Editor
- FMA
- The Fabricator
- FABTECH
- Canadian Metalworking
Setting safety milestones at AGI Olds
Alberta facility celebrates 10 years with no lost time incidents
- By Rob Colman
- January 30, 2024
- Article
- Management
In November, Ag Growth International (AGI) celebrated an outstanding safety milestone at its Olds, Alta., manufacturing facility with a no lost time incidence record that spans a decade. AGI marked the achievement with a special event and awards ceremony honouring the facility’s employees.
“Ten years with no lost time incidents is an incredible feat,” said Paul Householder, AGI president and CEO. “I commend the Olds team, who is dedicated to manufacturing excellence while looking out for each other and setting a high safety bar. At AGI, our goal is that every employee—regardless of where they work or the type of environment they work in—returns home at the end of each day in the exact same working condition in which they arrived. This is a top priority, one that I personally take very seriously."
A lost time incident (LTI) refers to a non-fatal injury that results in disability or an employee missing work due to an injury. An LTI measurement is a baseline representation of a company's safety performance and the effects of those injuries on workforce productivity.
Top-Down Leadership
“I am very proud of the employees. It is the result of the work they do on the floor, making great choices, being observant of their surroundings, and proactively identifying and mitigating potential hazards,” says Steve Ricklefs, AGI Olds plant manager. “They rose to the challenge and exemplify how safety is a priority that unites our workforce, ensures safe work conditions, and creates a more supportive environment for us to succeed.”
The AGI Olds facility was first commissioned in 1998, to produce smooth wall grain bins and hopper bottoms. Today, the Olds facility manufactures best in class AGI Westeel fuel storage tanks for agricultural and industrial applications. Tanks come in both single-wall or double-wall configuration and can be either stationary or mobile.
This attention to safety details doesn’t happen by chance, of course. Ricklefs believes it’s important that this concentration on safety starts at the senior management level.
“It’s well communicated from senior leadership that this is a priority,” he said. “We have key performance indicators based around safety expectations. Senior management wants to know about any injuries, but they also want to hear about the near misses and the hazards that are reported, and what we have done to mitigate those hazards.”
Daily Practice
On the ground, safety considerations begin before an employee even starts their first day on the job.
“We do things like pre-employment screening to assess whether a candidate fits our safety culture,” Ricklefs explained. “And then, through the on-boarding process, employees go through a rigorous orientation that communicates our general plant safety rules, such as what to do if you spot a hazard and what you do if you injure yourself at work. Once the orientation’s done, we train them on hazard assessments and our health and safety manual. We don’t expect them to full digest all that information right away, but it’s important to give them that exposure from Day 1.”
The Olds facility has many ways it keeps safety top of mind.
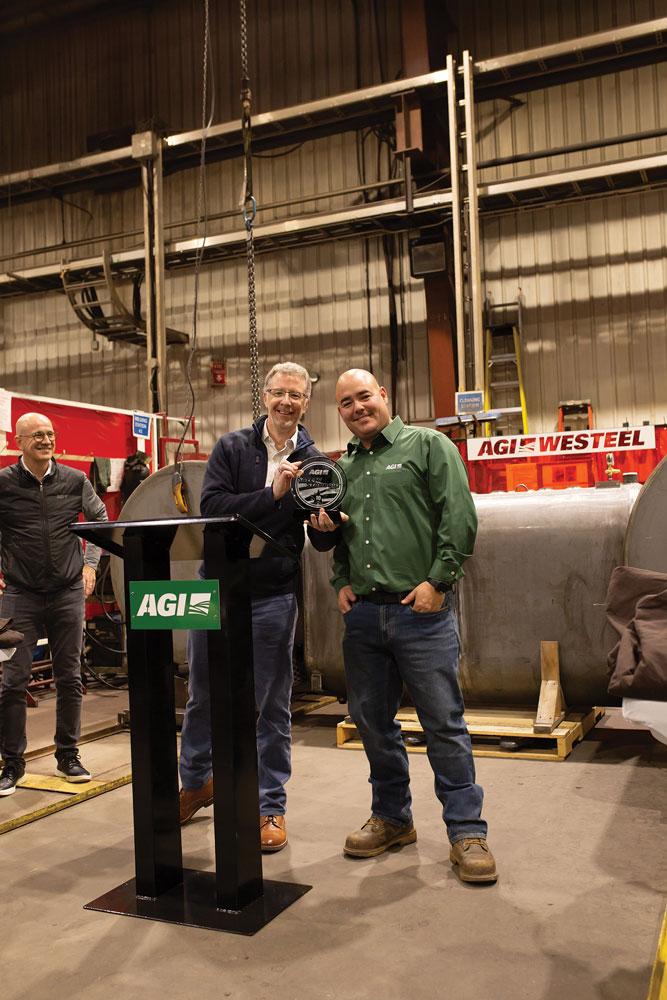
(From left) Paul Householder, AGI president and CEO, presents Steve Ricklefs, AGI Olds plant manager, with an award for 10 years of no lost time incidents. AGI’s concentration on safety starts at the senior management level.
