Editor
- FMA
- The Fabricator
- FABTECH
- Canadian Metalworking
Part flow precision push at CMP
Chateauguay, Que., electromechanical services company keeps bottlenecks in check with help from laser equipped with part sorting capabilities
- By Rob Colman
- September 12, 2023
- Article
- Fabricating
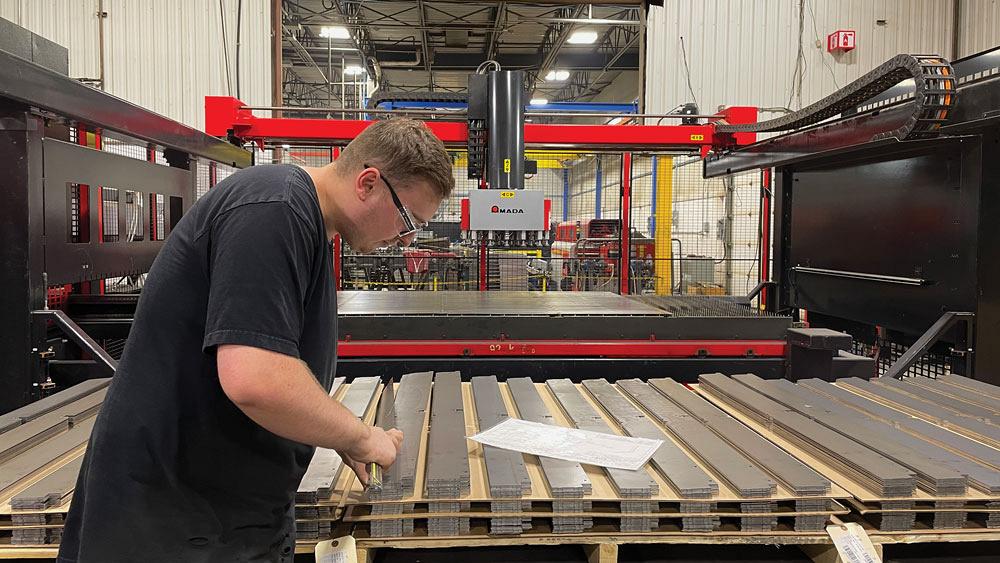
To ensure that it’s able to meet the demands of its customer base, CMP regularly invests in state-of-the-art technology. Most recently, that has included the purchase of an AMADA ENSIS 3015 AJ 9-kW fiber laser paired with an ASF 3015 EU tower and a TK 3015 automated parts sorter. Photos: CMP Advanced Mechanical Solutions
CMP Advanced Mechanical Solutions, Chateauguay, Que., is an electromechanical manufacturing services company that has been in business for more than 50 years. With its engineering, quality, and project management teams, it supports customers from prototype through pre-production and into volume manufacturing. To ensure that it’s able to meet the demands of its customer base, it regularly invests in state-of-the-art technology. Most recently, that has included the purchase of an AMADA ENSIS 3015 AJ 9-kW fiber laser paired with an ASF 3015 EU tower and a TK 3015 automated parts sorter.
Disruptive Tech in Focus
Recently, CMP shifted from being a broadly based electromechanical manufacturer to one focused on specific markets.
“We aim to focus on disruptive technologies,” said Jarrod Connolly, director, program management at CMP. “This includes the energy storage market, light rail, warehouse and logistics management, and a few others. In supporting these industries, the majority of our products come from our fabricated metals and welding business areas, but we have also introduced high-level assembly and integration into our facility. Ultimately, we want to be a full turnkey provider for our customers.”
Connolly noted that designs from design houses often don’t take manufacturability into account. That’s where CMP feels they make a big difference.
“We have many subject matter experts on our team who have been with us for a long time and can offer insight into how to approach the manufacturing process to make it as efficient as possible while also ensuring the highest quality level,” said Connolly. “We’ll look at implementing riveting solutions to avoid weld deformations, if that is a concern. We’ll look at different technologies to reduce the cost from a weight or materials perspective as guided by clients.”
