- FMA
- The Fabricator
- FABTECH
- Canadian Metalworking
Machine a Smooth, Consistent Pipe Bevel
Location really doesn’t matter
- By Sue Roberts
- August 23, 2016
- Article
- Fabricating
A good weld on a thick stainless pipe starts with a consistent, smooth beveled surface. Knowing that the joint requires the optimal number of passes with no variation saves time for the welder.
Creating the angled surface around the circumference of the pipe traditionally requires grinding that can be time-consuming or plasma cutting that can mean spending time moving the pipe to a plasma cutting station. Both processes rely on the experience of the operator to achieve the desired bevel angle, land area, and surface finish. Both processes introduce heat into the pipe.
Machining bevels can result in the precise angle and surface finish that comply with welding specifications, and in many instances, it can be done without repositioning the pipe.
Bevel in One Pass
“Our units are designed to cut bevels in incremental angles using interchangeable cutting heads for 30, 37.5, or 45 degrees. Pipe that is 4 inches in diameter or larger and up to ½-in, thick and plate up to ½ in. thick can be bevelled in one pass,” said Larry Feskanich, senior global marketing manager at RIDGID®. “A 10-in., schedule 40 pipe can be bevelled in about 45 seconds.”
Feskanich was referring to the recently introduced B-500 Transportable Pipe Beveller that uses a conical cutter head that holds six inserts.
An operator-controlled hand crank manually rotates the cutter head around the circumference of the pipe or along the plate’s edge. Two red, two yellow, and two green LED lights help the operator maintain the optimum speed to achieve a smooth finish and extend insert life. Green lights indicate an ideal speed; yellow means more speed is needed; red means slow down.
Ready for Welding
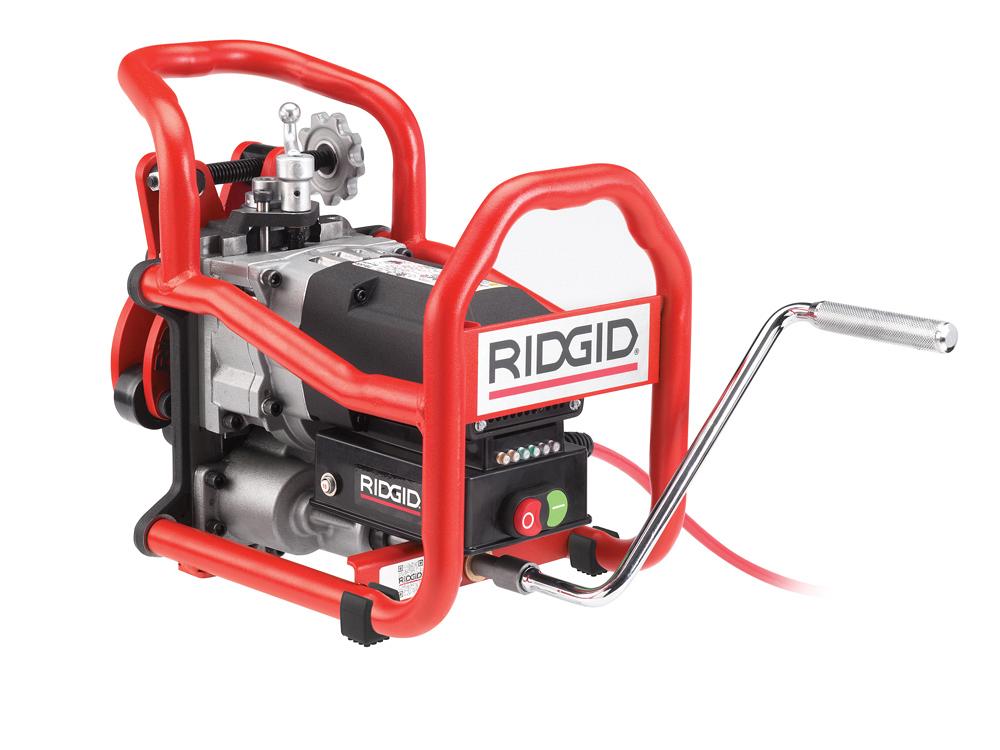
A series of LED lights above the on/off switches help operators maintain the proper speed when turning the crank that moves the cutting head to ensure a smooth bevel and long insert life.
“It is a cold cutting process, so once you are done with the bevel, the pipe or plate is cool,” Feskanich said. “Any heat that is created during the process is directed away from the material and into the chips, which are larger than those created during grinding. Since no heat is introduced into the material, it can go directly to welding. You don’t need to worry about cooling heated material after machining the bevel or perform any cleanup of the end.”
A seven-position gauge controls the depth of the bevel on the material edge. The edge can have anywhere from a zero land, the uncut area toward the inner wall of the pipe, up to a 3/16-in. land to prevent welding blow-through.
The 52-lb. beveller clamps onto a pipe or a plate, gripping the material between guide rolls and drive rolls. It can move along the edge of a fixed workpiece or be mounted on an adapter to machine a rotating pipe.
Go to the Pipe
“It can be moved around a job site,” said Feskanich. “Its compact dimensions—16 in. long by 11-1/2 in. wide by 13-3/8 in. tall—let it fit into some close areas. Since it doesn’t need acetylene gas to function, you don’t need to worry about hoses reaching the work area.”
The beveller was designed to be easy to use in a variety of settings. “We’re seeing these units being used a lot on-site in shipyards, in fabricating shops, and in mechanical contracting applications,” Feskanich said. “If you can cut a pipe relatively square, you can machine a bevel on it.”
Associate Editor Sue Roberts can be reached at sroberts@canadianfabweld.com.
Photos courtesy of RIDGID Inc.
RIDGID, 888-743-4333, www.ridgid.com.
About the Author
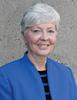
Sue Roberts
2135 Point Blvd
Elgin, IL 60123
815-227-8241
Sue Roberts, associate editor, contributes to both Canadian Metalworking and Canadian Fabricating & Welding. A metalworking industry veteran, she has contributed to marketing communications efforts and written B2B articles for the metal forming and fabricating, agriculture, food, financial, and regional tourism industries.
Roberts is a Northern Illinois University journalism graduate.
subscribe now
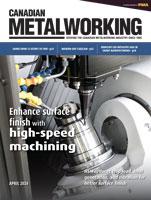
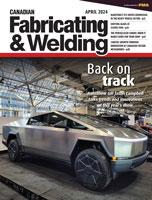
Keep up to date with the latest news, events, and technology for all things metal from our pair of monthly magazines written specifically for Canadian manufacturers!
Start Your Free Subscription- Trending Articles
Aluminum MIG welding wire upgraded with a proprietary and patented surface treatment technology
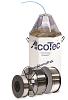
Achieving success with mechanized plasma cutting
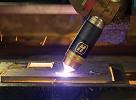
Hypertherm Associates partners with Rapyuta Robotics
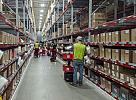
Gema welcomes controller

Brushless copper tubing cutter adjusts to ODs up to 2-1/8 in.
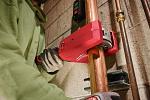
- Industry Events
MME Winnipeg
- April 30, 2024
- Winnipeg, ON Canada
CTMA Economic Uncertainty: Helping You Navigate Windsor Seminar
- April 30, 2024
- Windsor, ON Canada
CTMA Economic Uncertainty: Helping You Navigate Kitchener Seminar
- May 2, 2024
- Kitchener, ON Canada
Automate 2024
- May 6 - 9, 2024
- Chicago, IL
ANCA Open House
- May 7 - 8, 2024
- Wixom, MI