Editor
- FMA
- The Fabricator
- FABTECH
- Canadian Metalworking
Motion control on your plasma table
Understanding what is required of a high-precision table can help determine the right investment for your shop
- By Rob Colman
- Updated March 11, 2022
- March 24, 2022
- Article
- Fabricating
Plasma cutting technology has become more precise over the years, allowing shops to achieve cleaner, sharper, and more consistent edge quality in production. But not all plasma tables are created equal. The motion of the machine is dependent on mechanical and software inputs as much as it is on the power source itself. When shopping for a plasma system, it’s important to understand your end product goals and work back from there to determine what you require.
Choose Your Application
Plasma cutting tables have such broad potential applications, it’s important to consider what they will be used for: thick plate, HVAC, structural elements, bevels. Each application has its own requirements, so it’s also important to consider if precision parts, bolt holes, and other detail cuts will be required in production.
Motion quality isn’t an absolute. The cut quality required for some parts may not be as great, so a lesser motion quality may work in those cases.
“Quality is in the eye of the beholder,” said Joerg Toberna, director of marketing, Messer Cutting Systems. “The end result is a cut part. The question is, does it meet the requirements of your job? The answer to that is different for every shop.”
Speed requirements can play a role in machine choice, particularly if the goal is to produce thinner parts rapidly.
“Typically with thinner material, based on the amperage you are using, you will likely be going faster than you would on thicker material,” said Toberna. “If you don’t have the rigidity in your machine design, you are going to experience movement in the machine itself, which won’t allow you to achieve the quality you are looking for.”
If you are working with a very precise power source, of course, you will need to invest in superior motion control.
“For instance, Hypertherm’s XPR power source has a very stiff arc,” said Jacob Emery, product application engineer, Hypertherm. “So whatever happens for motion at the torch holder will happen on the arc end as well. What that means is that if your motion isn’t smooth or has a vibration, that is going to show up on your final cut part.”
Mechanical Guideways
There are a number of different guideway options for building a plasma machine, some of the most common being V-type, bar stock, and linear. But of course, each comes with a tradeoff.
“Bar stock used with check bearings are inexpensive but they are also inaccurate and are generally used on entry-level equipment,” said Tass Hamstra, sales manager, Machitech Automation. “V-type roller wheels are accurate, self-cleaning, and reliable, but they don’t offer much lateral stability for a machine with advanced processes such as bevelling and drilling.”
Linear guideways are considered the most accurate, but Hamstra warns that there are a variety of options even within this technology.
“Inexpensive linear bearings don’t have seals and will fail quickly in a plasma cutting environment,” he noted. “On a brand-new cutting table, those bearings might look like an upgrade from less expensive guideways but they just don’t last. Higher-end linear bearings are fully sealed and are even rebuildable.”
Digital Drives
Digital drive systems have to be engineered to suit the accuracy of your machine as well.
“If your processor can’t communicate quickly enough and receive data back from the table, you will have the same problem as you would with poor mechanical motion,” said Toberna. “Like your PC, if you have 20 applications open on your desktop, it’s going to slow down a bit. Your processor speed, if it isn’t properly sized for your applications, can act in a similar manner.”
Drives and Motors
Similarly, right-sizing drives and motors is important.
“Essentially you have to consider how much power is necessary for the performance you require,” said Toberna. “Heavier machines will generally require more powerful motors and drives to overcome the inertia of the machine. And you can have the best motor on the market but if your gearbox is subpar then you will get so much backlash you are not going to be able to cut that round hole. You can also oversize your drives and motors but that won’t necessarily provide better results.”
Hamstra notes that motor choice and quality can affect performance.
“Some high-end stepper motors are actually better than some lower-end servo motors, so while generally servomotors are a better choice, it depends on what you purchase,” he said.
“Some tables will actually have a motor with a direct drive output onto a pinion gear, with no gear reduction,” he noted. “This is not a good way to create a motion platform, but it is inexpensive because there is no gearbox. The gearbox allows your table to be tuned for a certain speed and acceleration, so it also has its own specs.
“Typically, in a plasma environment you are looking for a gearbox that is very high precision. This is measured in arc minutes,” Hamstra continued. “The lower the arc minutes number, the more precise the gearbox is and the less backlash you have, meaning that when you’ve got hold of the pinion gear you can’t move it back and forth. If you have any play there, you can imagine how that is amplified at the torch head as it moves through the motion in the machine. In all our machines, we use gearboxes that have less than 3 arc minutes in backlash. That’s the standard we use. Some have ratings at 7 arc minutes, which would be substantially less expensive.”