Managing Manufacturing Flow
The company’s investment in technology reflects its desire to be as flexible as possible.
“In the markets we serve, there’s a lot of engineering churn, which means part stability is going to change,” he said. “So we need to be as flexible as possible with the machinery that we have available to us. Sometimes, rather than invest in the hard tooling of a punch press, we will want the speed and flexibility of a laser. But having both on hand allows us to flex when we need to support changes in our customers’ products, in terms of both design and volume.”
The purchase of an AMADA ENSIS 3015 AJ 9-kW fiber laser paired with a tower and automated parts sorter is an extension of this drive for flexibility.
The ENSIS fiber laser technology uses a Variable Beam Control unit that automatically and precisely adjusts the diameter of the laser beam. This enables continuous processing of thin-to-thick materials by a single machine with no lens change or additional setup required. It can process up to 1-in.-thick mild steel.
The TK 3015 automated part sorting system uses a 3-axis gantry design that allows the unit to move quickly and precisely anywhere over the shuttle table. It allows for 360-degree part rotation to easily remove parts nested in different geometries. Vacuum cups on the part sorter are individually assigned during programming to ensure each part is firmly gripped before removal to prevent pickup failure.
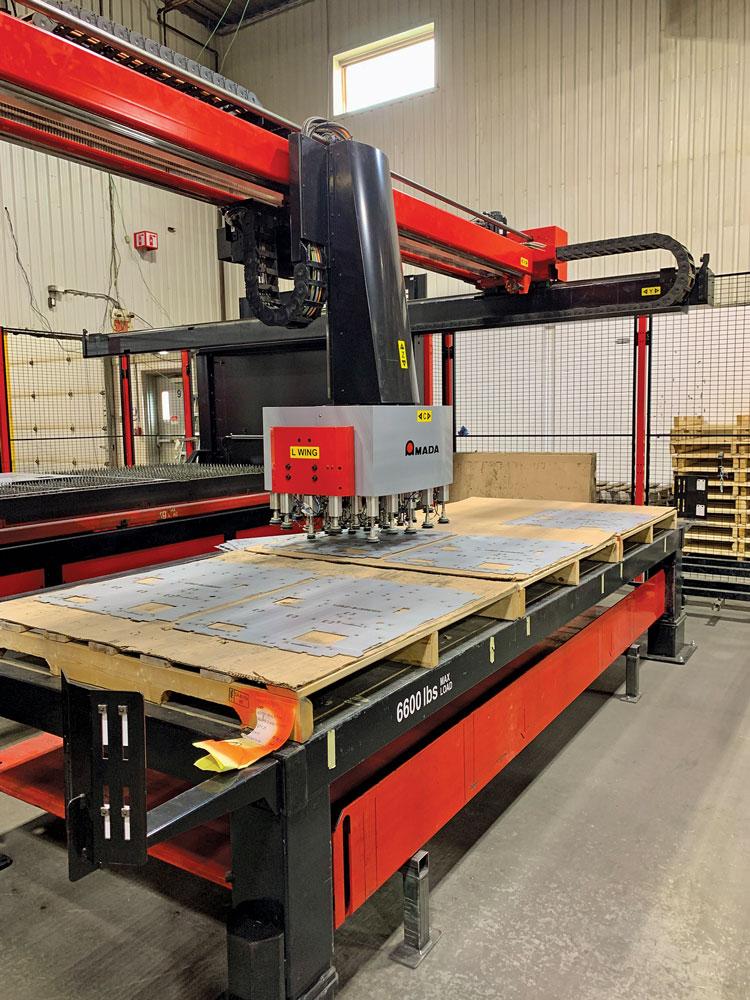
The TK 3015 automated part sorting system uses a 3-axis gantry design that allows the unit to move quickly and precisely anywhere over the shuttle table. It allows for 360-degree part rotation to easily remove parts nested in different geometries. Vacuum cups on the part sorter are individually assigned during programming to ensure each part is firmly gripped before removal to prevent pickup failure.
