Associate Editor
- FMA
- The Fabricator
- FABTECH
- Canadian Metalworking
Keeping a safe distance with physical barriers
Physical barriers can help mitigate the risks associated with robotics on the factory floor
- By Lindsay Luminoso
- September 20, 2023
- Article
- Health & Safety
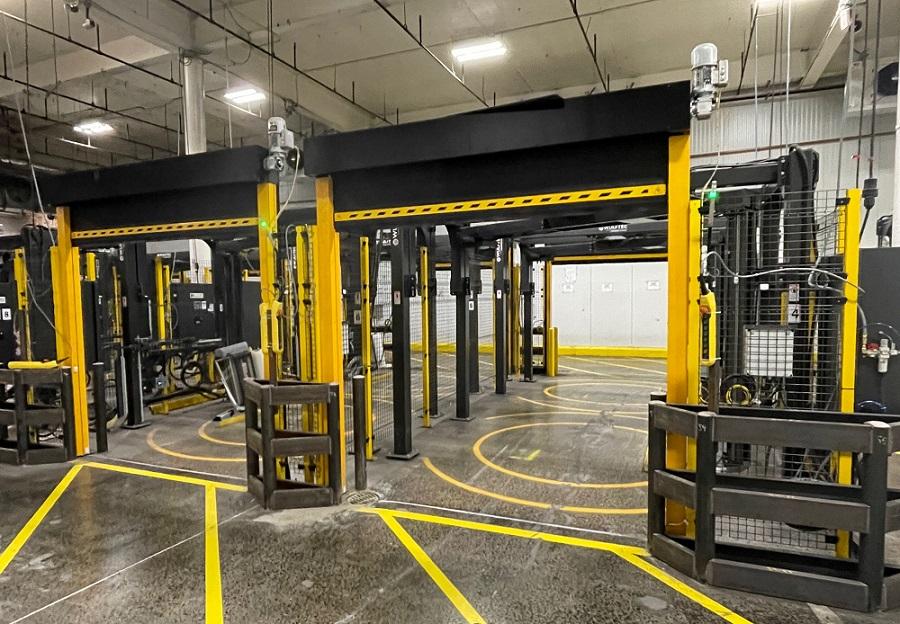
A roll-up door can potentially be located much closer to the manufacturing process because it eliminates the potential for human interaction. It also offers the ability to adjust and arrange the shop floor, potentially offering ergonomic and productivity benefits. Images: Dynatect
Automation presents both a great opportunity and a significant risk on the shop floor. Manufacturers that are new to robotics and automated equipment can quickly become overwhelmed when creating a safe work environment. Working with companies that specialize in safety devices specifically designed for automation is a good place to start.
“From a worst-case-scenario standpoint, shops can explore engineering controls to reduce that risk all the way through the process,” said Eric Esson, national sales manager, Dynatect, New Berlin, Wis. “That's where safety devices come in. Using engineering controls, shops can make a determination on the type of device that makes the most sense based on distance formulas and shop floor layout.”
The new ANSI/RIA R1506 standard requires shops to look not only at the primary risks of using robots and automation, but also at the secondary risks associated with the task. A risk assessment should be thorough enough to evaluate every part of the machine and process.
“It really spreads the responsibility, not only to the supplier of the safety equipment, but the machine provider and process engineers,” said Esson. “It makes everyone take ownership of risk mitigation.”
Safety starts at the top, but it’s also important to ensure that there is employee buy-in. Once automation is in place and a risk assessment has been performed, choosing the correct safety device can be challenging.
“There are advantages of using a roll-up door,” said Esson. “This physical barrier can take the place of that light curtain and offers the same level of safety per ISO 13849-1. It’s important to examine the operation as well. The motion of the robot is the primary hazard, but what the robot is doing should be examined as a secondary hazard. Is there an opportunity for a light curtain or does another device make more sense?”
Esson gives the example of a stretch wrap system application. There is the potential for entanglement and getting drawn into the machine because of the rotating pallet. What is preventing people from being in that area while there is motion taking place?
“A physical barrier like a door makes a lot of sense in applications where the stoppage time may be a problem,” he said. “With the door being a physical barrier, it can potentially be located much closer to the process itself, because there is no potential for human interaction. So not only are you getting a safe work environment, but it also offers the ability to adjust and arrange the shop floor, potentially offering ergonomic and productivity benefits.”
Another advantage of using a physical barrier like a roll-up door is that this device does not require visual cues like a light curtain. Visual pollution can be a problem and workers can become immune if there is too much stimuli in an environment.
“From a lean manufacturing principle, the door is very simple and clear,” said Esson. “When it is up, there is a sense of urgency. The operator should be performing a task. If that door is up and no operator is working, then that visual cue can signal to management that they need to assess why the worker is not performing the task at hand. The visual cues of the door are much more obvious than those found in other safety devices.”
