Training and Development Manager
- FMA
- The Fabricator
- FABTECH
- Canadian Metalworking
Upgrading grinding ergonomics
A look at how the latest grinding tech is limiting strains and stresses
- By Steve Schnoll
- February 1, 2024
- Article
- Metal Finishing
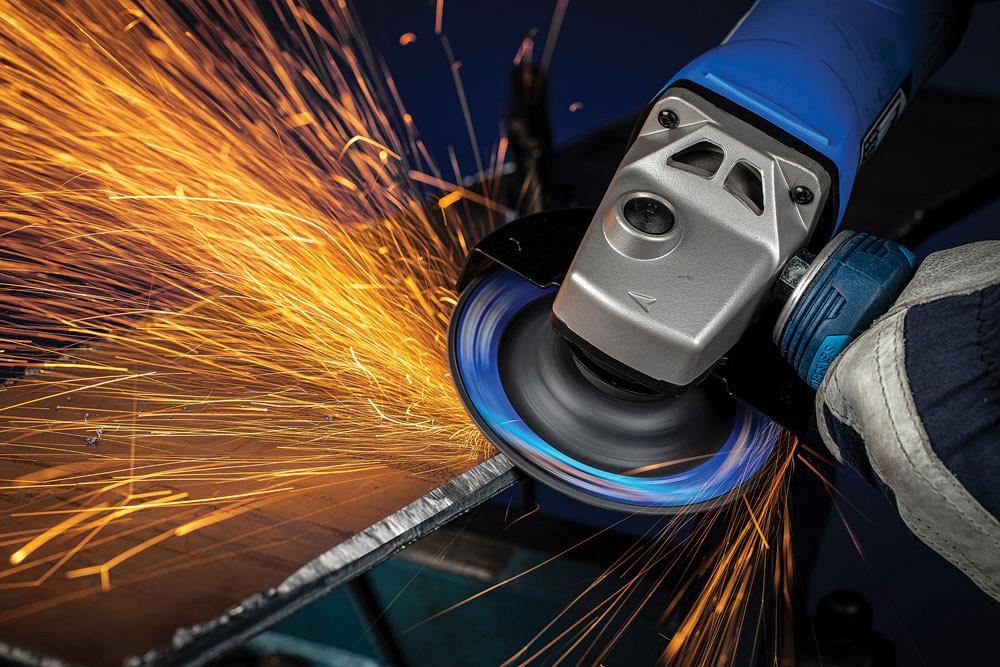
In recent research, the CC-GRIND ROBUST grinding disc produces considerably less noise during use than the grinding wheels used to date. This also was confirmed by noise measurements taken under operating conditions at customers’ premises. Noise emissions fell substantially from over 100 to around 94 dB(A) when using a corded angle grinder, and from over 96 to less than 89 dB(A) when using a cordless angle grinder.
While there is a lot of emphasis placed on health and safety, ergonomics also is an important consideration on the shop floor. A focus on comfortability can lead to long-term success, higher-quality work, and happier workers.
Ergonomics is especially important in grinding operations, which often have noise, dust, and vibration emissions that can lead to decreased safety and comfort.
Following common best practices can help improve ergonomics in grinding work.
Body Stresses and Vibration Emissions
One-off grinding jobs may not necessarily create immediate bodily stresses and strains. However, in today’s manufacturing environment, fabricators are often performing these tasks for the majority of their workday, meaning they are subjected to constant physically taxing work. However, operators can take a few steps to limit the bodily stresses that accompany grinding operations.
Use an Adjustable Vise. This is a simple tool that can make a huge difference when it comes to ergonomics. Not all manufacturers will think about vises, but choosing one that is adjustable will allow for the workpiece to be placed at a proper and comfortable angle for the operator.
For example, every operator might have a different angle of operation that they are comfortable with. An operator who is taller may want to move the workpiece to a different angle so that it sits at waist height and does not create any excess fatigue on the shoulders or neck when grinding.
It's very common to see operators grinding at an improper height. If the workpiece is too high, this can be extremely taxing on arms and shoulders. If it is too low, this can lead to hunching over and back strain. An adjustable vise will not only limit strain and fatigue, but it may also lead to improved performance.
Choose a Tool With an Ergonomic Design. As ergonomics becomes more important, the design of power tools has increasingly followed suit. The term haptic perception is used to describe the active feeling of size, contours, surface structure, and weight of an object by integrating all skin senses and depth sensitiveness.
Handle and trigger placement along with an ergonomic shape and optimized haptics can make all the difference in improved operational comfort. For example, a handle formed with rubber reduces the vibration produced during grinding work by half.