There are daily inspections of all machines, work areas, and equipment to note any deficiencies. The company also has a tagout program, so that if something is found defective, that repair and maintenance is addressed immediately.
“We also have tool box meetings prior to shift start every morning where we’ll talk about a safety topic,” said Ricklefs. “It might be a potential hazard that somebody noted from the day before, or it might be something that the team lead was thinking about at the time, such as a seasonal hazard like ice. We also have our monthly safety meetings, which typically include a training aspect. We use an online program that offers courses for pretty much anything, from lifting heavy objects to winter driving. We may watch a video and then have a quick test to ensure everyone picked up on the key points raised. We’ll then have follow-up discussions where people have a chance to tell their stories, previous issues they’ve had, and what they’ve seen during their careers. It’s a real community event for us that helps build that safety culture.”
The company has a health and safety committee, to which all hazards are reported, and where action plans for mitigation are determined.
COR Support
According to Ricklefs, the shop’s COR (certificate of recognition) designation through the province’s Manufacturers’ Health & Safety Association has also been a great help in maintaining safety management systems. He noted that the designation “requires rigour around hazard assessments, safe operating procedures, and robust modified work programs. They set forth a series of criteria that we need to meet, everything from safety commitments to preventive maintenance policies to up-to-date health and safety manuals. And they audit it annually.”
Ricklefs noted that working with COR makes safety management a natural everyday process.
“It helps us apply our continuous improvement mindset to health and safety,” he said. “If there’s a scope change in a particular part of production, I know I have to go back and check the hazard assessment and verify that the physical demands analysis is still pertinent. That has all become second nature using COR.”
Public Recognition
The Olds facility’s achievements have been recognized externally as well.
“This year, the Steel Tank Institute presented our team with a Safety Award of Excellence for zero OSHA [Occupational Safety and Health Administration] recordable incidents in 2022 and a Safety Award of Achievement for a 10 per cent reduction in the rate of OSHA total recordable incidents,” noted Ricklefs.
Householder emphasized the importance of these safety milestones.
"These important milestones demonstrate that safety, as a value, is deeply ingrained in the people and the processes that make up the AGI Olds facility," he said. “And when it achieves the level of importance that you see here in Olds, safety not only fuels AGI’s success as a global supplier of equipment for the grain, feed, fertilizer, food, and seed sectors, but it contributes to the long-term well-being of families, communities, and the local business economy.”
