Associate Editor
- FMA
- The Fabricator
- FABTECH
- Canadian Metalworking
When to form on a turret punch press
Overcome application challenges with the latest machine and tooling features
- By Lindsay Luminoso
- October 16, 2023
- Article
- Fabricating
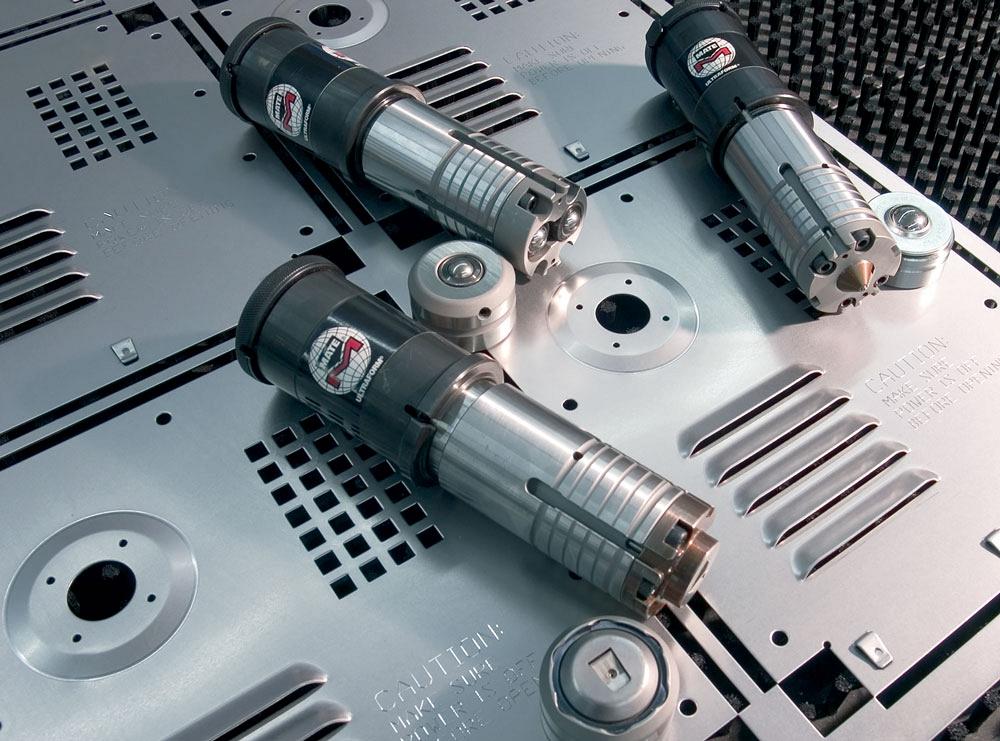
With Mate Ultraform, you can have an unlimited number of forming tools and use the same holder, reducing your overall tooling spend. Want to use a different form? Simply swap out the forming insert. Mate Precision Technologies
It’s all about reducing cycle time and secondary operations. That’s one of the main benefits of performing forming operations on a turret punch press. Not all punch presses are created equal, and there are some considerations to take note of before jumping in. But for fabricators that are currently running a form that requires multiple setups on a press brake, significant handling, or challenging angles of sheet, forming on the punch press may eliminate these issues. This is especially important for fabricators that are trying to run lean operations and reduce transportation time and waste.
Another benefit relates to the skilled labour shortage facing the industry today. Keeping as many projects as possible on the same machine means that fewer operators may be needed. On a turret punch press, one operator can perform multiple operations on one machine rather than constantly moving around the shop.
For the most part, high forming usually required a press brake. However, as many fabricators know, wait times for press brakes often are a production bottleneck. Using a punch press to form can help alleviate any backlog at the press brake and even reduce the need to invest in a new machine to deal with overflow capacity.
“There are a lot of forms that fabricators don’t often realize can be made on a turret,” said Susan Erler, product manager, punching/My Account, Wilson Tool International, White Bear Lake, Minn. “But producing them this way has lots of advantages.”
Limiting Factors and Features for Forming on a Punch Press
Start with the machine. With so many types of punch presses available, understanding the machine’s capabilities will help determine if forming (or “the form”) is possible and what the limiting factors are related to the operation.
