product manager for tooling and magnetic drills
- FMA
- The Fabricator
- FABTECH
- Canadian Metalworking
How to create clean holes in curved surfaces
A look at power tools, accessories, and getting started
- By William Furt
- October 20, 2023
- Article
- Fabricating
It is not uncommon for metal fabricators to take on a project that requires making a hole. Drilling and cutting holes into surfaces becomes more complicated when the surface is no longer a flat sheet. Creating a hole in curved surfaces, like pipes or tubes, can be a challenge, but there are some great tools available and best practices to follow to ensure that the holes are clean and burr free.
Choosing the Right Power Tool
Hand Drills. These tools are the best option for fabricators working on non-magnetic materials such as plastics, composites, aluminum, and some stainless steels. They are also portable, which allows for more versatility.
However, one of the main challenges with hand drills is that drill bits can easily wobble or slide out of the intended drilling spot, especially on piping or curved surfaces. That is why it’s a lot more common to break tools or have accidents.
Because of this, it is important to ensure you set up and clamp your workpiece appropriately when using a hand drill. However, it’s important to understand that this extra step makes hand drilling a much longer process, especially compared to faster and more precise options that are available for most applications.
Plasma Cutters. Most people don’t think about using a plasma cutter when it comes to creating holes. This option allows fabricators to cut material up to 1.5 in. thick quickly.
However, it is very difficult to create a perfectly round hole. Furthermore, plasma-cut holes often need additional cleaning and deburring to meet industry standards. This cutting option can work for some holes and applications, but for those needing a round, clean hole, other options are better suited.
Magnetic Drills. For precise, perfectly round holes, mag drills are the way to go. These tools are a fast and portable option for making clean holes in a variety of materials in diameters of ½ in. to 4 in.
A mag drill is essentially a portable drill press, meaning that it is robust enough to make holes on thick and tough materials, yet lightweight enough to be carried wherever you need it, making it a highly versatile tool.
It is important to note that mag drills, as the name indicates, rely on magnets to safely affix the drill to the workpiece, and therefore require a ferrous or magnetic the workpiece.
Drill Presses. A drill press is a good option for more aggressive or challenging applications that go beyond the capabilities of both a hand drill and a mag drill.
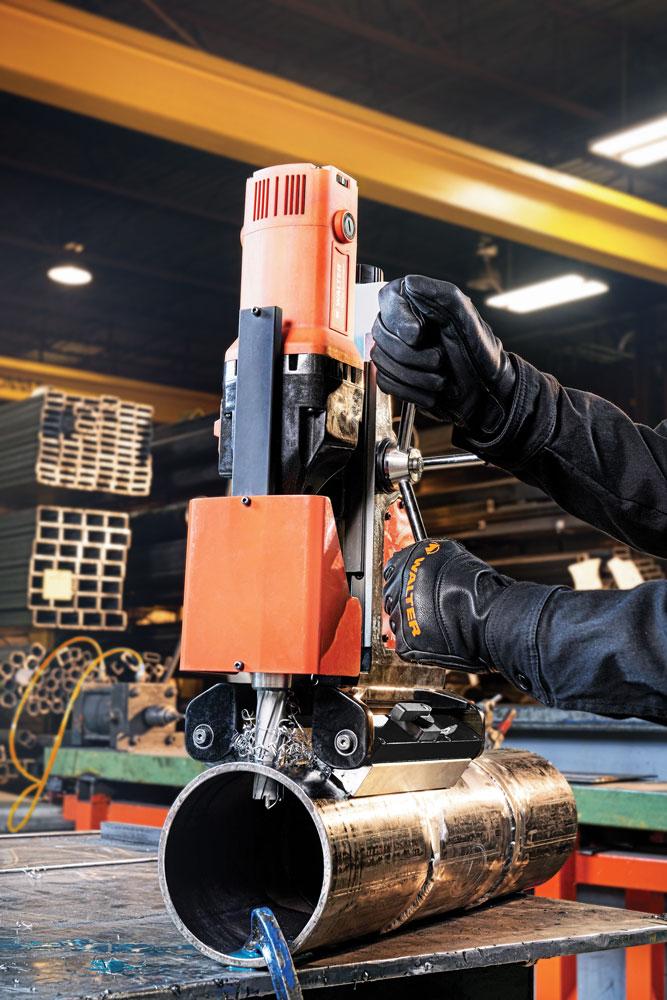
Mag drills are a fast and portable tool for making clean holes in a variety of materials in diameters from ½ in. to 4 in.
If you are working with extremely hard materials, seeking large-diameter or very deep holes, it is best to use a high-performance tool like a drill press.
The obvious downside to this tool is that it is expensive and sits in a fixed location.
Power Tool Options and Accessories
The diameter of the hole will dictate the type of consumable to use. For any diameter less than ½ in., a drill bit is a good choice. However, for drilling holes with diameters larger than ½ in., an annular cutter is recommended.
The setup is particularly important with a drill bit because it involves a single point touching another single point on the round surface, meaning that it could easily slip. Ensuring that the workpiece or mag drill is properly secured to prevent slippage is essential for good hole production and overall safety and tool longevity.
