Editor
- FMA
- The Fabricator
- FABTECH
- Canadian Metalworking
Keeping cool under production pressures at MTL Cool
Chambly, Que. company leans out fab processes to keep products and prototypes flowing
- By Rob Colman
- April 27, 2022
- Article
- Fabricating
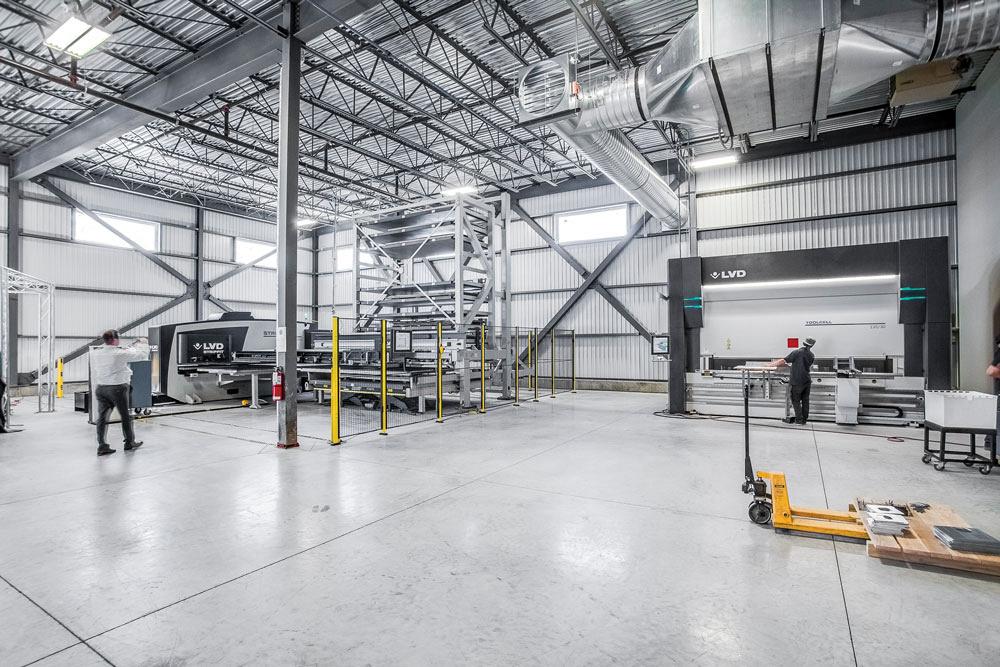
When MTL Cool decided to take on its own fabricating, the company wanted to ensure the equipment it purchased allowed for flexibility and efficiency. All photos courtesy MTL Cool
Simplifying production processes is key to speeding up production. When production involves a variety of parts and custom products, maintaining flexibility in those processes is also critical. When commercial refrigerator manufacturer MTL Cool planned its shift to fabricating metal parts in-house, this is what it had in mind from the start. To achieve these goals of simplification and flexibility, the company invested in a punch press with a tower for loading/unloading parts, a press brake with automated tool loading/unloading, and a flexible paint booth setup.
Family History, Changing Industry
MTL Cool is a Chambly, Que.-based, family-run manufacturer founded in 1997 that specializes in point-of-purchase refrigerated displays.
The family has a long history of working in refrigeration. Founder Mark Bedard began working with his father in a small garage in downtown Montreal repairing residential and commercial air conditioning units. Once his father retired, Mark took over the business and started pointing it in a new direction. In the late ‘90s, the company was asked to design a specialty refrigerated display that could accommodate a range of different products. It was that one custom request that kickstarted MTL Cool. The company’s client list has since included brands such as General Mills, Danone, and Kraft Heinz.
The company has been based in Chambly since 2006 and opened an expanded 50,000-sq.-ft. facility there in 2017 to take control of its manufacturing processes. Mark’s son Thomas has since joined the management of the company—the fourth generation of family to be involved in the refrigeration business.
“We’ve been through a few changes in terms of products since MTL Cool was created in 1997,” said Thomas Bedard, vice-president of production. “We were producing industrial chillers and heat pumps for a while. That was all tubing work. There was nothing major on the fab side to do, so we were primarily assembling the chiller. But in 2014 and 2015 we started importing a lot of material to build point-of-purchase refrigerators, and that supply chain can be unreliable, so we decided to make the shift and manufacture most of the materials ourselves.”
MTL Cool has always run on a philosophy of keeping operations as streamlined as possible. The team took that philosophy into its decision-making process for choosing its manufacturing machinery.
“We jumped head-first into the deep end with manufacturing,” said Bedard. “And it has paid off. We now import less than 10 per cent of the material we use in production.”
The company now also has a second assembly plant in Plattsburgh, N.Y.; all parts used for assembly south of the border are supplied by the Chambly facility.
Streamlined Fabrication
MTL Cool works in cold-rolled steel, galvanized, and some aluminum; the thickest sheet it uses is 10 ga. With the variety of secondary features required in many refrigeration units, a punch press was a natural fit for its fabrication shop.