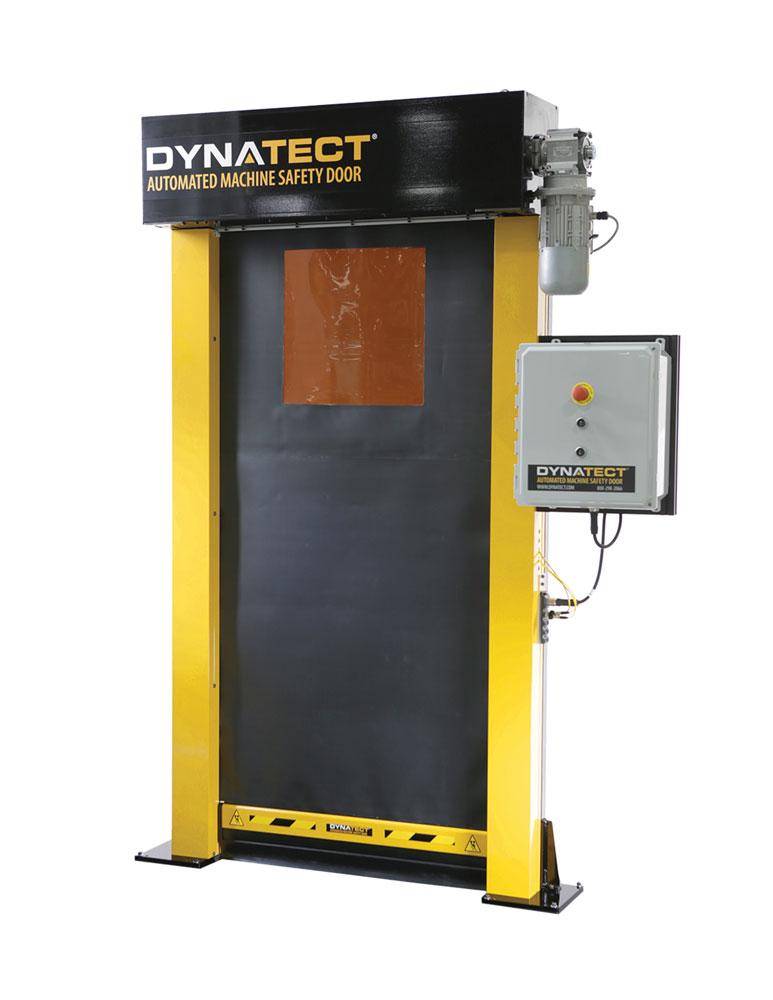
This roll-up door can take the place of a light curtain and offers the same level of safety per ISO 13849-1, according to Dynatect’s Eric Esson.
Some manufacturers don’t think about physical barriers and roll-up doors as a safety device option. Light curtains and laser scanners tend to be more commonplace but physical barriers are being used more and more.
“When some shops invest in a new piece of equipment, some employees may not have any experience working with the technology,” said Esson. “What do we need to do? How does this work? These are just some questions that employees might be asking. It’s important to get them up to a comfort level with the equipment, and proper training can do that. Having the correct knowledge of how safety works, the sequence of operation, what to expect, how to troubleshoot; knowing what to do when something happens is the biggest hurdle that shops can overcome with proper training.”
With a more global marketplace, there is a push towards standardization of safety standards. For the most part, many of the standards that exist in North America are merging with those in Europe and Asia, making them more international-friendly standards.
“A company manufacturing in Canada or the U.S. may be sending equipment to Europe or Asia,” said Esson. “Global or harmonized standards worldwide will make it easier for the machine builders to provide a trouble-free product, regardless of where it's going. The CSA standards are pretty much in line with the U.S. standards, which are pretty much in line with the European standards for any automation processes, with some exceptions.”
Esson explained that there are still areas of opportunity for harmonization. For example, Europe has existing standards for palletizing or stretch wrapping end line processes. If a device rotates more than six or seven times per minute, the standard requires guarding around the device. However, in Canada and the U.S., there are no regulations for this.
“As we see more harmonization, we can assume that if the standards exist in Europe, they will most likely be implemented in North America, and vice versa,” said Esson.
Associate Editor Lindsay Luminoso can be reached at lluminoso@canadianfabweld.com.
Dynatect, www.dynatect.com
About the Author
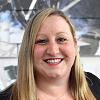
Lindsay Luminoso
1154 Warden Avenue
Toronto, M1R 0A1 Canada
Lindsay Luminoso, associate editor, contributes to both Canadian Metalworking and Canadian Fabricating & Welding. She worked as an associate editor/web editor, at Canadian Metalworking from 2014-2016 and was most recently an associate editor at Design Engineering.
Luminoso has a bachelor of arts from Carleton University, a bachelor of education from Ottawa University, and a graduate certificate in book, magazine, and digital publishing from Centennial College.
subscribe now
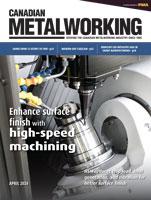
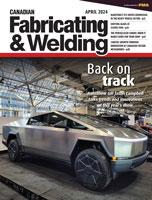
Keep up to date with the latest news, events, and technology for all things metal from our pair of monthly magazines written specifically for Canadian manufacturers!
Start Your Free Subscription- Trending Articles
Aluminum MIG welding wire upgraded with a proprietary and patented surface treatment technology
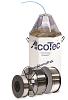
Achieving success with mechanized plasma cutting
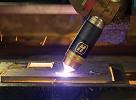
Hypertherm Associates partners with Rapyuta Robotics
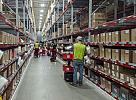
Gema welcomes controller

Brushless copper tubing cutter adjusts to ODs up to 2-1/8 in.
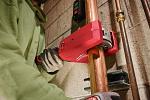
- Industry Events
MME Winnipeg
- April 30, 2024
- Winnipeg, ON Canada
CTMA Economic Uncertainty: Helping You Navigate Windsor Seminar
- April 30, 2024
- Windsor, ON Canada
CTMA Economic Uncertainty: Helping You Navigate Kitchener Seminar
- May 2, 2024
- Kitchener, ON Canada
Automate 2024
- May 6 - 9, 2024
- Chicago, IL
ANCA Open House
- May 7 - 8, 2024
- Wixom, MI