A helical rack and pinion drive system adds another level of precision to a table’s movement.
“The bonus to a helical rack compared to a straight rack is that you get smoother motion because you have more teeth in contact with the gear rack at all times,” said Hamstra. “It has more teeth engaged at any given time. A straight rack is ok, and there are many types of them. In a typical scenario, helical is going to give you smoother motion and better contact, and that allows you to have higher acceleration rates, allowing you to speed up and slow down faster, allowing you good-quality holes and good-quality corners. Plasma is all about achieving that right speed as efficiently as possible.”
Combos and Retrofits
For those considering a combination laser/plasma machine, it’s important to keep in mind the speed and robustness required by the technology at play.
“The acceleration and deceleration on a laser is much greater than what is needed on a plasma,” said Toberna. “So when you are looking at a machine being built for combo cutting, it needs two things: with the high acceleration and deceleration rates, the motion control needs to be much more substantial than it is on a standard plasma; and the machine has to be built to withstand the destructive power of a plasma. A plasma generates much more spatter and heat compared to a laser machine. Laser machines are generally not built for the harshness of that environment. A lot of these are going to be unitized machines rather than gantry-style designs.”
Shops that have older plasma tables and are considering upgrading the power source to achieve higher precision or hoping to add a drill station or bevel head should not be surprised if such an experiment delivers less than ideal results.
“Often with older machines the physical, mechanical backbone isn’t there to ensure the high-end movement required of these processes,” said Hamstra.
Ask Questions
Emery encourages people shopping for a new table to talk to table manufacturers about their motion controls, what they can handle in terms of tolerance, and acceleration.
“Get samples from the tables themselves so you see real world examples of what comes off that table,” he said. “With XPR, if you put that on two different tables, the way the cuts look might be very different.”
Emery noted that a ripple on the side of a cut, a really chewed corner, an overshoot, or small holes that appear oval are all indications that there may be a motion issue with a table.
One test that Emery and Toberna suggest is to use a pen trace tool to run different paths or parts at different speeds and then review the pen trace.
“Do you see wobbles in the corners? Do you see overshoot and then correction? Because if you see it on a piece of paper with a pen, you will see that in a plasma cut as well,” said Emery.
Ultimately, asking the right questions and understanding the goal of your system in terms of accuracy and precision will guide you to the right plasma system for your shop.
Editor Robert Colman can be reached at rcolman@canadianfabweld.com.
Hypertherm, www.hypertherm.com
Machitech Automation, www.machitech.com
Messer Cutting Systems, www.messer-cutting.com
About the Author
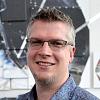
Rob Colman
1154 Warden Avenue
Toronto, M1R 0A1 Canada
905-235-0471
Robert Colman has worked as a writer and editor for more than 25 years, covering the needs of a variety of trades. He has been dedicated to the metalworking industry for the past 13 years, serving as editor for Metalworking Production & Purchasing (MP&P) and, since January 2016, the editor of Canadian Fabricating & Welding. He graduated with a B.A. degree from McGill University and a Master’s degree from UBC.
subscribe now
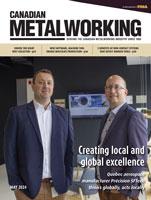
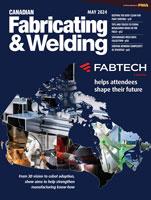
Keep up to date with the latest news, events, and technology for all things metal from our pair of monthly magazines written specifically for Canadian manufacturers!
Start Your Free Subscription- Trending Articles
Aluminum MIG welding wire upgraded with a proprietary and patented surface treatment technology
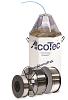
Hypertherm Associates partners with Rapyuta Robotics
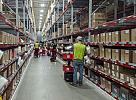
Protected and productive: welding helmet tech
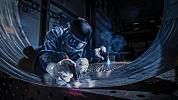
HGG Profiling Equipment BV names Western Canada area sales manager
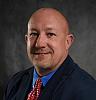
Compact weld camera monitors TIG, plasma processes
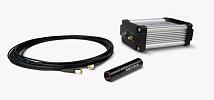
- Industry Events
CTMA Economic Uncertainty: Helping You Navigate Kitchener Seminar
- May 2, 2024
- Kitchener, ON Canada
Automate 2024
- May 6 - 9, 2024
- Chicago, IL
ANCA Open House
- May 7 - 8, 2024
- Wixom, MI
17th annual Joint Open House
- May 8 - 9, 2024
- Oakville and Mississauga, ON Canada
MME Saskatoon
- May 28, 2024
- Saskatoon, SK Canada