Feed Clearance. “The operator or programmer needs to know the machine,” said John Ripka, application technician, Mate Precision Technologies, Anoka, Minn. “Especially the size of the gap between the upper and lower turret plates. It all comes down to calculating how much height is needed to make a particular form, and if that is within that clearance.”
Knowing the feed clearance can help fabricators determine how high of a form the machine is capable of producing. The make and model of the machine should dictate that feed clearance.
“The feed clearance, or the space between the lower turret and the upper turret, historically has been 0.787 in.” said Erler. “Newer machines have higher feed clearance, 0.984 in. in many cases, allowing for higher forms. There are also machines with a single open punching head that can create forms beyond 1 in. high. If you have a lot of high forms in your product line, then you're going to want to steer toward a machine with that higher feed clearance.”
Tonnage. Another consideration would be the machine’s tonnage. Tonnages available in new machines range from 20 to 30 metric tons. Tonnage matters, particularly in forms like knockouts where they often exceed the tonnage capacity. There are some punch press machines capable of punching up to 50 tons.
“If you're doing a triple, quad, or tangential [forms], that tonnage adds up very quickly,” said Erler. “It can also come into play if you are planning on doing formed logos that require a lot of tonnage. It’s important to know the tonnage capacity to determine if certain forms can be produced.”
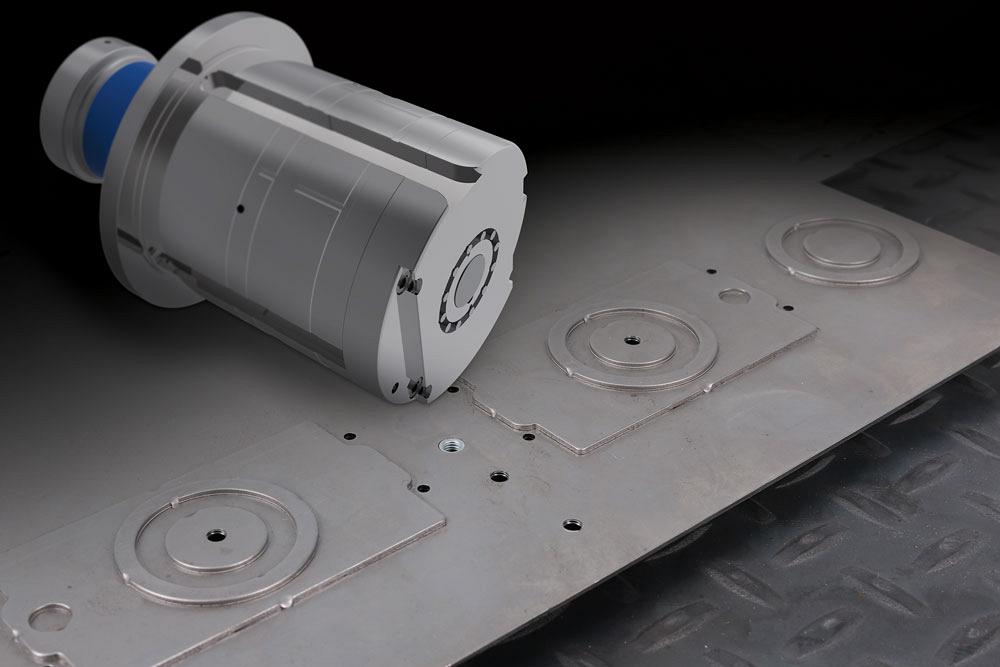
When an application calls for a multiform electrical knockout (EKO), there are tooling options. Depending on your machine, tooling style, material type, and thickness, it is possible to create triple, quadruple, and even tangential EKOs in one hit. Wilson Tool International
Programmable Ram. A majority of new punching presses have a programmable ram versus a mechanical ram. A programmable ram allows for wheel tools, hinge tools, and deburring tools in the turret where the sheet moves, while the ram is in hover mode or while it is held down and the operator moves the sheet.
Infinite Stroke Control. This feature allows the stroke of the punch (upper tool, regardless of punching or forming) to be controlled to within 0.0005 in. (0.01 mm).
“This allows very accurate control of the tool to create the desired forms,” said Ripka. “Also, it allows very small changes in stroke length, forming height, or angles to be made.”