The shop invested in an LVD Strippit PX-1530 punch press, which allows it to punch, bend, tap, and form parts. Its tool changer design features all-tool rotation—each tool can rotate a full 360 degrees. It has a capacity of up to 200 tools and the ability to form flanges up to 75 mm high. The punch is equipped with a tower that can facilitate lights-out operation. MTL uses primarily Mate tooling on the machine.
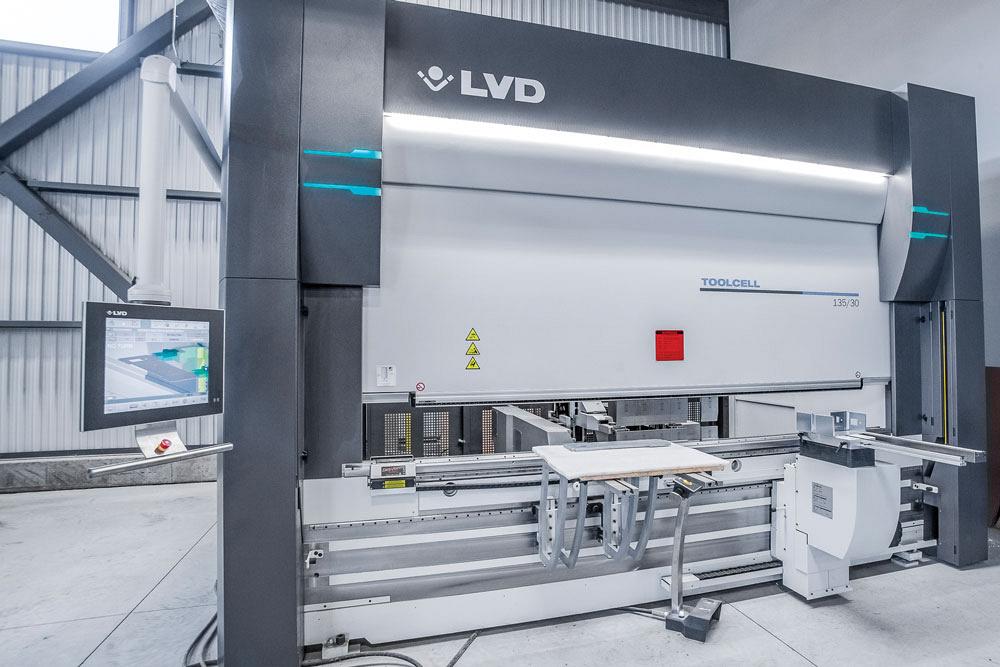
Both the punch press and press brake with automated tool changing are programmed offline to keep production and prototyping fab work moving on both shifts.
“Our design team has been able to come up with some really interesting features that I hadn’t seen before in other refrigeration units using the punch press paired with the tooling we have invested in,” said Bedard.
The company also wanted to ensure that any press brake work could easy adapt to order changes without concerns about tooling management. To address that potential bottleneck, it equipped itself with an LVD Toolcell 135/30 (135 tons by 3,060 mm). This press brake holds all its tools within the footprint of the machine. It is set up for a library of tools, including two complete lengths of self-seating punches and five complete lengths of vee dies. All of the tool loading/unloading is automated, and it is equipped with the company’s Easy-Form Laser, which monitors the angle of the bend in real time to provide instant feedback to the controller, essentially ensuring that each part is formed to the correct angle.
The metal fab department is managed by three team members during the day. All programming for both machines is done offline in the office using LVD’s CADMAN software. At night a two-man crew keeps both machines going. This is the only area at the facility that runs two shifts.
The flexibility of the shop is enhanced by its Gema powder coating machine, which includes both automatic and manual cabs to adjust to the needs of a job on the fly. The powder coating machine also has six FMP conveyor systems with five cleaning, drying, and baking steps. The paint department is a team of three employees.
In addition, the company has its own foam injection machinery, such that it can be self-sufficient in terms of building panels for its refrigerators. The company has about 40 employees in Chambly. With the investment in advanced machinery at the front end of production, more resources can be focused on assembly, both in Chambly and in Plattsburgh (shipments to the U.S. facility run every day or two).
Shifting Shop Needs
Since the company first invested in its fab shop equipment, business has increased such that it has had to change its approach in the fab department.
“Ideally we would purchase more equipment, but we don’t have the square footage available for that,” said Bedard. “Instead, we are subbing out our higher volume, cheaper parts and keeping our fab department focused on complicated, critical parts and prototyping.”
The flexibility of its automated machines means that running high-mix, low-volume parts is relatively straightforward for MTL Cool.
“We used to have subcontractors doing our prototype parts, but it slowed down our design process,” said Bedard. “Now, if we know we will be cutting parts for production on a certain gauge on a certain day, we will include prototype items on those nests. Having that flexibility is a real benefit because prototyping new products takes a great deal of time, rework, and tweaking to get it just right for customers. We can turn these designs around quite a bit faster with the approach we take because of the speed we achieve in cutting and bending on the shop floor.”
