president
- FMA
- The Fabricator
- FABTECH
- Canadian Metalworking
Lean practices are a required foundation for automation investment
Ensure lean principles cascade to all tech rollouts for lasting efficiencies
- By William (Bill) Neeve
- February 15, 2024
- Article
- Management
Lean manufacturing must be an all-encompassing system in your business if you hope to gain all of the benefits its introduction is designed to provide. It is not an event, it is a holistic approach to operating daily.
Newer technologies like cobots draw the eye of employees and owners alike. Their flexibility and ease of programming make them an ideal tool for filling gaps created by retiring employees and the challenges of finding new talent for a shop floor. But like any other piece of automation, a cobot is simply a means to an end—a tool. If you hope to get the most value possible out of a cobot, it has to be viewed in the big picture of your manufacturing operations.
Likewise, the implementation of Industry 4.0 connectivity requires the same rigor to ensure the data you collect is both as complete as necessary and collected in a manner that makes it a useful, rather than underused, tool.
Lean can add great value to your company, but it requires a combination of lean methodologies, technology, and, most importantly, effective communication across the organization. Lean can make the introduction of new forms of automation and new methods of information flow easier because, when used in a holistic manner, it helps shape the way in which they are introduced.
Critical Lean Starting Points
Any lean journey requires buy-in from the top of an organization. If you are going to go through any transformation, you have to start with the senior team so that they have a good grounding in what it involves and what is necessary to make it work.
A holistic view for such a transformation involves immersing the whole company in lean thinking so that there is a lean foundation for every technology investment throughout the company. That means building it on the foundation of the five lean principles of the Toyota Production System:
- Value. Value defines what really matters to your customers. It is the customer that defines the value of your product or service and the reason that you exist.
- Value Stream. A value stream represents all the value-added and non-value-added activities required for your product or services to flow from concept, development, transformation of raw material or information, delivery to and payment from your customers.
- Flow. Flow indicates how well your value stream is functioning. Does it start and stop, lacking rhythm and failing to deliver on time; or is it smooth as silk, just humming along and delivering just-in-time (JIT)?
- Pull. Pull is a replenishment system initiated by consumption, or by actual customer orders, wherein the upstream internal or external supplier produces something only when the downstream internal or external customer signals a need.
- Perfection. Perfection is the ideal of continually improving value, value stream, flow, and pull. Perfection will never be achieved, but you will get as close to perfection as is possible by continuously cycling through the five lean principles.
Once the senior team is trained to understand how lean works as a long-term philosophy, even at the expense of short-term goals, your organization can start developing cross-functional teams. Teams like this, bringing expertise from each area of the business, help everyone better understand how the business functions as a whole. Oftentimes, one part of a company really has little understanding of how another operates and why.
Oftentimes companies use Band-Aid solutions throughout a business; at the time, that solution made sense, but quite often no one returns to the issue and considers whether there’s a more efficient way to handle it. Lean creates an environment where processes are continually revisited to ensure they are as efficient as necessary.
Value Stream Mapping and Automation Rollouts
Value stream mapping is the method by which a cross-functional team sits down and examines the flow of processes through a business. Through this exercise, it’s possible for everyone to understand where the bottlenecks are in a manufacturing facility and what might be the best manner in which to improve that flow. Members of the team can look at key steps of the process and ask, Do we still need all of those pieces in the process? Once the process flow through the business has been made as efficient as possible, only then does it make sense to determine how new investments might further improve flow.
When considering an investment in new technology, you might be tempted to only look at the processes on the floor. However, it’s critical to understand how information flows from the front office to inform that process as well. What type of files flow from the front office to the back? How are these files received from customers and has this filesharing been standardized? If not, does it need to be? Understanding the flow of information from the arrival of a part design to when that part is shipped to a customer is critical in understanding where efficiency gains can be found.
A value stream map is not a static process, however. Parts change, customer requirements change—it’s important that these be revisited regularly to ensure optimal flow is maintained.
When a disruptive technology becomes available that might change the nature of that flow, these cross-functional teams are just as critical. Sitting down as a group, they can discuss important concerns such as whether it will require reallocation of human resources, a reconsideration of the shop layout, and a discussion of what complementary technologies may be worth considering as next steps in the facility’s efficiency journey.
Industry 4.0 - The Next Level of Efficiency
Companies wishing to optimize their operations need to understand the interplay between a traditional lean management system and Industry 4.0.
The connection between lean thinking and Industry 4.0 is their shared goal of operational excellence. As Industry 4.0 is driven by cyber-physical systems, so will lean thinking, or as we refer to it, Lean Industry 4.0. Lean Industry 4.0 operates in new technologies that augment traditional lean strategies.
Lean Industry 4.0 and Industry 4.0, like lean in general, should be implemented holistically, rather than independently or sequentially. This provides a much better understanding of customer demand and allows the immediate sharing of the demand data throughout complex supply chains and networks.
