Lead Engineer
- FMA
- The Fabricator
- FABTECH
- Canadian Metalworking
Maximizing laser cutting performance
Top preventive maintenance tips to keep your laser cutting machine performing
- By Tom Eldin
- December 22, 2023
- Article
- Fabricating
Regular equipment maintenance helps identify and address potential issues before they escalate, thus extending the overall lifespan of that equipment. Addressing minor problems during routine maintenance is a more cost-effective approach than waiting for major issues to develop that can lead to costly repairs.
Understanding your laser is key to making sure it continues to perform at its peak. Regular maintenance helps maintain the precision and accuracy of your cuts, which is crucial for industries that require tight tolerances and consistent quality. Well-maintained equipment also operates more efficiently, which can lead to energy savings and reduced operating costs.
Ultimately, preventive maintenance also ensures that a shop runs to plan, meaning that it can maintain production schedules and resource allocation.
Key machine components within a laser cutting machine require particular attention. Many machine tool suppliers will specify when certain maintenance processes should be performed.
The basic components of a laser cutting table are the physical machine tool itself, the laser source, the chiller, pallet changer, and dust collector. Each component requires careful consideration when it comes to maintenance.
The Machine Tool
When I refer to the machine tool here, I am referring to the various mechanical parts that are required to running the machine, not including the laser source itself. This includes the need to lubricate the rack and pinion X, Y, and Z axes, and the guide rails. Your machine tool supplier likely suggests a lubrication maintenance schedule based on the amount itis used. Be sure to check this carefully.
The axis limits of a machine will change over time with wear and tear and can cause program functionality problems. Review these axis limits regularly to ensure you are still in spec.
Make regular visual checks on the bellows for your rack and pinion system to ensure there is no chance of dirt penetrating this. Make similar checks to water connections to look for cracks and kinks.
Change cooling water filters per the manufacturer’s instruction (usually annually), as do gas filters for the laser.
Be sure to install a 0.01-µm filter in the nitrogen supply line to safeguard the laser system from potential contaminants. Lasers have compressed air intake which can carry dust, dirt, oil, and moisture. Without minimum yearly machine filter changes, these contaminants can enter the machine’s internal components. This will cause wear, corrosion, and reduced efficiency
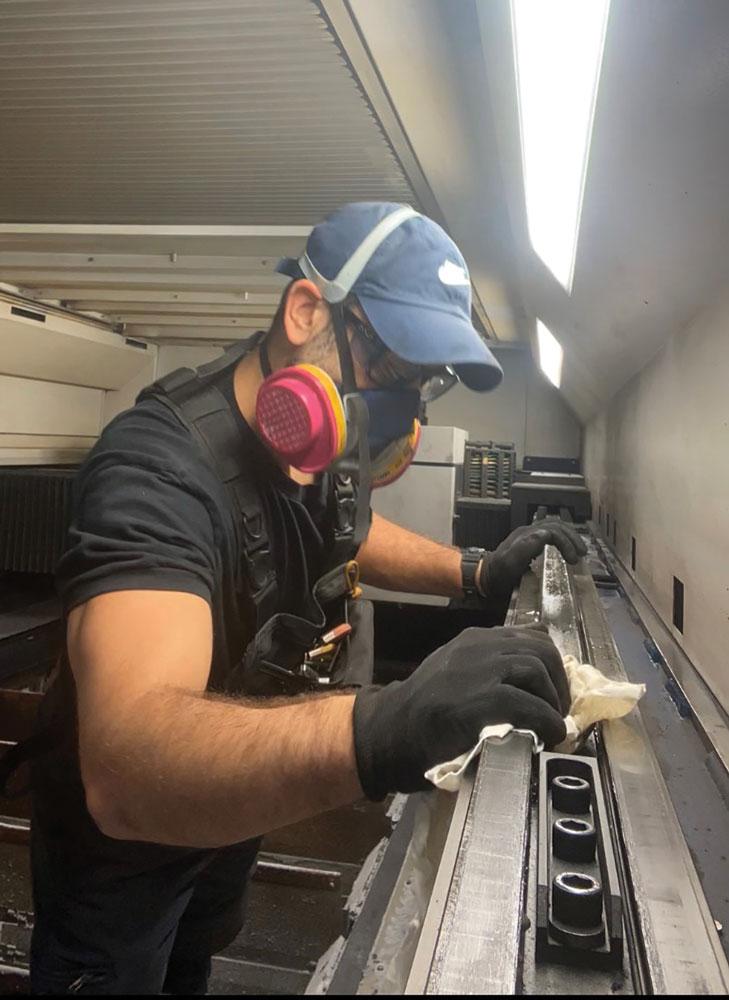
Preventive maintenance ensures that a shop runs to plan, meaning that it can maintain production schedules and resource allocation. Here a technician is seen cleaning and lubricating linear guide rails. Laser Service Solution
Other key safety points to tackle include checking emergency stops, reset, and pause buttons to ensure they are working properly. Also, perform a visual inspection of warning lamps as well.