Look for a Grinding Disc With Aggressive Material Removal Rates. As products evolve and integrate the latest technology, a grinding disc with an optimized backer shape will make an ideal amount of contact with the workpiece, which ensures high stock removal coupled with less pressure required. This means operators can exert less force and complete work faster than they would using a standard flap disc or griding wheel.
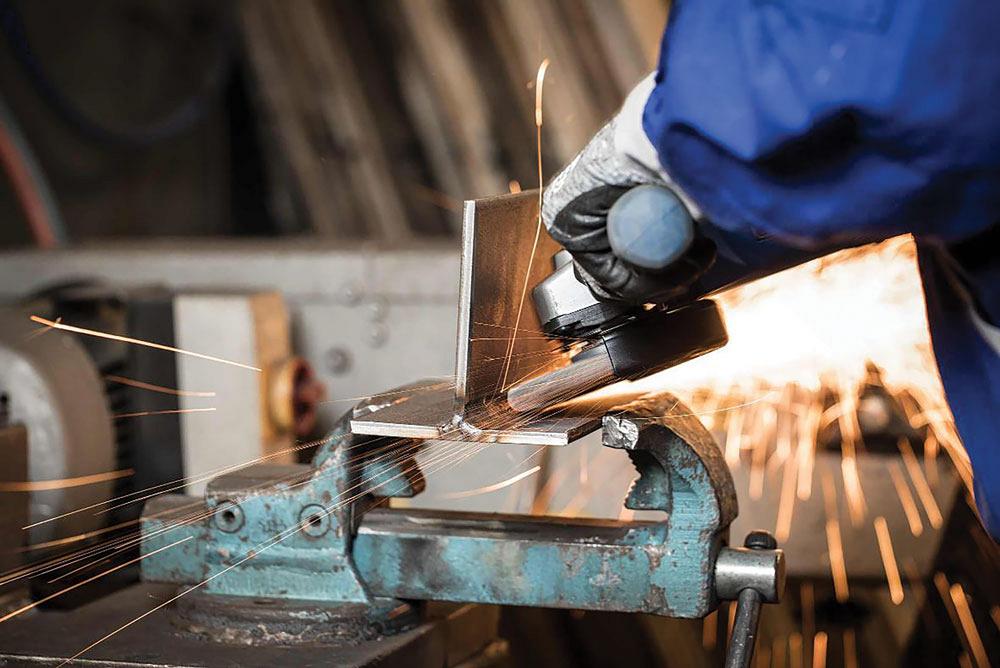
Not all vises are created equal. A static vise can limit an operator’s range of motion and strain their arms. Choosing one that is adjustable will allow for the workpiece to be placed at a proper and comfortable angle for the operator.
Wear Gloves. A protective glove can combine vibration protection with comfort.
The vibrations caused by the grinding process are substantially dampened at the contact surfaces, without impairing dexterity. A glove should be heat resistant, spark resistant, and free of health-hazardous substances.
Noise Issues
Protecting an operator’s hearing and ears during the grinding process is essential, especially because grinding operations typically generate high and sustained noise levels that can damage pressure-sensitive organs within the ear. Prolonged exposure to excessive noise can be detrimental to health and safety. However, even limited noise exposure can have adverse affects, which is why it is important to limit the amount of grinding noise and ensure that workers have properly fitted PPE.
Choose Tools That Limit Noise. While protecting against noise is always advised, it’s important to look for tools that prevent noise from being generated in the first place. Look for grinding discs that reduce overall noise exposure by finishing jobs faster or those that simply create less noise.
Choose noise-abating measures within the process itself, for example, using low-noise machines and drives coupled with adjusting the acoustics in the room.
Wear Proper Ear Protection. PPE will help reduce harmful noise exposure. Manufacturers can work with in-ear or over-ear hearing protection to ensure that noise emissions are limited. However, not all hearing protection is created equal.
For example, it’s important to evaluate how earplugs reduce continuous and impulse noise.
Ear protection like earplugs should be light and comfortable enough to wear all day long, especially when grinding operations take up most of a worker’s day.
In environments where communication is necessary, there are hearing protection options available that make this possible.
The right tools and PPE will help reduce noise exposure.
