Director of technology and process engineering
- FMA
- The Fabricator
- FABTECH
- Canadian Metalworking
Prepping for robotic or automated material removal
Key steps on your journey to a more efficient finishing operation
- By Cédrik Rochon and Ryan Boyd
- February 26, 2024
- Article
- Fabricating
Editor’s Note: This article was adapted from the whitepaper, “A road map for implementing robotic or automated material removal in metalworking operations,” available at onlythebest.walter.com/automationcfw.
Material removal is a fundamental aspect of metalworking, encompassing processes such as grinding, sanding, finishing, polishing, deburring, and cutting. Most material removal applications (in metal) are made after welding, but some applications such as surface prep, cutting, or weld cleaning between passes, can take place before or even during the welding process. And it is not always glamorous work. Polishing stainless steel to a mirror finish is just as essential as grinding down heavy flashing on a cast metal part, but both processes are time-consuming, physically demanding, and require experience that is challenging for many companies to find, hire, and retain.
The projected shortage of welders in the next few years is often discussed in Canadian Fabricating & Welding, and while robotic welding systems can help shoulder some of that burden, the welders themselves are often responsible for several downstream processes as well—weld grinding, deburring, etc. If the welder is nowhere to be found, what does that mean for the pre-, mid-, or post-weld material removal work? These are some of the reasons why a company would consider automating some or all of its material removal processes.
To plan and execute the integration of robotic or automated material removal in fabricating operations, it’s important to consider your company’s readiness, requirements, technology options, and system design.
Shop Readiness
Assessing organizational readiness is a crucial step in planning the implementation of robotic or automated material removal systems as well as designing the improvement or expansion of pre-existing robotic systems. Below are three key considerations when assessing your shop’s readiness to automate:
- Technical infrastructure. Evaluate the existing infrastructure to ensure compatibility with automated systems. This includes available power supply, networking capabilities, and space for installation. Most metalworking machinery (CNC milling machines, press brakes, shears, bending systems, rollers, plasma cutting tables, etc.) requires the same power sources as robotic material removal cells. If you already have any of those in your facility, you are likely well equipped already.
- Workforce skills and training. Assess the skills of the existing workforce and identify training needs to ensure a smooth transition to automated processes. Training programs may be necessary to operate and maintain the new system efficiently and successfully. Some questions to ask are:
- Could your current employees/operators easily transition from doing the work to managing a machine that is doing the work?
- Do your current employees have prior experience with similar automated systems? If yes, the training needs are minimal. If no, training is required. Fortunately, today’s systems are more intuitive and having a similar learning curve as a touch screen tablet or smart phone.
- Regulatory compliance. Understand and comply with relevant industry regulations and standards concerning the integration of robotic or automated systems into the workplace. Collaborative robots, or cobots, which are becoming more popular because they are user-friendly and require limited programming, are great in certain applications but may not deliver the productivity of industrial robots when it comes to your operations. There are different safety regulations and space requirements to consider as well when deciding between different types of robots.
System Requirements
What is success? What does good look like?
Clearly defining the specific requirements for the automated material removal system is crucial for a successful implementation. Does 100 per cent of the process need to be automated? What about only 80 per cent of that process, since those are the least pleasant tasks for your workforce to perform?
These requirements encompass:
- Material types and sizes. Identify the types and sizes of materials that will be processed by the automated system to determine the necessary capabilities and specifications. Robot payload is an important factor to consider based on the size of tooling used at end of the arm when it’s a tool-in-hand process but also when it’s part-in-hand process. Tool-in-hand refers to the robot arm being directly equipped with a tool. Part-in-hand means that the robot picks up the pieces and brings them to a stationary working tool.
- Throughput and capacity. Estimate the required throughput and capacity of the system to ensure it can handle the expected production demands efficiently. Also ensure that your upstream processes can provide the expected workload to the robot or automated system.
- Oftentimes, focusing on current bottlenecks is a great place to start to ensure there will be sufficient satisfactory gains in terms of productivity.
- Process variability—ensuring machine compliance. Consider the variability in the material removal process, such as different shapes or surface finishes, and ensure the system can adapt and adjust accordingly. When looking at material removal, traditional accessories like abrasives naturally wear down as they work. To ensure your automated system is getting the highest output possible from the abrasives tools, force compliance devices often are used to allow for automatic compensation for (a) part-shape variability, and (b) orientation of working angle. In consequence, “active” or “passive” types of force compliance devices are essential to ensuring the most efficient and capable robotic material removal systems.
Active compliance devices apply consistent force in any orientation automatically, making it a great candidate for parts with curved surfaces.
Passive compliance devices, however, rely on external, customer-supplied air pressure regulators to set the applied force. They work extremely well for less demanding flat or prismatic parts or in more specialized processes like weld shaving, where high-accuracy force control is unnecessary.
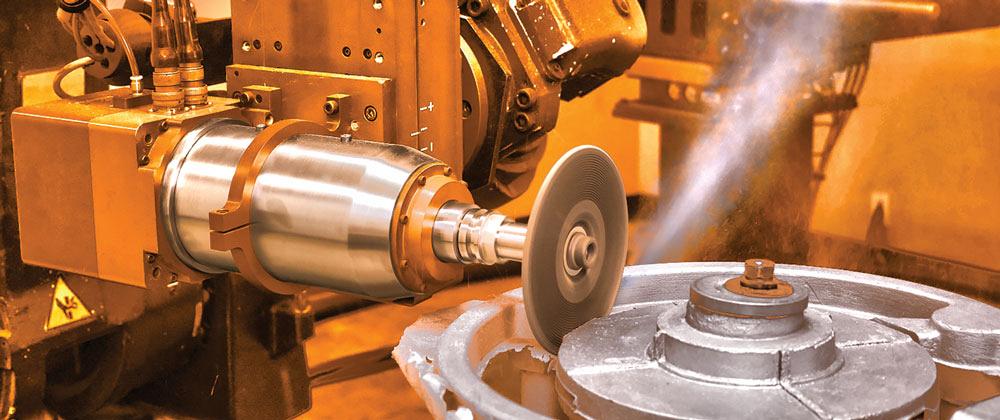
Assessing organizational readiness is a crucial step in planning the implementation of robotic or automated material removal systems as well as designing the improvement or expansion of pre-existing robotic systems.