For eye safety, check the protective windows on a fibre laser and all possible points of egress for light from the cutting area. To do this, use a flashlight in a dark room and run it around all possible egress points.
The Laser
The laser itself is probably the least likely part to be overlooked for inspection, but it’s worth reviewing the essential points that need to be checked.
The nitrogen input to a fibre laser is key. If this is compromised, it will affect kerf and cleanliness of your cut. Having new or maintained gas regulators will ensure that the correct pressure is being delivered. Gas leaks often occur with old regulators, which can be costly. Check the lateral air blast nozzle for cleanliness, ensuring it’s not plugged with spatter. Cutting issues could result if the nozzle isn’t checked.
Cleaning the nozzle changer regularly and checking the alignment of the head to the nozzles when changing is important. Make sure the calibration plate is kept clean as well.
Performing a visual inspection of the laser while it is running can also be helpful to capture any issues.
Lastly, remember to have your service engineer check internal fans for cleanliness. Improper airflow can hamper all other components if compromised enough.
The Pallet Changer
The pallet changer is just as important as any other part of the machine in keeping it running smoothly. There are several items that need to be reviewed regularly.
First, check the lateral guideways and readjust them, if necessary. Guideways are the area where the pallet wheels are guided into the pallet changer. It’s important to make sure no scrap is in there. Any hindrance could cause the wheels to jump the track, causing all kinds of problems.
Check the oil level and the rest of the hydraulic system to ensure there are no leaks. Also be sure to check how often the hydraulic oil requires changing. Depending on the manufacturer, this could be required every three to five years. Be sure to bring the table down first before changing the oil.
Check the motor chains to see that they are securely attached and lubricate as necessary. The chain deflection will be specified by your machine’s maintenance manual.
Check the wheels on the pallet changer for chips; after installations, there can be a settling of the machine which can cause misalignment of the pallet with the machine tool. This can wear the wheels prematurely. A good preventive maintenance practice is to check and realign or level beds to ensure smooth operations.
Measure the step between A/B pallet rails and the processing machine and check that they are within the tolerance value. If there is no step but there is an abnormal sound, look under the table to see if there is any obstacle or damaged section on the wheel.
Dust collector maintenance mainly involves keeping up with filter change schedules and regularly checking the dust bin and emptying it as often as necessary. Consider replacing filters instead of cleaning them, because they are very carcinogenic. There are gauges on the dust collector that will let you know if it is clogged.
Check suction hose attachments regularly for leaks.
Chille
rWater conductivity is important for fibre laser systems because it directly affects the performance of the laser. Fibre laser systems, like many other types of lasers, generate a significant amount of heat during operation. This heat needs to be efficiently dissipated to maintain stable and reliable laser performance.
Respecting factory water conductivity can reduce corrosion of metal parts which can degrade performance of the laser system.
Factory manuals generally recommend water and filter changes every six to 12. Some machine tool builders recommend regular water, while some use deionized or distilled water, and yet others recommend additives. Refer to your factory-supplied manual for both water and filter change guidance.
Cleaning condenser fins and replacing external filter matts will ensure that the laser is getting sufficient air to cool the water. This is critical also during summer months. Fluctuations in temperature can cause variations in laser output power and beam quality. Correct cooling water helps maintain stable operating temperature, ensuring a predictable laser performance.
