Editor
- FMA
- The Fabricator
- FABTECH
- Canadian Metalworking
Rethinking the spray gun
Ergonomics, efficiency at heart of new design
- By Rob Colman
- January 10, 2022
- Article
- Fabricating
A spray gun is never going to be the most high-tech tool on your shop floor, but ensuring that it is operating at peak capacity and as efficiently as possible can sometimes occupy more time than it should. A relatively new spray gun from 3M aims to change that.
Spray Basics
“The main concern anyone is going to have is how well the gun sprays,” said Bill Suzuki, applications development specialist with 3M Canada. “Operators want to make sure that it’s a robust tool and that they can set up and maintain a nice spray pattern, whether they are spraying an adhesive, a thicker coating, or a paint. That’s what they rely upon.”
Much of the key information that leads to a good spray transfer is supplied in the technical data provided by the manufacturer of the liquid.
“These data sheets will explain recommended pressures; the atomizing tip size to use (anything from 1.2 mm to 2 mm); and the required viscosity of the product, which sometimes involves thinning the product,” said Suzuki. “Once those are dialled in, then it’s up to the technician to adjust their distance and hand speed to achieve the coverage and finish they are looking for.
“Hand speed will depend on the individual. It’s a good idea, with any new coating you are using, to test a scrap part to figure those things out. Typically, the faster your hand movements, the more you are able to open the fluid adjustment to allow more fluid to come out, but painters who are slower have to reduce the flow, particularly on a vertical. That’s where you can get runs on topcoats or provide too thick a coating. It doesn’t take long for an experienced applicator to dial in those settings, though.”
What Makes A Good Spray Gun?
What makes a good spray gun is the ability to replicate a pattern time after time.
“A key thing is transfer efficiency,” said Suzuki. “That is the percentage of the coating coming out of the gun that ends up on the surface you are spraying. You want that percentage to be in the mid to high 70s. Anything that doesn’t end up on the part is wasted on the floor, masking, or out the exhaust. That increases your costs on supplies, but also more time wasted on more passes over your parts.”
Maintaining that spray pattern can involve regular cleaning of the gun also.
“If a product hardens up in a gun, it could take an operator a couple of hours disassembling and cleaning the gun of material,” said Suzuki. “So, a product that takes less time to be cleaned can be a benefit.”
A concern that operators don’t consider as often is the ergonomics of a spray gun. Whether the operator is using a pressure pot or a gravity-fed spray cup on top of the gun, the less weight involved in the whole assembly, the less likely the operator is going to feel fatigued by the work.
The last consideration is how quickly the operator can change out colours or types of coatings on the gun.
“Sometimes operators will bring multiple spray guns into a booth because that is the only way they are able to achieve the efficiencies they hope for with the tools they have on hand,” said Suzuki.
Design Difference
3M recently introduced its Performance spray gun to address many of these issues. The main difference with this spray gun is that the coating being sprayed does not flow through the gun body.
“The atomizing head is the only part of the whole system that comes into contact with the material you are spraying,” said Suzuki. “If something hardens in it, it can easily be swapped out for a new head. In terms of cleaning that head, because you are only cleaning it and not a whole gun, you will use a fraction of the cleaning solvent you might otherwise have to use.”
The exchangeable head enables the operator to switch out the tip size to anywhere from 1.2 to 2 mm for a gravity-fed system, and between 1.1 and 1.8 mm for fluids from a pressure pot.
“This means that the same gun can be used for both thick and thin materials,” said Suzuki.
If an operator is using multiple colours in the same booth, it is possible to go into the booth with several PPS™ cups equipped with their own heads.
“In that case, it’s just a matter of wiping off the needle that regulates the flow through the atomizer head when switching from colour to colour,” said Suzuki. “Depending on the cycle time of production, this can be an immense time savings.”
The ergonomic adjustment in this product’s development was to make the gun body out of composite material, which makes it lighter than metal guns.
“This is actually a stumbling block initially for some spray gun users because they expect a certain heft from a gun,” said Suzuki. “But once they see that it does the job, the ergonomic benefits become clear.”
Editor Robert Colman can be reached at rcolman@canadianfabweld.com.
3M, www.3m.com
About the Author
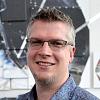
Rob Colman
1154 Warden Avenue
Toronto, M1R 0A1 Canada
905-235-0471
Robert Colman has worked as a writer and editor for more than 25 years, covering the needs of a variety of trades. He has been dedicated to the metalworking industry for the past 13 years, serving as editor for Metalworking Production & Purchasing (MP&P) and, since January 2016, the editor of Canadian Fabricating & Welding. He graduated with a B.A. degree from McGill University and a Master’s degree from UBC.
subscribe now
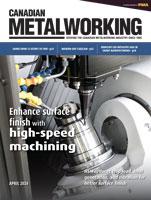
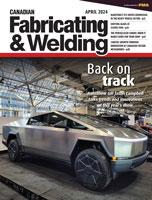
Keep up to date with the latest news, events, and technology for all things metal from our pair of monthly magazines written specifically for Canadian manufacturers!
Start Your Free Subscription- Trending Articles
Aluminum MIG welding wire upgraded with a proprietary and patented surface treatment technology
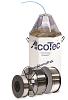
Achieving success with mechanized plasma cutting
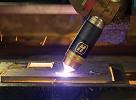
Hypertherm Associates partners with Rapyuta Robotics
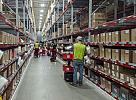
Gema welcomes controller

Brushless copper tubing cutter adjusts to ODs up to 2-1/8 in.
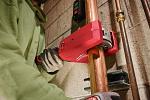
- Industry Events
MME Winnipeg
- April 30, 2024
- Winnipeg, ON Canada
CTMA Economic Uncertainty: Helping You Navigate Windsor Seminar
- April 30, 2024
- Windsor, ON Canada
CTMA Economic Uncertainty: Helping You Navigate Kitchener Seminar
- May 2, 2024
- Kitchener, ON Canada
Automate 2024
- May 6 - 9, 2024
- Chicago, IL
ANCA Open House
- May 7 - 8, 2024
- Wixom, MI