Upforming Stations. Upforming stations provide more room to work with taller forms. While some machines have it, it is generally an optional feature.
“There may be a limit to the number of upforming-type stations that some machines can have,” said Ripka. “Most machines will only have maybe three or four of these upforming stations when they're available. However, these stations can expand forming capabilities to include taller forms.”
Most forming applications that result in forms taller than a material thickness or two use spring-loaded dies to help with stripping. These dies are typically much taller than standard dies. Upforming stations and machines that can drop the die below standard die line use these features to assist with stripping as they pull the die away from the bottom side of the sheet (and form). They also allow taller forms because the die does not take up valuable forming space above the standard die line.
Auto Indexing. How many auto-index stations does the machine have and where are they situated? Auto indexing is important, not just for forming, but also for sheet slitting and shearing.
“Many tools require an auto-index station to perform a radius and make anything that's not a straight line,” said Erler. “If you think of that 0.984-in. feed clearance, in some cases you can get forms that are close to 1 in. high. Some tools have a cam in the lower unit, so you can progressively wipe up that form using the auto-index station, creating forms much larger than the largest station.”
This allows for forms to be produced on a punch press that traditionally would require a press brake.
Forming Applications and Tools
There are so many different forms, from simple to complex, that can be produced on a turret punch press, as long as the machine has the features and capabilities to handle it.
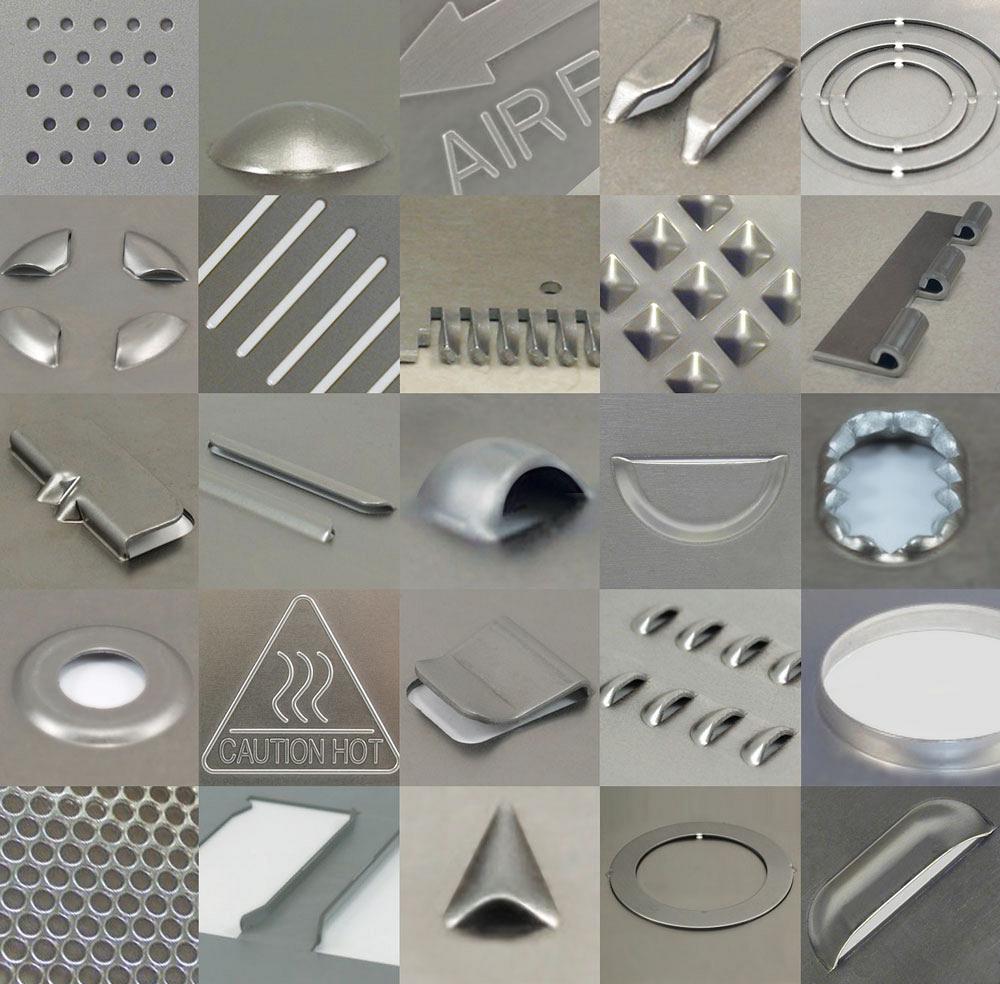
Simple forms such as extrusions, embosses, or bent tabs are relatively easy to create, as long as the machine has the necessary space to allow the forms. More complex forms, such as hinges, card guides, cold forge embosses, and multiple bend tabs, can be created with a bit of programming expertise and operator experience. Mate Precision Technologies
“Simple forms like countersinks, extrusions, and embosses can pretty much be done on any machine, even if you don't have any special upforming capabilities because the form heights are minimal. They don’t require much space or turret gap to be created,” said Ripka.