CO2 Laser Maintenance
Although fibre lasers are the common choice when companies purchase laser cutting tables today, there are still many CO2 workhorses out in the field that require special attention.
One of the benefits of fibre lasers is that the need to maintain mirrors is removed. Bend mirrors on CO2 lasers, for instance, need to be cleaned or replaced once a year. Upward facing mirrors have a tendency to become dirty quickly due to gravity, so these also require special attention.
Bend mirror alignment and mode checks are key, but these are usually performed by factory trained service specialists. Check with your supplier to make sure you are on a necessary schedule for this.
Replace and align the internal resonator mirror based on hours of use. These requirements vary widely depending on what machine you are using and can range anywhere between 4,000 and 20,000 hours of use. Check with your machine tool supplier.
The cutting head’s processing lens needs to be cleaned and checked for thermal distortion, and replaced when spattered or scratched, since this can cause the lens to shatter. Never handle a shattered lens. Instead, call a trained laser engineer to clean the system for you. Check the head for looseness by pushing and pull it by hand.
Conducting regular focus checks will help keep the laser cutting precisely. Also check the nozzle center adjustment screws for proper movement because they can wear over time.
Looking for gas leaks is important on an older machine as well, in the lines and at the cutting head.
Water lines similarly can rot internally from years of acidity on older lasers, so it is important to check the flexibility of these hoses and change one at a time when an issue arises.
Maintenance Schedules
The frequency of maintenance checks will vary depending on the nature of the check, your cutting volume, and material your shop is cutting.
Generally speaking, you should perform a quick and simple cleaning and visual inspection daily to ensure optimal performance. For instance, keeping lenses clean and the nozzle clear of debris are daily concerns.
Weekly and monthly checks include cleaning optical components. It is also important to check coolant levels and hoses and cables on chiller components to ensure proper circulation.
Annual or periodic maintenance includes a detailed check of your laser source and any electrical connections, switches, and control panels.
It’s useful to check with your machine tool supplier for detailed preventive maintenance advice. Having a checklist of what should be checked and when is a useful tool to have in your shop to ensure that equipment is maintained at proper intervals.
Be sure to contact a qualified technician to perform complex repairs or when major malfunctions occur.
It’s easy to believe that as long as your laser is cutting cleanly, there is no way that a critical failure is possible. But without properly maintaining the laser head, the machine tool’s mechanical components, the pallet changer, and the dust collector, a failure could be closer than you think.
No one can afford downtime in this environment of just-in-time delivery of components. Make sure your laser keeps you as productive as possible by giving it the attention it requires.
Tom Eldin is lead engineer at Laser Service Solution, Etobicoke, Ont., 647-618-3212, tom@laserservicesolution.com, laserservicesolution.com.
subscribe now
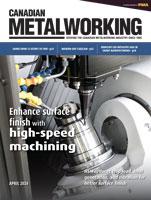
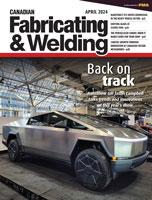
Keep up to date with the latest news, events, and technology for all things metal from our pair of monthly magazines written specifically for Canadian manufacturers!
Start Your Free Subscription- Trending Articles
Aluminum MIG welding wire upgraded with a proprietary and patented surface treatment technology
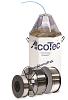
Achieving success with mechanized plasma cutting
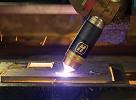
Hypertherm Associates partners with Rapyuta Robotics
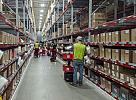
Gema welcomes controller

Brushless copper tubing cutter adjusts to ODs up to 2-1/8 in.
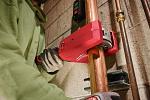
- Industry Events
MME Winnipeg
- April 30, 2024
- Winnipeg, ON Canada
CTMA Economic Uncertainty: Helping You Navigate Windsor Seminar
- April 30, 2024
- Windsor, ON Canada
CTMA Economic Uncertainty: Helping You Navigate Kitchener Seminar
- May 2, 2024
- Kitchener, ON Canada
Automate 2024
- May 6 - 9, 2024
- Chicago, IL
ANCA Open House
- May 7 - 8, 2024
- Wixom, MI