- FMA
- The Fabricator
- FABTECH
- Canadian Metalworking
Is it time for an automated or semi-automated welding system?
Choose the configuration that’s right for you by asking questions of your current processes
- April 18, 2023
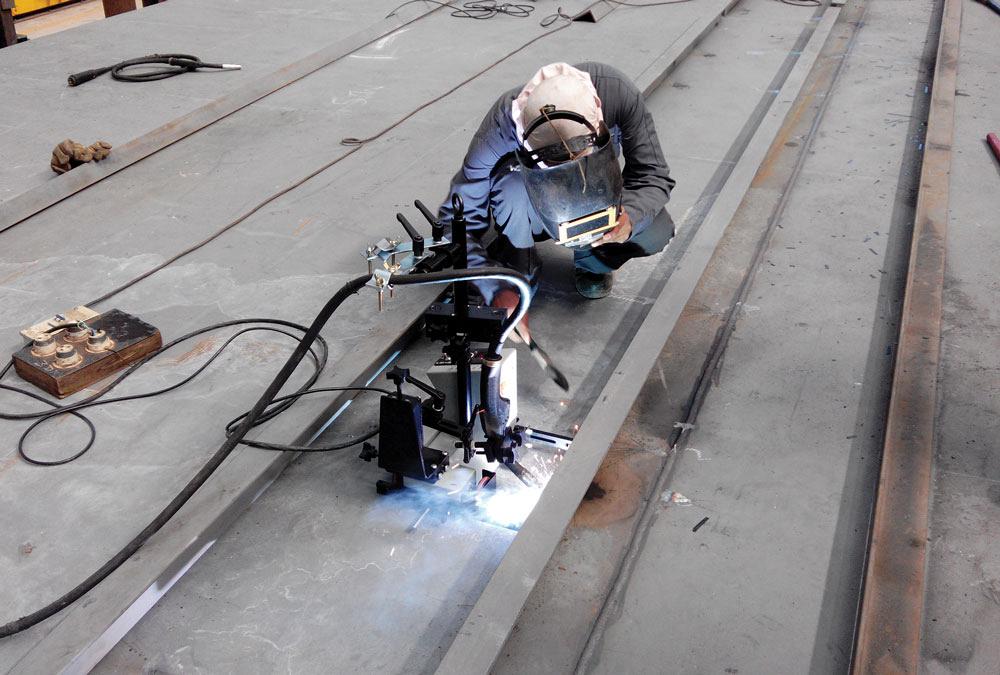
Welding automation from Gullco used to complete this ship hull project resulted in more than 50 per cent savings. The project switched from shielded metal arc welding to mechanized GMAW. Images: Gullco
Welding automation systems use a series of robotic controls and automated equipment attached to a programmed controller. These systems produce high-quality, consistent welds of various types and styles with limited or no human intervention. There are multiple types of welding automation systems. Some units can only perform a single weld type in a specific orientation while other more flexible and programmable units can accommodate multiple weld styles and orientations for complex configurations.
The challenge is determining when to jump into automation, knowing what to expect, and figuring out how to measure your success. Start off by answering a couple of questions about your current operations to understand what is necessary to move forward.
How Do I Know When It’s Time to Move to an Automated System?
Manufacturers are rapidly moving toward automation because of its numerous efficiencies, increases in high-quality production, and reduction in safety hazards and costs. Welding automation in particular can be a smart investment for your organization. Two of the key concerns behind the switch to welding automation are:
- Shortage of skilled labour. Automated welding systems require less human labour to produce the same output. Whether it’s a temporary shortage of labour driven by a peak in demand or a long-term labour shortage because of dwindling availability, welding automation can fill in the gaps and supplement the shortage. Automated systems that do require human operators or overseers require less training and experience, making it easier to fill those roles.
Automated welding systems are ideal for anything that requires continuous welding, such as shipbuilding, rail car production, and bridge construction.
- Quality and consistency concerns. Human welders can offer manual and customizable welding techniques for special projects, but there’s a price for manual welding. Manual labour is naturally going to incur variation from unit to unit, especially as welders become fatigued from prolonged periods of welding or encounter distractions or other obstacles. This results in unpredictable product quality and project slowdowns.