When you get to complex forms like hinges or formed tabs with multiple bends, depending on the height, there's more thinking and calculations involved to make sure that these can be produced. There also is a level of skill involved with more complex forms. An operator with limited forming experience may encounter some trial and error during the process before the formed dimensions are correct.
“Add a radius on any bend whenever you can,” said Erler. “Go with the largest radius that the form allows for and ensure that you have realistic tolerances. We sometimes see prints where tolerances are extraordinarily tight, and it'll turn out to be something where the tolerance really doesn't matter. So have tolerances where they're important but not where they're unnecessary.”
To ensure good forming, fabricators should provide detailed drawings to their tooling suppliers. These suppliers can review the forms and also what is next to the forms to create a big picture of the overall process. Are there forms nearby that we need to relieve the tool for? Could that nearby hole distort when we make the form? Then punching should be done after forming. In many instances, tooling suppliers can look at all aspects and lend guidance on the process and order of operations and shed light on any potential red flags.
Overcoming Forming Application Challenges
When forming, the machine is stretching and pulling material from one place and moving it to another, which creates stress in the sheet. Stress in the sheet creates the tendency for it to curl or twist. And the more forms added, the more likely the sheet will curl or deform.
“If you can’t get the sheet to stay flat or stay coined, you may have issues with the sheet corners or form features catching on the underside of a turret plate or tools that may hang down a little bit from an upper turret,” said Ripka. “So, it’s important to be careful when you're processing parts that have forms.”
When forming with the grain or across the grain, one method might create more stress than the other because of the way the material is forged or fabricated. If you can reduce the amount of distortion, this can save a lot of headaches in the long run.
“A lot of that is just paying attention to detail of your sheet and sheet orientation,” said Ripka. “In some cases, forming closer to the clamps might be easier than forming away from the clamps. However, if you're doing a whole row of hinges, it may be easier to start away from the clamps and then move toward the clamps because of how the sheet will actually stretch, and locations will slightly change. If you're perforating a sheet, the sheet actually expands. With the different operations, you have to consider what direction you want to punch or form to keep overall accuracy of the locations of your forms.”
Having a programmer or operator who is experienced certainly helps, especially with some of the more challenging forms. Experience also will make some of the decisions and steps involved more intuitive. Some shops may not be familiar with all the forms that the punch press can make, but experienced operators may be willing to push limits.
“You're really converting the turret into a little mini press brake,” said Erler. “Wipe-up tools of 90 degrees are a good example of that. Sometimes customers think that if a form is too big for the biggest station that there's no way that you could do it on a turret. Wheel tools allow you to form sizes much larger than your maximum station size. Fabricators sometimes forget that what they think is a limiting factor may not always be one.”