The best way to understand how the technology helps is to look at how the company approaches part flow through its facility. As Connolly explains it, they plan on using a theory of constraints model to drive production through what it calls the different “drums” in its facilities. The company uses multiple planning tools—from a linear production model to support some customers to a batch production model for others—to manage flow through its facilities.
The key to all of this, however, is understanding where the bottlenecks are for each customer’s production and managing production flow so that no one area of that production is left waiting for materials.
Flexibility Support
The company has invested in welding robots and an automated paint line to support part flow and uses assembly instruction management software managed by sister company VKS to aid in accuracy and efficiency in that area of the shop. Wherever possible, technology is used to help manage bottlenecks. The new laser with its part sorting capabilities fits right in with this.
“The laser with its part sorting technology is preparing us for the possible needs of our customers,” said Connolly. “Knowing that customers may have design demands that require the processing of a variety of materials in a short amount of time, this type of setup is ideal. With this machine, it’s easy to quickly process a variety of materials pulled from its tower and picking and placing finished cut parts for further processing.”
CMP works primarily with steel and aluminum, along with some pre-coated material, in gauges up to ¼ in.
This laser setup has been in place for more than a year now.
“We have had a relationship with AMADA that spans around 30 years, and it has been a very good partnership,” said Connolly. “This technology just seemed like the right fit for our customer base in the market at the time. The ability for us to have parts ready to go to subsequent operations, and the flexibility of being able to run multiple gauges and different materials on the laser as quickly as possible, gives us the full package for us to be able to optimize our production.
“It has definitely optimized part cutting and processing,” he continued. “Parts come off the laser without need of further processing before bending and assembly, and the speed and part sorting technology allows us to turn on a dime to shift production as necessary. The reduction of part handling, of course, is also a benefit, saving time and adding a level of worker safety to that part of our production. It’s the flexibility that it adds, and an added level of velocity, that means the most to us. There is no downtime with this machine.”
So while this type of part sorting technology might be used to kit all parts for an assembly in some shops, CMP is more interested in running as full of a nest as possible for a number of assemblies.