This flexibility is ultimately helping the company grow.
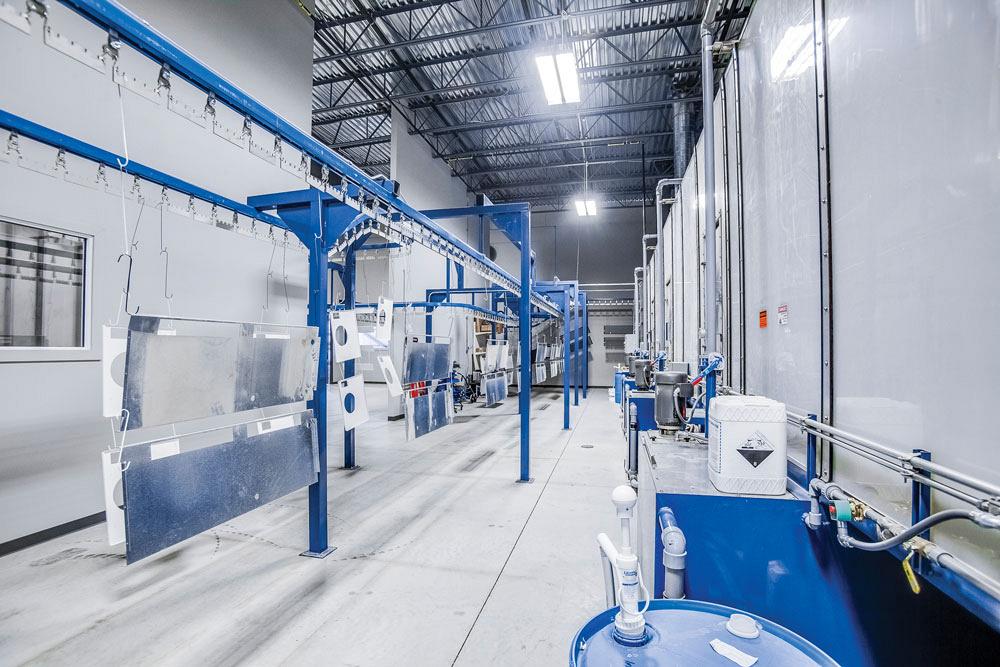
The shop's powder coating setup also is designed for efficiency. Three employees staff the department over one shift.
“Since MTL Cool began to market and sell our own products made in Canada and the USA, the growth trajectory has been very strong,” said Bedard. “We are making significant strides with major retailers in the grocery industry and look to continue to bring needed, innovative, and quality products to the market. We continue to implement actions to increase the use of our existing facilities and are looking at strategic plans to take it to the next level.”
Editor Robert Colman can be reached at rcolman@canadianfabweld.com.
MTL Cool, www.mtlcool.com
LVD Group, www.lvdgroup.com
About the Author
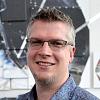
Rob Colman
1154 Warden Avenue
Toronto, M1R 0A1 Canada
905-235-0471
Robert Colman has worked as a writer and editor for more than 25 years, covering the needs of a variety of trades. He has been dedicated to the metalworking industry for the past 13 years, serving as editor for Metalworking Production & Purchasing (MP&P) and, since January 2016, the editor of Canadian Fabricating & Welding. He graduated with a B.A. degree from McGill University and a Master’s degree from UBC.
subscribe now
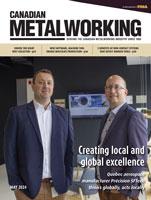
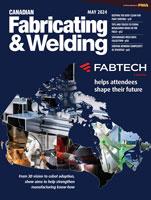
Keep up to date with the latest news, events, and technology for all things metal from our pair of monthly magazines written specifically for Canadian manufacturers!
Start Your Free Subscription- Trending Articles
Aluminum MIG welding wire upgraded with a proprietary and patented surface treatment technology
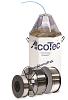
HGG Profiling Equipment BV names Western Canada area sales manager
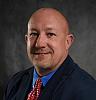
Protected and productive: welding helmet tech
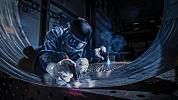
Automotive industry gets back on track
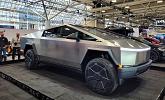
Gas mixer delivers precise mixture adjustments quickly for laser welding
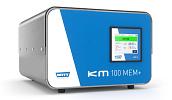
- Industry Events
Automate 2024
- May 6 - 9, 2024
- Chicago, IL
ANCA Open House
- May 7 - 8, 2024
- Wixom, MI
17th annual Joint Open House
- May 8 - 9, 2024
- Oakville and Mississauga, ON Canada
MME Saskatoon
- May 28, 2024
- Saskatoon, SK Canada
CME's Health & Safety Symposium for Manufacturers
- May 29, 2024
- Mississauga, ON Canada