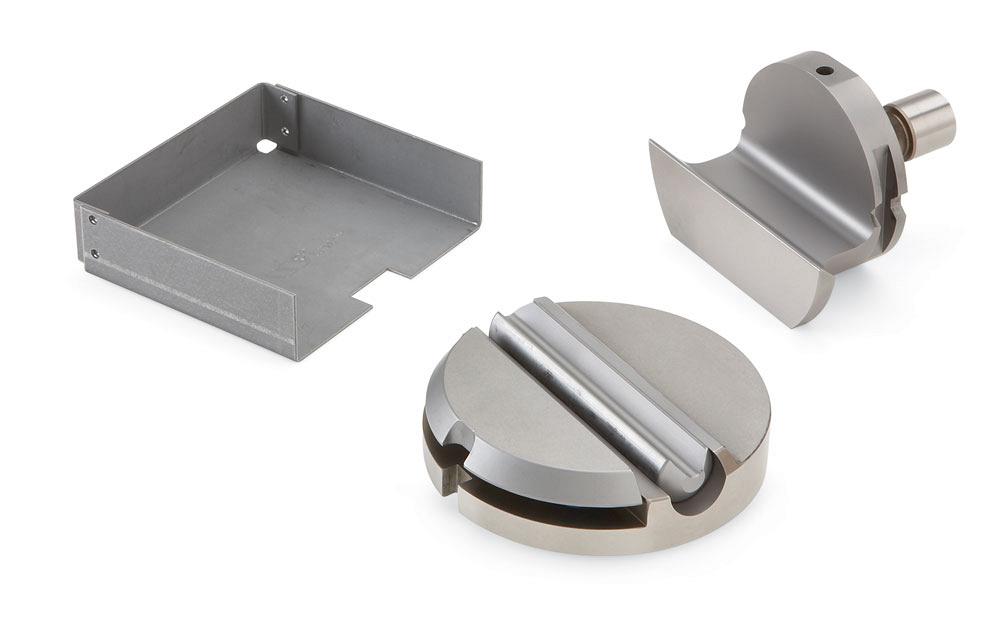
Wilson Tool’s Opti-Bend tooling enables sheet metal fabricators to perform 90-degree bends on a punch press, eliminating time-consuming secondary operations typically performed on a press brake. Wilson Tool International
If the material is thin, fabricators can use an option such as a thread form tool that allows for a self-tapping screw to be used even in thin material.
There are some forms where fabricators may think they will yield too much sheet distortion—for example, a huge emboss that is fairly high. While the feed clearance is okay, the sheet will most likely distort. It’s important to note that oftentimes there are ways around that.
“A specific dimple tool can preform that emboss, stretch the material, and somewhat minimize the distortion on that hit, then do a post-form to form higher than you would think while mitigating the sheet distortion,” said Erler. “Fabricators need to remember that there are often tooling options that solve the machine and turret limitations.”
The Importance of Station Placement on the Turret
It’s important to recognize that typical forming dies will sit taller than a standard punching die, which can significantly affect a station’s placement in the turret.
“Forming dies will typically sit up to 0.25 in. higher than a typical punching die,” said Ripka. “If upforming is not available, every time the sheet moves across that die, you may get extra scratches on the bottom of the sheet. Also, if you have a taller forming die right next to a punching die, the sheet may not lie flat during punching. There's a chance that you can put a little kink or dent in the sheet during punching because the uneven sheet level results in downward flex during punching, because the adjacent forming die sits higher than the punching die.”
One of the ways around this is to place the forming dies in the same area. While this is not always possible, it will certainly help. Another thing to consider, if possible, is to ensure that you are not punching next to a forming die.
“Punch your holes first, then do forming,” said Ripka. “It’s not necessarily going to eliminate the issues, but in most cases it is the best option.”
Ripka also suggested adding a dummy move in the middle of the process to allow for a die to be swapped out. This would effectively allow fabricators to punch all the holes without the forming die in the turret. And then with the dummy move, the forming die can be installed and forming operations can start. While this adds an extra step and increases cycle time, it can be an effective and often overlooked option.
Station selection can sometimes come into play as well. For the most part, fabricators go with the smallest station that the form will fit in to reduce cost. However, choosing a larger station than the geometry calls for can also be effective in reducing distortion.
“There are times where you get distortion in the station that the size of the die dictates,” said Erler. “By going to a larger station where there is more holding pressure on the sheet from the biggest surface area, you can mitigate sheet distortion.”
