Associate Editor
- FMA
- The Fabricator
- FABTECH
- Canadian Metalworking
MoveMobility brings manufacturing in-house
Investing in new equipment allows MoveMobility to make customizable parts
- By Lindsay Luminoso
- December 4, 2023
- Article
- Fabricating
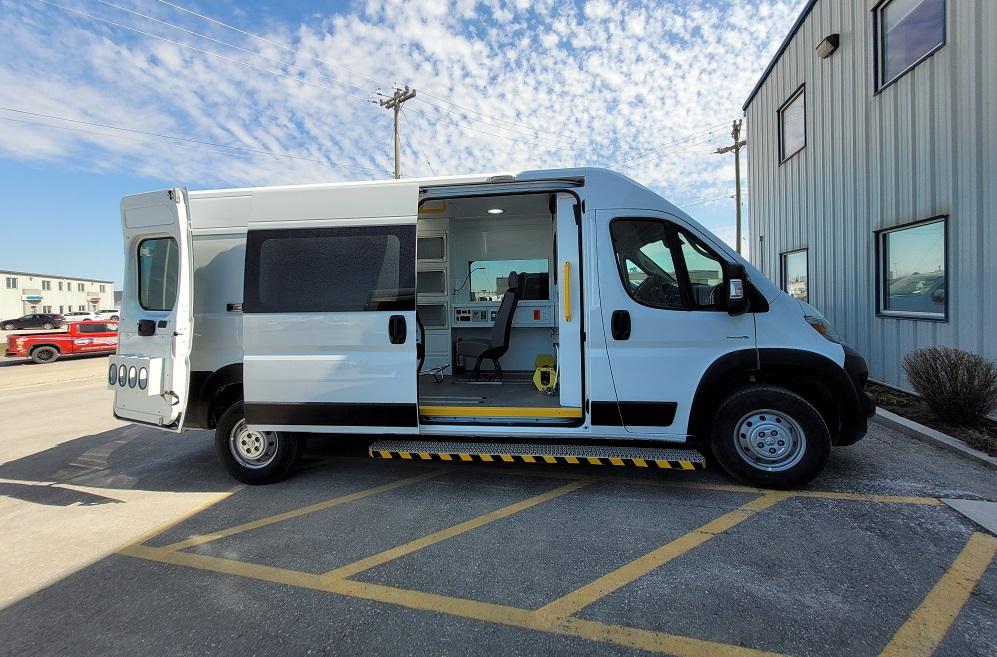
MoveMobility offers eight different options for wheelchair-accessible vans and four different mobile medical vans.
The team at MoveMobility had a vision – to manufacture innovative, customizable wheelchair-accessible vehicles and mobile medical vans. What started as a small operation has grown significantly over the past few years.
“We were one of the first companies in Canada to come to market with a medical vehicle,” said Bryn Jones, general manager, MoveMobility. “We can take a standard van chassis and modify the vehicle to include a range of different specifications depending on customer needs. For example, in the past 18 months, we’ve seen more and more organizations and medical associations looking for mobile clinic vehicles.”
Today, the company offers both wheelchair-accessible vans, which was its flagship offering, and mobile medical vans using Ram ProMaster and Ford Transit chassis in various roof heights and lengths. These vans are fitted with interior and exterior features based on usage.
The company offers eight different options for wheelchair-accessible vans and four different mobile medical vans.
The Mobile Response Van is a non-emergency mobile medical van that provides a mobile treatment space and transportation in one vehicle. The Mobile Medical Clinic Van is a mobile medical clinic used to bring healthcare directly to clients and is dubbed a doctor's office on wheels. The Mobile Outreach Van provides transportation and a safe on-site workspace designed for travelling street outreach teams. And the Mobile Mitigation Van provides a safe, sterile, and private space with sterile injection equipment and is billed as a mobile supervised consumption site.
“We have built quite a few mobile medical vans for regional health authorities that have a rural health program,” said Jones. “They will be used to go into communities that are more vulnerable, in populations that don’t want to be transported to a hospital, or to bring patients into hospitals that don’t have access to transportation. We spent a lot of time designing different options based on customer feedback and we are really proud of what we have to offer.”