“We are consistently reprogramming our lasers to be as optimal for sheet utilization as possible,” said Connolly. “We want to get the most bang for our buck on the sheet use side. And because we have such a variety of products moving through the shop at specific times of the year, it’s rarely the same nest that’s running from hour to hour. In our linear production lines, we will nest to the highest utilization as possible for the project itself. But we also do dynamic nesting—looking at our two- and three-week release reports to understand what products are coming through the shop, and the gauges of those materials, so that we can select the appropriate sheet size and program optimally.”
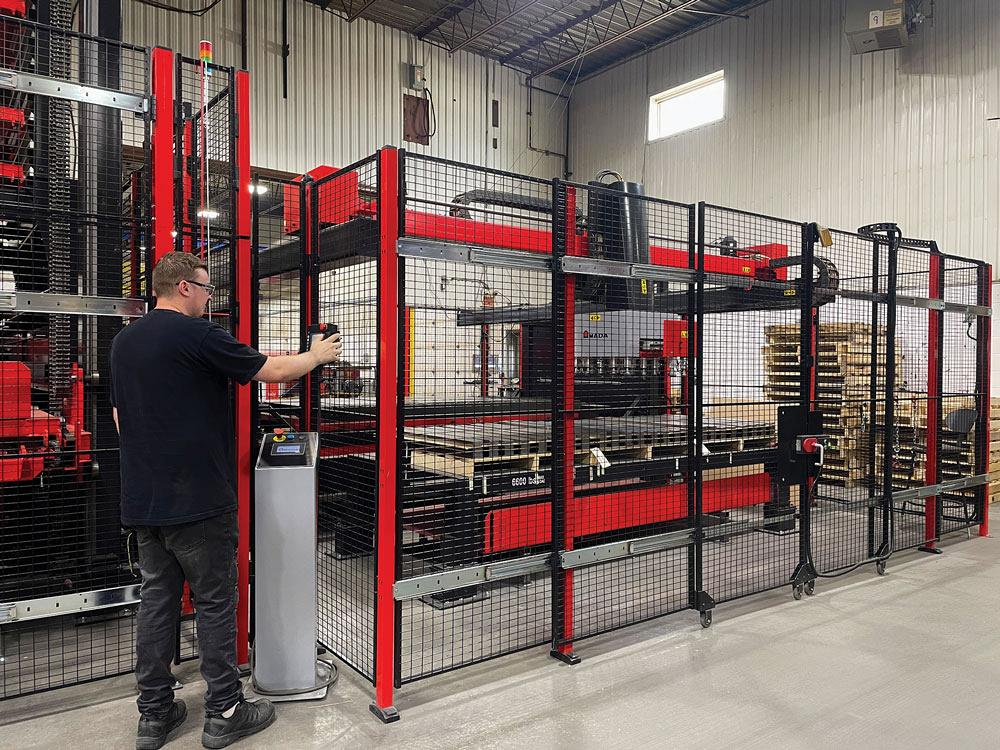
“It has definitely optimized part cutting and processing,” said Connolly. “Parts come off the laser without need of further processing before bending and assembly, and the speed and part sorting technology allows us to turn on a dime to shift production as necessary. The reduction of part handling, of course, is also a benefit, saving time and adding a level of worker safety to that part of our production.”
To manage this, Connolly considers the shop to have a “medium” amount of inventory, but it’s always a balancing act in terms of flexibility and staying as lean as possible.
“Having that flexibility upfront has helped us in our production processes,” said Connolly.
Asked what comes next for the company, Connolly insisted that process improvements are an ever-shifting target.
“The only constant in our business is change, and we embrace it.”
Editor Robert Colman can be reached at rcolman@canadianfabweld.com.
CMP Advanced Mechanical Solutions, www.cmpdifference.com
AMADA CANADA, www.amada.ca
About the Author
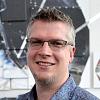
Rob Colman
1154 Warden Avenue
Toronto, M1R 0A1 Canada
905-235-0471
Robert Colman has worked as a writer and editor for more than 25 years, covering the needs of a variety of trades. He has been dedicated to the metalworking industry for the past 13 years, serving as editor for Metalworking Production & Purchasing (MP&P) and, since January 2016, the editor of Canadian Fabricating & Welding. He graduated with a B.A. degree from McGill University and a Master’s degree from UBC.
subscribe now
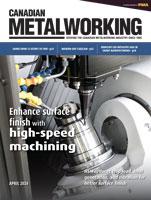
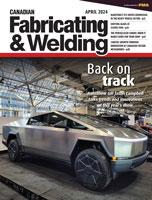
Keep up to date with the latest news, events, and technology for all things metal from our pair of monthly magazines written specifically for Canadian manufacturers!
Start Your Free Subscription- Trending Articles
Aluminum MIG welding wire upgraded with a proprietary and patented surface treatment technology
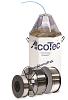
Achieving success with mechanized plasma cutting
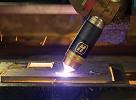
Hypertherm Associates partners with Rapyuta Robotics
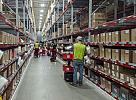
Gema welcomes controller

Brushless copper tubing cutter adjusts to ODs up to 2-1/8 in.
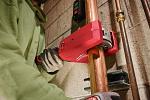
- Industry Events
MME Winnipeg
- April 30, 2024
- Winnipeg, ON Canada
CTMA Economic Uncertainty: Helping You Navigate Windsor Seminar
- April 30, 2024
- Windsor, ON Canada
CTMA Economic Uncertainty: Helping You Navigate Kitchener Seminar
- May 2, 2024
- Kitchener, ON Canada
Automate 2024
- May 6 - 9, 2024
- Chicago, IL
ANCA Open House
- May 7 - 8, 2024
- Wixom, MI