Automated welding systems can significantly speed up turnaround times, increase overall efficiency, and reduce unwanted variability. While human welders deliver as much as 25 per cent efficiency in weld delivery on a very good day, automated systems deliver between 80 and 90 per cent efficiency.
How Do I Pick the Right Equipment?
With so many weld automation systems, customizations, and add-ons available, it’s important to choose the right system for your specific needs. Consider the following factors:
- The position and orientation of the weld in relation to the assembly
- The amount of manual torch control that should be retained for human operators
- The precision and safety add-ons, such as height-sensing equipment, cameras, positioning tools, and remote controls
- The weld profile requirements
- The strategies to reduce direct material handling
Working with a professional consultant or support team during this stage of planning can be invaluable. The right turnkey service team will assess your shop floor or on-site conditioning, provide suggestions based on the environment and the desired applications, and lend advice to optimize current and future equipment use.
How Can I Calculate the ROI for Welding Automation Equipment?
Welding automation equipment is a business expense. So, it’s important to know the upfront and ongoing expenses, as well as the increases in revenue and related reductions in costs. The key factors to include in your calculations are:
Arc-on Time. Manual welding is incredibly inefficient, with an arc-on time of 25 per cent efficiency rate, at best. Further, manual welding requires high skill levels, and it can be very difficult to hire experienced welders. Semi-automatic welding processes, including gas metal arc welding (GMAW), metal-cored arc welding (MCAW), and flux-cored arc welding (FCAW), have greater arc-on efficiency.
Fully automated welding, in which the machine holds and directs the torch, is the most efficient option, with arc-on times reaching 80 to 90 per cent efficiency rates.
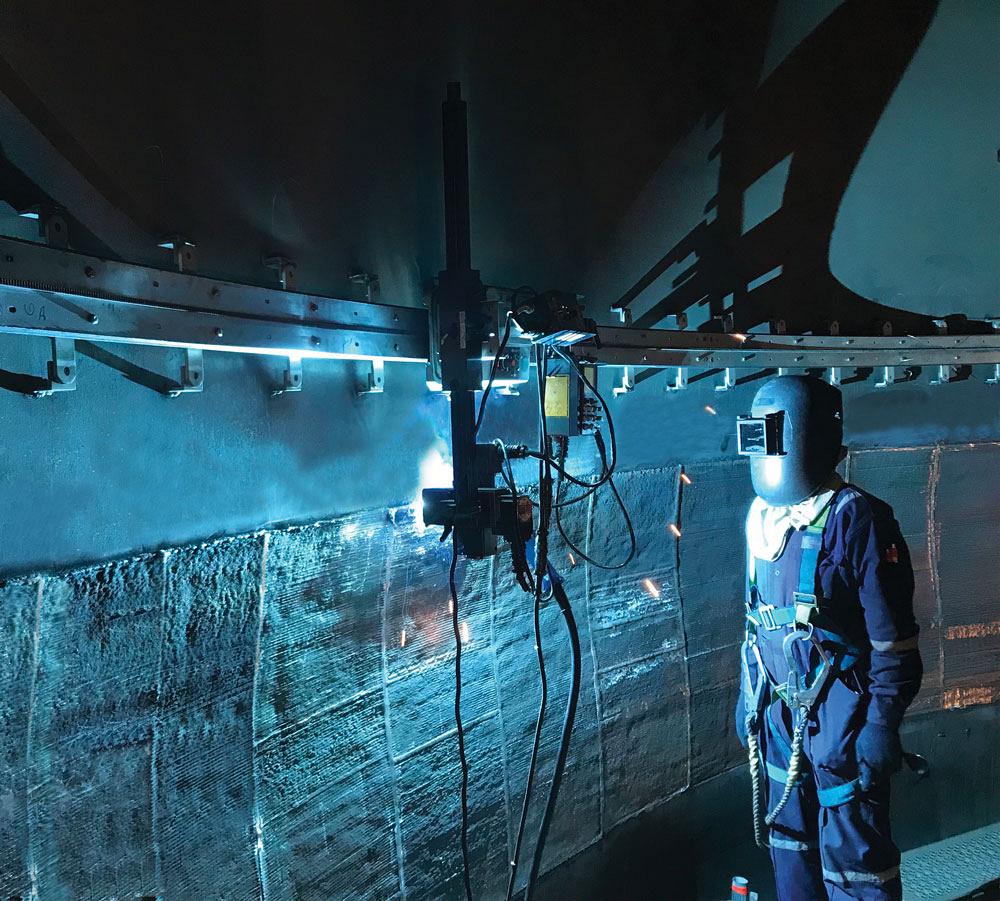
The schedule of the welding volume specified 6 to 7 kg/h of deposited weld metal. Mechanization was necessary to achieve such a high deposition rate and to accommodate various welding positions. Therefore, the welding torches had to be maneuvered around the joints using a welding carriage to provide the motion and control of the weld arc.
