- FMA
- The Fabricator
- FABTECH
- Canadian Metalworking
The one-two combination
How abrasive wheels for both cutting and grinding make for more efficient work in the field.
- By Canadian Metalworking
- May 11, 2015
- Article
- Metal Finishing
Speaking with surface grinding experts, there really is no one abrasive wheel that fits all applications perfectly when it comes to cutting and grinding, however there are products that will deliver the cutting productivity and grinding stability to safely get the job done.
These so-called combination wheels are typically depressed center, or Type 27, design allowing for the lock nut to recess within the wheel so it won’t interfere with any grinding actions and to also provide the desired rigidity needed for grinding.
Typically, the combination wheels on the market are thin enough to efficiently perform cutting and notching operations while being reinforced enough so an operator is able to put a slight bevel on the end of a pipe or tube, or clean up and deburr any imperfections after cutting.
“Combo wheels are becoming more popular,” says Rick Hopkins, product manager for welding and fabrication with Weiler. “While they are reinforced to handle some level of grinding, they are not designed to handle heavy grinding.”
“Stability, reinforcement is the main factor here,” confirms Rick Hatelt, Ontario Territory Manager with PFERD Canada.
Dedicated cut-off wheels are very thin, around 0.040- or 0.045-inch thickness to deliver fast thin cuts, increasing productivity and reducing the possibility of overheating the metal. The typical construction design of these wheels will include two layers of fiberglass reinforcement.
“In order to handle any type of grinding operation you need a minimum of at least three layers of reinforcement in the wheel,” says Hopkins. For this reason the typical combination cutting/grinding wheels are between 0.065-inches and 1/8th-inch (0.125-inch) thick. These reinforced products not only make the grinding of a surface faster and easier on the operator, but it’s also a major safety concern, as disc breakage can be a serious hazard.
“I would say that some 80 per cent of users out there are using cut-off wheels to deburr after their cut, and the discs are not designed for that application,” says Marc Brunet-Gagné, product manager with Walter Surface Technologies.
“Users don’t want to waste time. They want to do the job fast and well. But while it’s important to be productive and do the job well, it’s more important to work in a safe way.”
Brunet-Gagné notes that operator error leads to most cases of disc breakage, so when the company finds a high recurrence of breakage issues at a location they’ll first offer a safety seminar to ensure the operators are using the product in a safe way, but then they will also recommend that users move to a combination type wheel to prevent further accidents.
“We’ve had a huge success with our Combo Zip product in a very large shipyard factory in Western Canada,” he says. “They were having an issue with the breakage of cut-off wheels, and now they only use the Combo Zip, and no other cut-off wheels are allowed inside the yard.”
While the combination product is welcome from a health and safety standpoint in industrial locations, it’s also a product of convenience for operators out in the field.
Most shops will have multiple grinding tools on hand dedicated to either cutting or grinding, but the operator travelling in a work van from site to site will likely be carrying one grinder, suggests Hatelt. “Quite often that grinder has a cut off disc on it because you can’t cut with a grinding wheel, so that user will cut and deburr with that cut-off disc,” he says.
Of course, since the combination discs are thin they won’t have the same life-span as a ¼-inch dedicated grinding wheel. But where these discs saves time is in disc changeover. Brunet-Gagné notes that even in an industrial setting workers don’t always have a supply of wheels with them, so the trip to get the wheels takes time. “And time is money,” he notes.
Another prime target for these products is the entry-level worker. “For someone just beginning in the metalworking world, this is a very safe wheel,” says Brunet-Gagné. In cases where there are temporary workers being brought on to job sites, these people may not be getting the proper training because there isn’t always time, so having a cross-purpose wheel with a margin for safety makes sense.
“And on top of all of that, it’s a relatively inexpensive product,” notes Hatelt.
Another area where wheels of this size, Type 27 wheels at 1/8th-inch thick, are very well suited is the pipeline industry. Many of the cutting/grinding wheel manufacturers offer a dedicated 1/8th-inch thick pipeline product because an 1/8th-inch is about the size of the gap in the seam between two sections of pipe.