Jones noted that the company’s goal is to manufacture ambulances, for which there is a great shortage of, by the end of the year. Currently, the company is working with governmental authorities in the U.S. and Canada to develop next-gen ambulances as well as focusing on the engineering and design of future options.
“We’ve seen so much growth over the past few years,” said Jones. “It’s really exciting. And while there are some other companies out there doing what we are doing, and let’s be honest, probably cheaper, we have found that the quality and utility that we are able to provide our customers has allowed us to thrive in such a heavily regulated industry.”
Manufacturing Operations
MoveMobility currently operates out of manufacturing facilities in Winnipeg and Mississauga, Ont., and employs over 50 people across both locations.
The company has invested in a huge acreage of land just north of its current location and hopes to expand onto this plot as it grows. Jones expects that a new facility is at least a few years away but will probably be three to four times the size of its existing space.
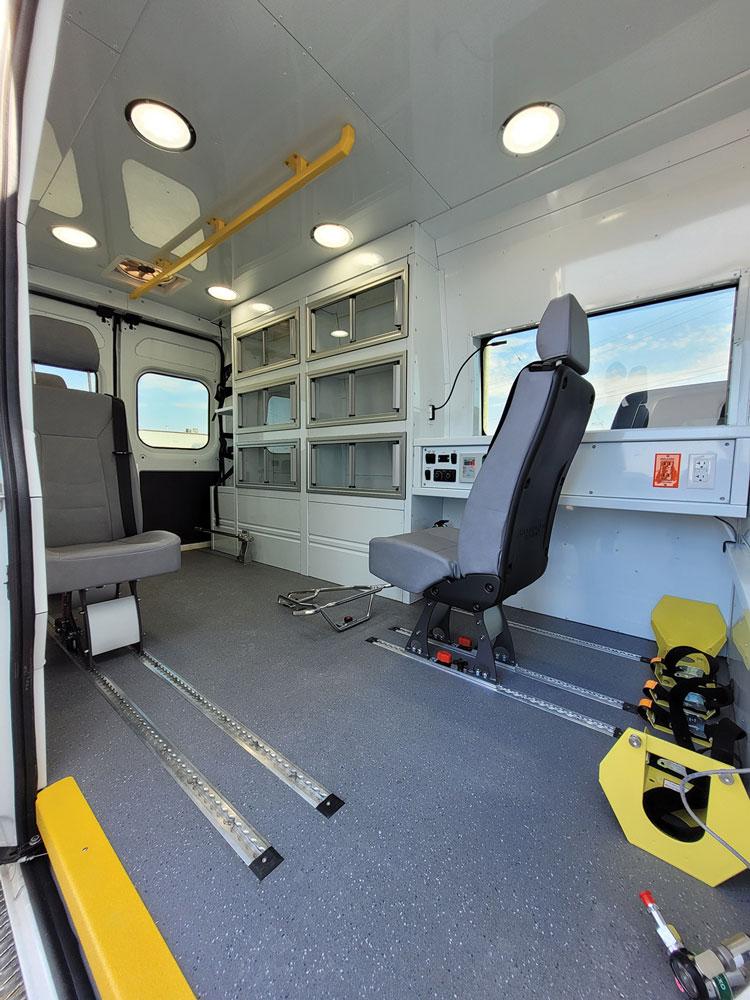
The interior of a Ram ProMaster has been fitted with features to make transferring patients safer and easier.
However, in the meantime, the company is focused on ensuring that it can meet the needs of its existing customers.
“As we started designing the different product lines, we recognized that there would be over 400 different components, 90 per cent of which would be mirrored left and right components, in each vehicle,” said Jones. “Because of this, we were only able to produce around one van per month with our existing suppliers. If even one piece was made wrong, the entire van production halted. It was a huge bottleneck in our production. And we also started to notice how expensive it was getting to outsource all the customizable panels.”
This is when Jones and his team started to explore bringing some of its manufacturing needs in-house. He turned to LinkedIn and asked the community to recommend equipment manufacturers. Immediately, a friend recommended Wallace Machinery & Tool Co. Ltd.
