eliminated shaker parts and tabs by producing a finished part ready for stacking and bending without the need of secondary operations.”
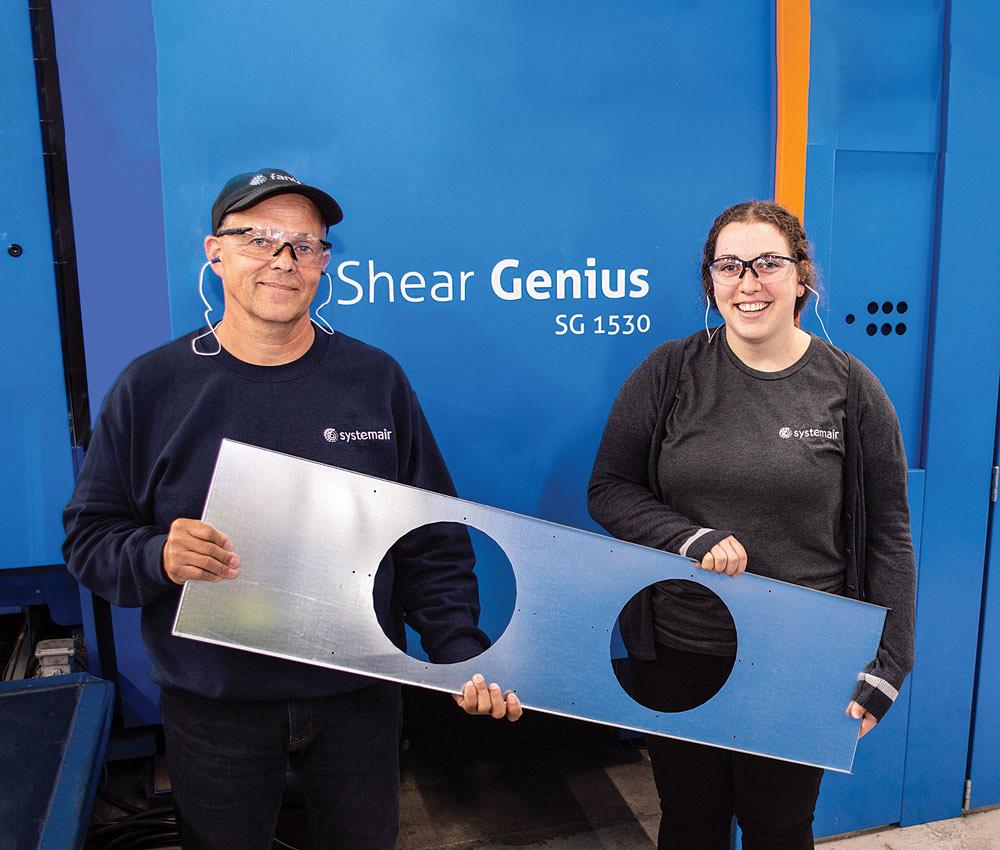
Ron Gallant, fabrication /maintenance manager (left) and Sylvie LeBlanc, production manager hold a part fabricated on the Shear Genius.
“And the Shear Genius allows us to run lights-out over the weekend and have parts ready for bending Monday morning,” added Gallant. “We also purchased a coil feeder in 2018 to load both Shear Genius cells. This saves us 15 to 20 per cent on our metal, not counting the labour and material handling savings.”
Express Bending
The servo-electric EBe Express Bender is a panel bender that is fully automated, from the loading of flat punched parts to unloading of the finished product. It offers precise control of bending axes, fast and smooth bending motion, programmability, and rigid construction that is resistant to variation in thermal conditions.
The panel bender increases production capacity due to its automated loading and unloading process. Systemair’s EBe is equipped with a picking and centring device (PCD) and a multifunctional table for the positioning and the centring of parts. The PCD-equipped panel bender with optional turning device provides increased automation when loading several stacks of different pieces, which allows batch or kit production and prepares the panel bender for future connection with other Prima Power machines.
“Today, a part takes 30 seconds to set up on the Express Bender that took 10-15 minutes on the press brake,” said Gallant. “And we achieve more consistent quality with the panel bender. It also allows us to do precision hemming on our doors.”
“We gained 50 per cent additional capacity with the Prima Power equipment purchased in 2018,” noted LeBlanc. “This purchase allowed us to grow 20 per cent per year over the past five years. We were able to double our production.”
Bright Future
Systemair Bouctouche’s 13,000-sq.-ft. facility has 220 employees and is running at full capacity.
“We are currently running at 24 hours per day with our current equipment,” concluded LeBlanc. “From a North American perspective, we have enjoyed a very good relationship with Prima Power. The Prima Power technology has allowed us to produce a lot more and grow as a company, but also from an employee standpoint, to work safely and more comfortably.”
Systemair, www.systemairbouctouche.ca
Prima Power, www.primapower.com
subscribe now
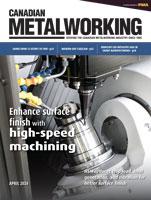
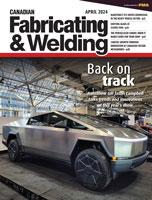
Keep up to date with the latest news, events, and technology for all things metal from our pair of monthly magazines written specifically for Canadian manufacturers!
Start Your Free Subscription- Trending Articles
Aluminum MIG welding wire upgraded with a proprietary and patented surface treatment technology
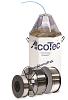
Achieving success with mechanized plasma cutting
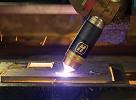
Hypertherm Associates partners with Rapyuta Robotics
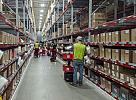
Gema welcomes controller

Brushless copper tubing cutter adjusts to ODs up to 2-1/8 in.
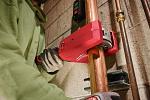
- Industry Events
MME Winnipeg
- April 30, 2024
- Winnipeg, ON Canada
CTMA Economic Uncertainty: Helping You Navigate Windsor Seminar
- April 30, 2024
- Windsor, ON Canada
CTMA Economic Uncertainty: Helping You Navigate Kitchener Seminar
- May 2, 2024
- Kitchener, ON Canada
Automate 2024
- May 6 - 9, 2024
- Chicago, IL
ANCA Open House
- May 7 - 8, 2024
- Wixom, MI