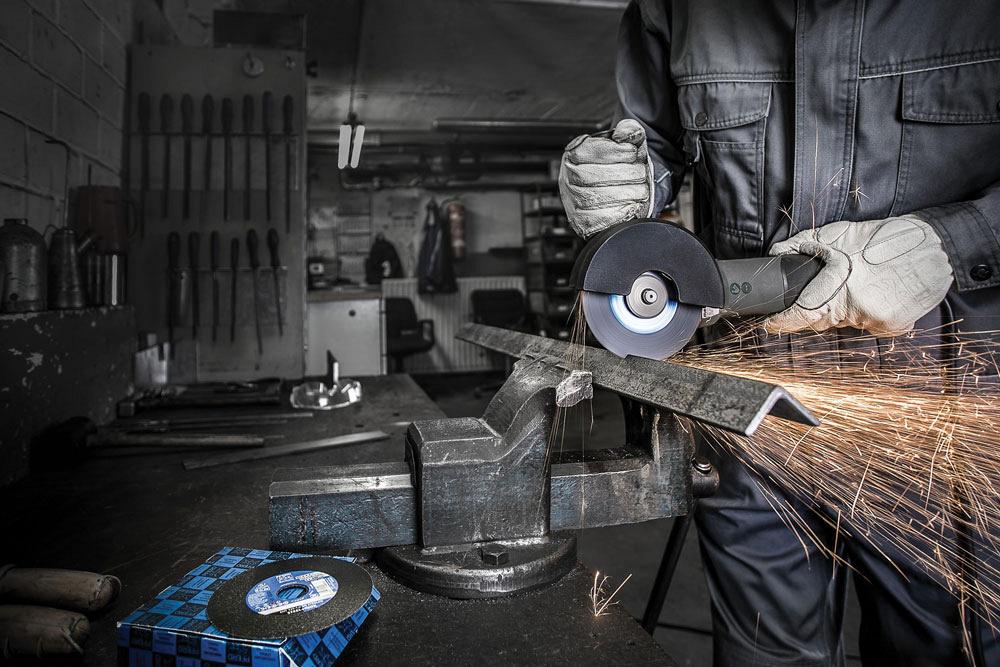
Using a grinder with a guard can help an operator fine-tune where the sparks fly without contorting his or her body to reduce spark exposure.
Dust and Spark Debris
Air quality within working rooms must more or less correspond to outside air. From a health point of view, a dust particle’s size and its pollutant content both matter.
A particle with a diameter larger than 10 µm, also known as called coarse dust, gets caught more easily on nasal hairs or mucous membranes. Smaller dust particles, however, can penetrate deep into the lung via the windpipe and bronchi. For this reason, fine dust is also termed as inhalable or respirable dust.
Use a Flap Disc. A flap disc, as opposed to a traditional grinding wheel, will create a lot less dust. Some of the latest disc technology does not have bond and reinforcement elements that contribute to dust creation.
The aggressiveness of the abrasive grit and the optimum contact angle to the workpiece also mean that the material creates less dust. This is because a flap disc tends to produce chips, not dust. The larger and heavier the chips, the lower the risk of dust entering the lungs.
Use an Adjustable Guard. Adjust the guard when grinding to make sure that the sparks are flying away from both the operator and workers in the area, as opposed to towards them. Being able to fine-tune where the sparks fly will make it easier for the operator to perform grinding operations without contorting his or her body to reduce spark exposure.
Ensure Proper Ventilation. It’s important to make sure that an operator wears proper PPE for ventilation. A dust mask is a good starting point. Look for a mask that provides optimum protection from dust, up to 30 times the maximum workplace concentration.
Also, look for ergonomic features like a breath-out valve, which minimizes the build up of heat and humidity from the user’s breath, or an integrated nose clip that can be adapted to fit comfortably and guarantees a tight fit over the mouth and nose.
Steve Schnoll is training and development manager at PFERD Inc., 9201 W. Heather Ave., Milwaukee, Wis. 53224, us.pferd.com.
About the Author
subscribe now
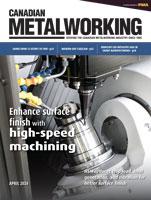
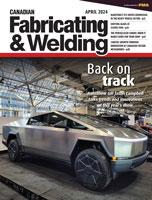
Keep up to date with the latest news, events, and technology for all things metal from our pair of monthly magazines written specifically for Canadian manufacturers!
Start Your Free Subscription- Trending Articles
Aluminum MIG welding wire upgraded with a proprietary and patented surface treatment technology
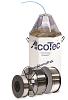
Achieving success with mechanized plasma cutting
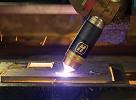
Hypertherm Associates partners with Rapyuta Robotics
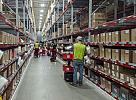
Gema welcomes controller

Brushless copper tubing cutter adjusts to ODs up to 2-1/8 in.
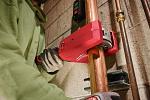
- Industry Events
MME Winnipeg
- April 30, 2024
- Winnipeg, ON Canada
CTMA Economic Uncertainty: Helping You Navigate Windsor Seminar
- April 30, 2024
- Windsor, ON Canada
CTMA Economic Uncertainty: Helping You Navigate Kitchener Seminar
- May 2, 2024
- Kitchener, ON Canada
Automate 2024
- May 6 - 9, 2024
- Chicago, IL
ANCA Open House
- May 7 - 8, 2024
- Wixom, MI