Jones reached out to Wallace Machinery to inquire about press brakes, knowing that pandemic supply chain issues were in full effect. The distributor had an Accurpress Accell Hybrid 190-ton floor model available that it used for spare parts.
“In August of 2022, they offered it to us, and we immediately said yes,” said Jones. “By December of that year it was delivered, and we had it wired up and running over the Christmas holidays.”
Just before the new press brake arrived, Jones also was in search of a fibre laser. But similarly, there were very limited options available in Canada because of supply chain issues.
Wallace Machinery was able to source a Mitsubishi ML3015GX-F60 in Japan that was a cancelled order.
“Originally, we were looking for something with advanced technology and all the bells and whistles, but we recognized the situation,” said Jones. “We weighed the pros and cons and ultimately decided that having something available now was a much better proposition than having to wait and continue to outsource.”
Again, the company jumped at the opportunity and by April 2022, the fibre laser was delivered. Within six months of bringing operations in-house, MoveMobility had brand new manufacturing plant setup.
Growing Pains and Gains
“One of the big challenges we faced with the shift in our operations was that we had this new equipment and no idea how to operate it,” said Jones. “My brother and I quickly realized we needed to learn how to use it. We hired two people from other organizations that had operated the same machines in the past. Having experienced operators made the transition easier. It was a leap of faith, and we took it. Looking back now, we accomplished a lot.”
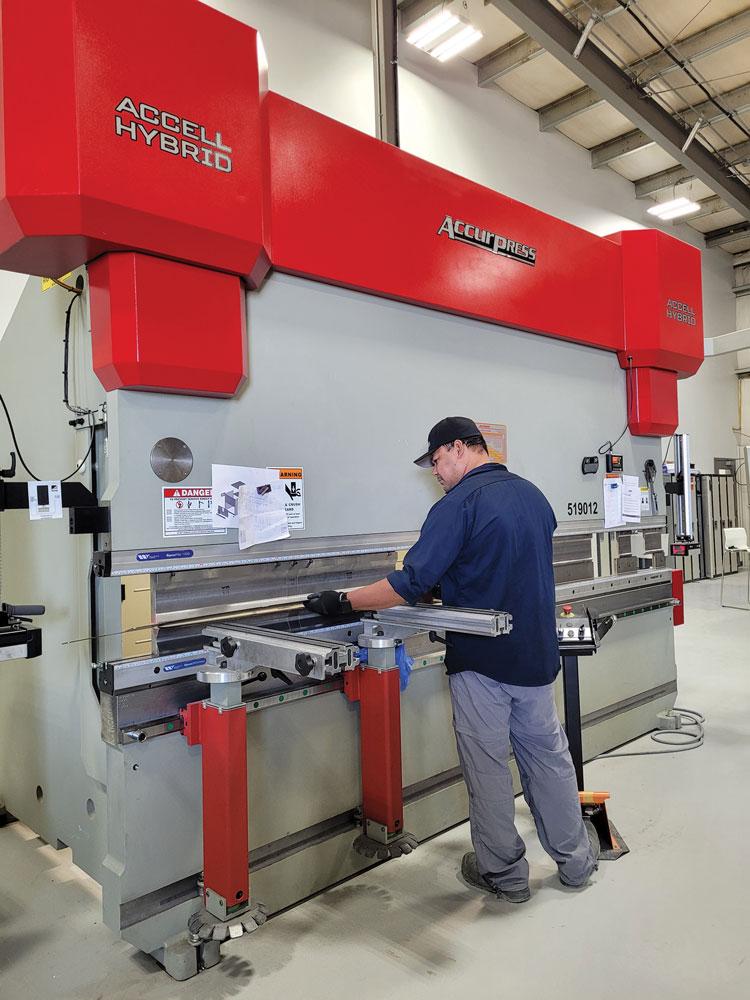
Jones reached out to Wallace Machinery to inquire about press brakes, and the distributor had an Accurpress Accell Hybrid 190-ton floor model that MoveMobility immediately purchased. It was installed in December 2022.