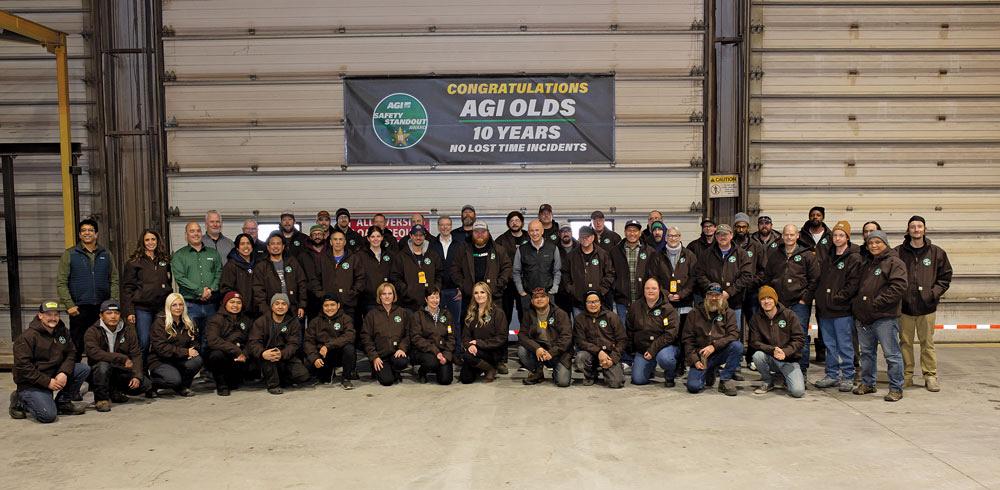
The AGI Olds team celebrates 10 years of no lost time incidents and a strong safety culture, which began years ago after earning its COR (certificate of recognition) designation through the Manufacturers’ Health & Safety Association (MHSA).
Two other AGI manufacturing facilities also were honoured in late November for “no lost time” milestones: Nobleford, Alta., and Joplin, Mo., which celebrated records for three-year no lost time incidence records.
“I really need to emphasize that from the top down, safety is our No. 1 priority,” said Ricklefs. “We encourage talking about safety both in and out of the workplace. And we are very proud of our associates for keeping each other safe. We believe that zero incidents is not just an aspiration but it is an expectation.”
Editor Robert Colman can be reached at rcolman@fmamfg.org.
AGI, www.aggrowth.com
About the Author
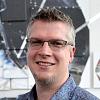
Rob Colman
1154 Warden Avenue
Toronto, M1R 0A1 Canada
905-235-0471
Robert Colman has worked as a writer and editor for more than 25 years, covering the needs of a variety of trades. He has been dedicated to the metalworking industry for the past 13 years, serving as editor for Metalworking Production & Purchasing (MP&P) and, since January 2016, the editor of Canadian Fabricating & Welding. He graduated with a B.A. degree from McGill University and a Master’s degree from UBC.
subscribe now
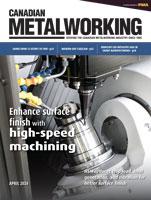
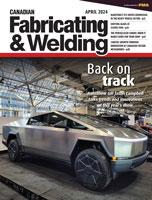
Keep up to date with the latest news, events, and technology for all things metal from our pair of monthly magazines written specifically for Canadian manufacturers!
Start Your Free Subscription- Trending Articles
Aluminum MIG welding wire upgraded with a proprietary and patented surface treatment technology
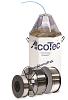
Achieving success with mechanized plasma cutting
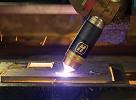
Hypertherm Associates partners with Rapyuta Robotics
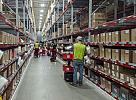
Brushless copper tubing cutter adjusts to ODs up to 2-1/8 in.
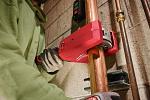
Gema welcomes controller

- Industry Events
MME Winnipeg
- April 30, 2024
- Winnipeg, ON Canada
CTMA Economic Uncertainty: Helping You Navigate Windsor Seminar
- April 30, 2024
- Windsor, ON Canada
CTMA Economic Uncertainty: Helping You Navigate Kitchener Seminar
- May 2, 2024
- Kitchener, ON Canada
Automate 2024
- May 6 - 9, 2024
- Chicago, IL
ANCA Open House
- May 7 - 8, 2024
- Wixom, MI