An annular cutter tends to drill a lot faster than other tools. Unlike the drill bit that cuts the hole out of the material, the annular cutter cuts a ring around the surface, creating a slug that pops out. This tool is ideal for hole diameters of more than 2.5 in.
The challenge with using an annular cutter on a curved surface is that the cutter does not lie flat, meaning that not all the teeth are engaged with the surface at the same time. This is called intermittent cutting and it happens at both the beginning and end of the cut.
Because of this, a carbide-tipped annular cutter is recommended. This tool is more robust than a typical steel version and is less likely to break during intermittent cuts.
Pilot pins always are recommended with annular cutters to clearly identify where the cutter should be located on the curved surface to ensure the drilling occurs in the correct spot. The pilot pin also serves as a method of ejecting the slug from the cutter and opening the internally fed coolant valve for direct lubrication and cooling of the cutter and workpiece.
Getting Started With Curved Surfaces
The setup is so important when it comes to drilling, especially on curved surfaces, and particularly with pipes.
If you are using a vice when drilling into a small tube, understand that it will not be as rigid as it needs to be—the jaws will be flat and will not grip the curved surface as well as they would a flat surface. The workpiece can therefore move around and turn easily. This is why choosing a workholding system designed for pipes or curved materials is a good starting point.
If the pipe is small enough, a V-block can ensure that it is clamped properly.
For 3-in.-dia. pipes, rather than clamping the workpiece itself, it is best to use a specialized magnetic drill with curved magnets that attach onto the workpiece instead. These types of drills will securely attach to both flat and curved workpieces securely thanks to magnets that rotate. This allows for an easier, faster, and safer application that delivers a clean hole every time.
Creating Clean, Burr-free Holes
Once the workpiece has been secured, the next important step is lubrication. This is one of the most important factors affecting drilling outcomes. When working with metals, you always should use a lubricant.
Operators in a rush sometimes skip this step to save time or eliminate potential cleanup. However, several lubrication options are available that are more manageable and easier to clean up. For example, a stick lubricant applied to the cutter will melt just enough to provide adequate lubrication as the drill heats up. This is a quick and easy option to ensure the tool is lubricated without any mess.
The more that you use lubricant, the cooler your cut and the smoother the chips. One of the common problems when drilling into pipes with an annular cutter, because of intermittent cutting, is that the slug is not always perfectly flat and can sometimes get stuck in the cutter. Using lots of lubricant will help address this.
Also, it’s essential to adapt RPM and feed rates to the application. It’s always a good practice to start off slow and apply a little bit more pressure toward the end so that you can pop the slug out faster and with more ease.
The feel of the drilling process also is a good indication of cut quality and process ease. Operators can modify the feed rate based on this feel, which encompasses pressure and vibration as well as visual and audio cues from the drill. If the cutter is making too much noise or is vibrating too much, adjust the speed to get the drill back on track and working correctly.
For deburring holes on curved surfaces and cleaning the edges, a countersink is the best tool. This tool makes it very easy to clean centered holes. The advantage of using a countersink with a mag drill is that you don’t have to demagnetize the drill after cutting. Instead, you just remove the drill bit or annular cutter and replace it with the right-sized countersink then go into the hole with the tool, so it is already located exactly where it needs to be.
Choosing the right tool for the job and setting up the process properly are essential for producing high-quality, burr-free holes in curved surfaces. But lubrication and proper speeds and feeds will make the process all that much faster and easier.
William Furt is product manager for tooling and magnetic drills for Walter Surface Technologies, 5977 Trans-Canada Hwy, Pointe-Claire, Que. H9R 1C1, www.walter.com.
About the Author
subscribe now
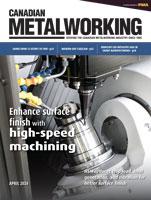
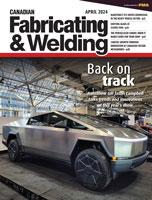
Keep up to date with the latest news, events, and technology for all things metal from our pair of monthly magazines written specifically for Canadian manufacturers!
Start Your Free Subscription- Trending Articles
Aluminum MIG welding wire upgraded with a proprietary and patented surface treatment technology
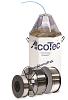
Achieving success with mechanized plasma cutting
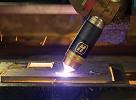
Hypertherm Associates partners with Rapyuta Robotics
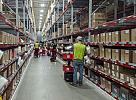
Gema welcomes controller

Brushless copper tubing cutter adjusts to ODs up to 2-1/8 in.
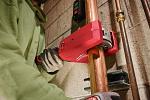
- Industry Events
MME Winnipeg
- April 30, 2024
- Winnipeg, ON Canada
CTMA Economic Uncertainty: Helping You Navigate Windsor Seminar
- April 30, 2024
- Windsor, ON Canada
CTMA Economic Uncertainty: Helping You Navigate Kitchener Seminar
- May 2, 2024
- Kitchener, ON Canada
Automate 2024
- May 6 - 9, 2024
- Chicago, IL
ANCA Open House
- May 7 - 8, 2024
- Wixom, MI