The fibre laser was purchased to solve a specific challenge—to produce components for a highly customizable, low-volume medical vehicle line that didn’t make sense to outsource. And while the company is now uses the laser to cut the parts, there are times when it sits idle.
“Right now, we’ve got this fantastic machine sitting idle,” said Jones. “It can turn things around quickly when we need it, which is why we have it. Some people think we are crazy to have it for only a few cuts, but that’s OK. It works for us, and it really will allow us to grow at a pace we are comfortable with. For us, the laser works great. Mitsubishi and Wallace Machinery’s support has been great throughout the process, which is what we needed.”
Another shift for MoveMobility was moving away from fibreglass panels to aluminum panels. Today, the company works primarily with pre-painted aluminum. The pre-painted sheets come in, the operators cut and bend it, leaving the laser film on right up until install. Beyond the traditional white, the company is looking to add yellow and black pre-painted aluminum sheets to make the processes more consistent.
Depending on the complexity, it take anywhere from 30 hours all the way up to 250 hours to build a van at the Winnipeg facility.
“The next step for us is robotic welding,” said Jones. “There are a number of subassemblies that we either have to hand-mount or subcontract out now. We would like to better control it in-house. The robot, if we brought it in right now, would only run two days out of the month. I can't justify the expense right now, but again, in the next few months, once we're steadily building ambulances and other vehicles, we probably can justify it. This would be for subassemblies only, as we have an eye on moving towards electric vehicles, and welding on those just doesn’t work.”
Currently, the company has several patents pending on existing designs, and they are about to jump into a new secret project that has the team very excited for the future.
“We are looking towards some very fun projects, taking on something that we really haven’t seen anyone else do before,” said Jones. “People are going to scratch their heads and wonder how we were able to do what we are doing, and that’s such a fun aspect of this business. We are pushing design and engineering limits and our manufacturing operations are supporting this innovation.”
Associate Editor Lindsay Luminoso can be reached at lluminoso@canadianfabweld.com.
MoveMobility, movemobility.ca
Wallace Machinery & Tool Co. Ltd., www.wallacemachinery.com
About the Author
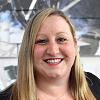
Lindsay Luminoso
1154 Warden Avenue
Toronto, M1R 0A1 Canada
Lindsay Luminoso, associate editor, contributes to both Canadian Metalworking and Canadian Fabricating & Welding. She worked as an associate editor/web editor, at Canadian Metalworking from 2014-2016 and was most recently an associate editor at Design Engineering.
Luminoso has a bachelor of arts from Carleton University, a bachelor of education from Ottawa University, and a graduate certificate in book, magazine, and digital publishing from Centennial College.
subscribe now
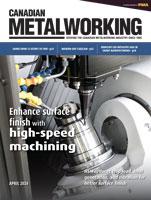
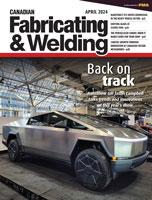
Keep up to date with the latest news, events, and technology for all things metal from our pair of monthly magazines written specifically for Canadian manufacturers!
Start Your Free Subscription- Trending Articles
Aluminum MIG welding wire upgraded with a proprietary and patented surface treatment technology
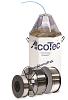
Achieving success with mechanized plasma cutting
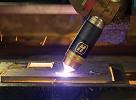
Hypertherm Associates partners with Rapyuta Robotics
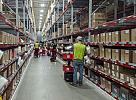
Gema welcomes controller

Brushless copper tubing cutter adjusts to ODs up to 2-1/8 in.
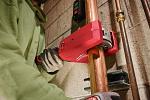
- Industry Events
MME Winnipeg
- April 30, 2024
- Winnipeg, ON Canada
CTMA Economic Uncertainty: Helping You Navigate Windsor Seminar
- April 30, 2024
- Windsor, ON Canada
CTMA Economic Uncertainty: Helping You Navigate Kitchener Seminar
- May 2, 2024
- Kitchener, ON Canada
Automate 2024
- May 6 - 9, 2024
- Chicago, IL
ANCA Open House
- May 7 - 8, 2024
- Wixom, MI