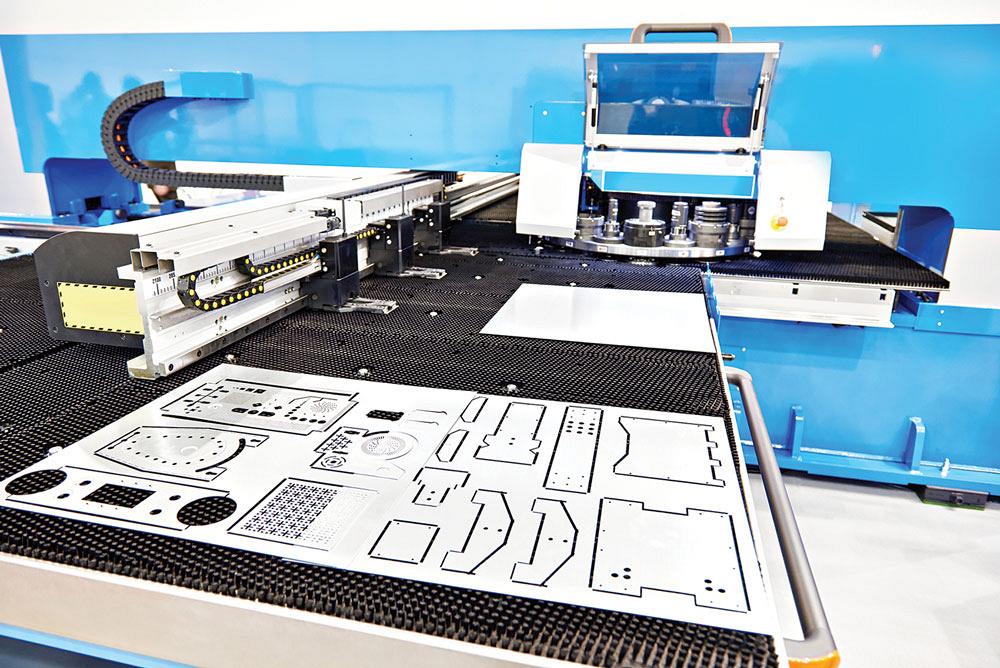
Forming dies will typically sit higher than a typical punching die. If the sheet moves across the forming die, it can scratch the bottom of the sheet. sergeyryzhov/iStock/Getty Images Plus
Associate Editor Lindsay Luminoso can be reached at lluminoso@fmamfg.org.
Mate Precision Technologies, www.mate.com
Wilson Tool Intl., www.wilsontool.com
About the Author
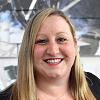
Lindsay Luminoso
1154 Warden Avenue
Toronto, M1R 0A1 Canada
Lindsay Luminoso, associate editor, contributes to both Canadian Metalworking and Canadian Fabricating & Welding. She worked as an associate editor/web editor, at Canadian Metalworking from 2014-2016 and was most recently an associate editor at Design Engineering.
Luminoso has a bachelor of arts from Carleton University, a bachelor of education from Ottawa University, and a graduate certificate in book, magazine, and digital publishing from Centennial College.
subscribe now
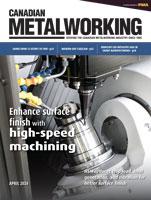
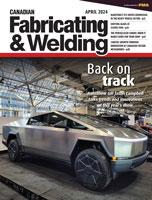
Keep up to date with the latest news, events, and technology for all things metal from our pair of monthly magazines written specifically for Canadian manufacturers!
Start Your Free Subscription- Trending Articles
Aluminum MIG welding wire upgraded with a proprietary and patented surface treatment technology
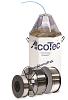
Achieving success with mechanized plasma cutting
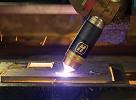
Hypertherm Associates partners with Rapyuta Robotics
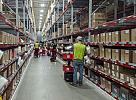
Brushless copper tubing cutter adjusts to ODs up to 2-1/8 in.
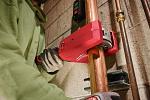
Gema welcomes controller

- Industry Events
MME Winnipeg
- April 30, 2024
- Winnipeg, ON Canada
CTMA Economic Uncertainty: Helping You Navigate Windsor Seminar
- April 30, 2024
- Windsor, ON Canada
CTMA Economic Uncertainty: Helping You Navigate Kitchener Seminar
- May 2, 2024
- Kitchener, ON Canada
Automate 2024
- May 6 - 9, 2024
- Chicago, IL
ANCA Open House
- May 7 - 8, 2024
- Wixom, MI