“With bonded abrasives there is a lot of variation in the actual thickness of the product. The thickness that is printed on the wheel is really a nominal thickness. And based on the manufacturing process, there can be a slight variation in the true thickness of a wheel,” explains Hopkins.
“But for the pipeliners that thickness is critical, so the 1/8th-inch pipeliner wheels are true 1/8th-inch wheels.”
These wheels are used primarily for root pass cleaning applications. After welders lay down their initial pass, or the root pass, on a seam, they will hard grind into that bead to clean it out of any impurities and grind down the bead into a concave shape to ready the seam for subsequent passes.
Pipeline welding is a critical application because of the amount of pressure and the potentially hazardous material that’s flowing through the pipes. These welds are x-rayed repeatedly to ensure the seams are cleaned of impurities to lay the foundation for every pass.
“A pipeliner is slightly different from a combination disc,” says Hatelt. “A pipeliner is always a 1/8th-inch thick, and it’s reinforced differently because a pipeliner is used probably 99 per cent of the time on its edge, like a cut-off disc.”
“We say a pipeliner can be used for light grinding, cutting is no problem because it’s reinforced that way, but our DUODISC is reinforced to cut and grind. It has slightly different reinforcing in it that allows it to put that lateral pressure on the angle of the wheel. “
Hopkins explains that Weiler is currently in the process of expanding its bonded abrasive disc line. “We’re very happy with our general purpose line that we have right now (the Vortec Pro),” he notes. The company’s current 1/8th-inch offering is a general purpose disc, but because it’s not triple reinforced it’s not a true combination wheel, so they’ve designated it for notching. He adds that the company will be adding 1/8th-inch combination wheels as part of its complete program going forward.
Weiler is also in the process of doing extensive research on the pipeline industry in order to tailor products specifically to that use.
He notes that aside from root pass cleaning, other applications include facing a section of pipe that’s not butted up against another, where the pipe has been beveled and users will want to grind the sharp edge of that bevel into a slight flat so it will butt together.
“It helps the welder have enough metal material to penetrate that weld and truly fuse those two sections of pipe together,” he explains. “So that’s the type of operation where having a 1/8th-inch combo wheel, where operators can do their cutting or notching and then immediately go on the side of the wheel and do some level of grinding is beneficial.”
Combination cutting and grinding discs deliver productivity benefits because of their versatility, but, it’s the safety benefits of these products that should make them an item to be considered for any applications where cutting and grinding are required.
About the Author
subscribe now
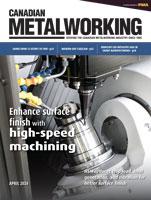
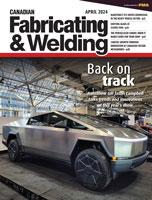
Keep up to date with the latest news, events, and technology for all things metal from our pair of monthly magazines written specifically for Canadian manufacturers!
Start Your Free Subscription- Trending Articles
Aluminum MIG welding wire upgraded with a proprietary and patented surface treatment technology
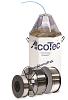
Achieving success with mechanized plasma cutting
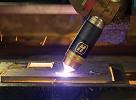
Hypertherm Associates partners with Rapyuta Robotics
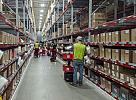
Gema welcomes controller

Brushless copper tubing cutter adjusts to ODs up to 2-1/8 in.
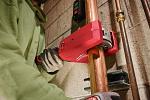
- Industry Events
MME Winnipeg
- April 30, 2024
- Winnipeg, ON Canada
CTMA Economic Uncertainty: Helping You Navigate Windsor Seminar
- April 30, 2024
- Windsor, ON Canada
CTMA Economic Uncertainty: Helping You Navigate Kitchener Seminar
- May 2, 2024
- Kitchener, ON Canada
Automate 2024
- May 6 - 9, 2024
- Chicago, IL
ANCA Open House
- May 7 - 8, 2024
- Wixom, MI