Technology Choices
Choosing the appropriate technology is a critical step in the implementation process. Factors to consider include:
- Robotic platforms. Evaluate different robotic platforms (e.g., articulated, cobots, SCARA) and select one that aligns with your specific requirements and budget. If there are other pre-existing robots in your facility (robotic welding cells, for example) and you have a preferred brand based on reliability, service, etc., then you can often find a capable robot for material removal applications from that same trusted partner to ensure maximum compatibility and minimize the need for additional training.
- End effector tools. Select suitable end effector tools based on material and process. Also, consider whether the robotic process will be part-in-hand, tool-in-hand, or both. Compliance tools are often required when working with a consumable product like abrasive wheels, which change size and shape as they are used. An end effector tool that can compensate for that wear or change in force based on directional usage is crucial to ensure process reliability and conformity across the life of the consumable, as well as to eliminate the need to reprogram machine paths for every piece.
- Control systems. Choose a robust and user-friendly control system that allows for easy programming, monitoring, and integration with other components of the manufacturing process. Choosing a good integration partner with experience in the operations you’re trying to automate is also important because they can handle a lot of the programming uncertainties you may have, especially if you do not have anyone with experience already on staff. Choosing a product provider with an established relationship with integration partners can further help streamline processes and reduce project timeframes without sacrificing quality.
System Design
Designing the automated material removal system involves creating a detailed layout and architecture that ensures optimal performance and safety. It is also important to note that even though the goal is to replace previously manual tasks, the process itself could sometimes be modified significantly when adopting a robotic cell. Areas of access, piece fixturing, tool size, and consumable used are all variables that are usually constrained when it comes to manual work and the tools that are used. When it comes to robotic systems, the end result can often be attained faster and more efficiently thanks to the wider breath of accessories that are available.
Considerations include:
- Integration with existing processes. Ensure seamless integration with other manufacturing processes and systems, creating a cohesive and efficient production line. As mentioned previously, ensuring that the automated system will have no adverse effects on any other upstream or downstream processes is important. Understanding the “starting point” of the workpiece, the desired end result, and everything that happens in between is all part of the robotic system design process.
- Safety measures. Incorporate safety features such as sensors, emergency stops, and protective enclosures to mitigate risks associated with automated systems. Cobots often are marketed as tools that don’t need an enclosure or built-in safety measures that stop the robot when unexpected contact occurs due to their slower moving speeds. For material removal with high-speed or hazardous accessories on the end-of-arm tool that could potentially cause physical harm if not properly considered, cobots are not necessarily the safest choice.
- Ergonomics and accessibility. Design the system to be easily accessible for maintenance and equipped with user-friendly interfaces to streamline operations. An important thing to evaluate is where, when, and how operators will need to access the workpieces that have been worked on by the robot. Should the robot have two separate working bays, so while one is being loaded/unloaded, the robot remains in action? If maintenance needs to be performed on the robot, will it require dismantling the entire cell to access certain parts? Thinking ahead can help reduce these potential issues and delays.
Integrating robotic or automated material removal in fabricating operations will be key for growth at many companies in the near future. Planning that integration will be essential for your team.
Ryan Boyd is director of sales engineering and Cédrik Rochon is director of technology and process engineering at Walter Surface Technologies, 5977 Trans-Canada Highway W., Pointe-Claire, Que. H9R 1C1, 800-363-7368, www.walter.com.
About the Authors
subscribe now
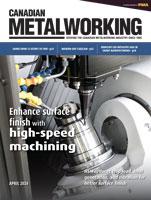
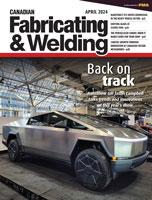
Keep up to date with the latest news, events, and technology for all things metal from our pair of monthly magazines written specifically for Canadian manufacturers!
Start Your Free Subscription- Trending Articles
Aluminum MIG welding wire upgraded with a proprietary and patented surface treatment technology
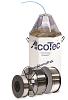
Achieving success with mechanized plasma cutting
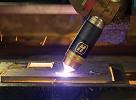
Hypertherm Associates partners with Rapyuta Robotics
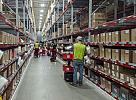
Gema welcomes controller

Brushless copper tubing cutter adjusts to ODs up to 2-1/8 in.
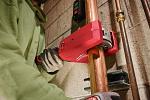
- Industry Events
MME Winnipeg
- April 30, 2024
- Winnipeg, ON Canada
CTMA Economic Uncertainty: Helping You Navigate Windsor Seminar
- April 30, 2024
- Windsor, ON Canada
CTMA Economic Uncertainty: Helping You Navigate Kitchener Seminar
- May 2, 2024
- Kitchener, ON Canada
Automate 2024
- May 6 - 9, 2024
- Chicago, IL
ANCA Open House
- May 7 - 8, 2024
- Wixom, MI