Quality and Potential for Defects. Overwelding, mistakes, and inconsistencies result in delays and costly material waste. Overwelding costs organizations millions of dollars in wasted parts and welding materials each year.
Target Payback Period. The “payback period” is the amount of time it will take to recoup the costs of transitioning to an automated system. For large organizations, one year or less is an optimal payback period. Working with a capital expenditure program can help you calculate how long it will take your organization to recoup the total cost of implementing welding automation.
Labour Replacement. Semi-automatic welding systems reduce your reliance on skilled labourers so you can quickly train operators to manage the equipment. Fully automated systems shift your labour requirements and can even open up your equipment to more uses and applications.
Reduced Material Cost. Welding is an expensive portion of the total production costs, making up approximately 28 per cent of the cost of welded goods. With automated processes, you can reduce material and labour costs and increase efficiency with near-immediate benefits on your bottom line.
When Should I Expect ROI?
Calculating the timeline in which you begin to recoup your costs on automated welding equipment is essential so you can predict your payback date and gain insight into the ROI of the transition. Expect both direct and indirect returns quickly.
Automated processes can quickly improve efficiency. If your organization manages large-scale welding orders, you’ll see a faster direct ROI.
Indirect returns should also factor into your calculations. Some of the most beneficial indirect returns include increased product quality and consistency, reduced material waste due to inefficiencies or mistakes, fewer reworks and expensive replacements, and greater production capacity due to reduced delays and wasted time.
Calculating both direct and indirect returns can help you predict your facility’s anticipated payback period. Once the new equipment has been paid for, the efficiencies represent pure profit and the ability to grow your organization.
Nick Drake is marketing manager, Gullco Intl., 1175 Nicholson Rd., Newmarket, Ont. L3Y 9C3, 905-953-4140. This article was adapted from a white paper developed by Gullco. For a link to related case studies, visit www.gullco.com.
subscribe now
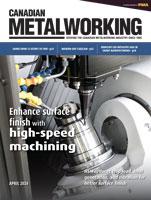
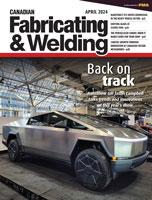
Keep up to date with the latest news, events, and technology for all things metal from our pair of monthly magazines written specifically for Canadian manufacturers!
Start Your Free Subscription- Trending Articles
Aluminum MIG welding wire upgraded with a proprietary and patented surface treatment technology
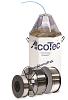
Achieving success with mechanized plasma cutting
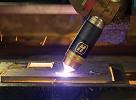
Hypertherm Associates partners with Rapyuta Robotics
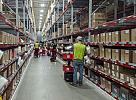
Gema welcomes controller

Brushless copper tubing cutter adjusts to ODs up to 2-1/8 in.
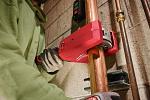
- Industry Events
MME Winnipeg
- April 30, 2024
- Winnipeg, ON Canada
CTMA Economic Uncertainty: Helping You Navigate Windsor Seminar
- April 30, 2024
- Windsor, ON Canada
CTMA Economic Uncertainty: Helping You Navigate Kitchener Seminar
- May 2, 2024
- Kitchener, ON Canada
Automate 2024
- May 6 - 9, 2024
- Chicago, IL
ANCA Open House
- May 7 - 8, 2024
- Wixom, MI