Industry 4.0 facilities will produce faster with less waste by integrating production and logistics processes, enhancing cooperation among machines and humans, and increasing efficiency on the factory floor. Cyber-physical systems enable a much quicker one-piece flow of customized products and have the potential to radically reduce inventories throughout the supply chain.
In Industry 3.0, using lean manufacturing in the physical world, lean success is created through JIT manufacturing. Lean thinking is implemented within a facility’s four walls and is a commitment to:
- Total focus on the customer.
- JIT manufacturing and inventory management.
- Engaged, educated, empowered employees.
- Pull production.
In Industry 4.0, Lean Industry 4.0, in the virtual world, success is achieved through JIT information. Lean Industry 4.0 is implemented across the entire supply chain, from suppliers to customers, and is a commitment to:
- Total digital focus on the customer.
- Digital product information or innovation.
- Data-driven services.
- Digital operations, or operational excellence.
Some of the tools for this transformation include:
- Cloud computing – Using cloud-based software for enterprise and analytics applications. More production-related undertakings will require increased data-sharing across sites and company boundaries. As a result, machine data and functionality will increasingly be deployed to the cloud, enabling more data-driven services for production systems.
- Internet of Things (IoT) – Having field devices communicate and interact with one another and with more centralized controllers, as necessary. This also decentralizes analytics and decision-making, enabling real-time responses.
- Simulation – Using this technology to leverage real-time data to mirror the physical world in a virtual model, operators can test and optimize machine settings for the next product in line in the virtual world before the physical changeover, thereby driving down machine setup times and increasing quality.
System integration will drive companies, departments, functions, and capabilities to become much more cohesive as cross-company, universal data-integration networks evolve and enable truly automated value chains. The collection and comprehensive evaluation of data from many different sources—production equipment, enterprise and customer management systems—will become standard to support real-time decision-making.
Lean Industry 4.0 ensures that lean thinking will continue to play a key role in driving customer satisfaction while also providing an organizational real-time structure that is flexible, productive, and profitable while driving growth.
Companies will be able to expand on their lean thinking understanding and knowledge as they move to Lean Industry 4.0. Many companies have started lean-thinking activities within their organizations, but very few are Lean Industry 4.0 ready, which also means that they may not be Industry 4.0 ready.
The reason for this was discussed earlier. If senior management is not driving the lean bus, lean thinking will fail to reach expected goals, or it may fail completely.
Creating a functional lean management operation is a top-down proposition—it is not rocket science. Which means it is never too late for any organization to commit to lean thinking, and in so doing, commit to excellence. But for the rollout of a successful Lean Industry 4.0, a baseline lean structure has to be established.
Lean Support
If you haven’t started the lean journey, you might want to lay the foundation with lean first and, in parallel, develop your draft technology plan. When you start a lean transformation and evaluate the flow of the business with value stream mapping, you always start with a map that shows how the business is operating today. With that map, you consider what could be done better and come up with a future-state map. While you are doing that, you should be developing a technology plan that overlays the future-state map.
If your company has already started lean or integrated certain types of technology, never hesitate to take a step back and re-evaluate your situation. It’s never too late to change tack to ensure you have the right plan in place to keep your business flexible enough to adapt to future needs.
For those hesitant to tackle lean thinking, there are assessment processes available that can help you determine where you are currently before taking the lean journey and help you to consider what should come next. What technology should mirror your standard lean rollout? Remember, lean is a journey, not a set destination.
William (Bill) Neeve is president of Cycle Time Management Inc., 525 Highland Rd. West, Suite 100, Kitchener, Ont. N2M 5P4, 226-747-7475, billneeve@leancycletime.com, leancycletime.com.
About the Author
William (Bill) Neeve
subscribe now
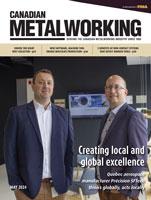
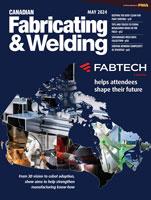
Keep up to date with the latest news, events, and technology for all things metal from our pair of monthly magazines written specifically for Canadian manufacturers!
Start Your Free Subscription- Trending Articles
Aluminum MIG welding wire upgraded with a proprietary and patented surface treatment technology
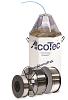
HGG Profiling Equipment BV names Western Canada area sales manager
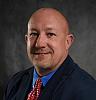
Protected and productive: welding helmet tech
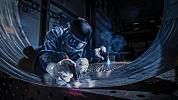
Automotive industry gets back on track
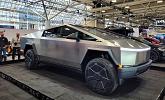
Power source added to cobot welding system for simplified automation
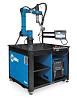
- Industry Events
Automate 2024
- May 6 - 9, 2024
- Chicago, IL
ANCA Open House
- May 7 - 8, 2024
- Wixom, MI
17th annual Joint Open House
- May 8 - 9, 2024
- Oakville and Mississauga, ON Canada
MME Saskatoon
- May 28, 2024
- Saskatoon, SK Canada
CME's Health & Safety Symposium for Manufacturers
- May 29, 2024
- Mississauga, ON Canada