Editor
- FMA
- The Fabricator
- FABTECH
- Canadian Metalworking
Hydrogen fuel cell efficiency push
Exploring the hurdles for a long-haul-friendly tech
- By Rob Colman
- May 12, 2023
Electric vehicles powered with lithium-ion batteries are currently the go-to option for the consumer market. However, the range available using such batteries isn’t ideal for long-haul trucking needs without reducing payloads. For this reason, hydrogen fuel cell propulsion systems have been developed to meet those needs. Manufacturing these systems comes with their own challenges.
On February 9, 2023, the TRUMPF Group held a press conference to discuss how the company sees the future of this technology and what must happen for it to truly become feasible on a large scale. Although production facilities for this technology are being planned or are already under construction, the high cost of manufacturing is still an issue.
The heart of a hydrogen fuel cell is the “stack,” which consists of many bipolar plates that convert hydrogen and oxygen into electricity, which in turn drives the electric motor.
“Without highly sophisticated manufacturing technology and lasers, these ultra-thin metal plates could not be produced economically today,” said Christian Schmitz, member of the managing board, TRUMPF SE + Co. KG, and CEO of TRUMPF Laser Technology. “Welding stainless steel bipolar plates is difficult. We are talking here about fine welds. They are barely visible to the naked eye. The weld seam must be perfect. Even the smallest error would be fatal. This is because hydrogen is the smallest molecule in the world, much smaller than natural gas, and it slips through every crack. A single leaky bipolar plate can render a complete fuel cell stack unusable. The welding process must be of the highest quality. This is best achieved with the laser.”
TRUMPF is quite involved in the manufacture of fuel cells and sees how hydrogen technology has the potential to support the heavy-duty transport sector.
“However, fuel cells are not only used in trucks, buses, or cars,” said Schmitz. “They are also suitable for supplying power to industrial plants and residential buildings, in steel production, the chemical industry, and in aviation. The stationary applications differ from the mobile applications in terms of construction and materials. However, the tasks for the laser remain basically the same.”
One fuel cell stack has between 300 and 500 plates. Welding the plates takes between three and five seconds per plate with the laser technology available today (running 1 m/second).
“At the same time, each plate must be tested to ensure that it is perfect,” noted Johannes Buehrle, head of global industry and business development management – mobility, at TRUMPF Laser Technology. “Testing currently takes 40 seconds per plate. The key for improving the viability of mass production will be speeding up both of these processes.”
TRUMPF is working on integrated sensor systems that ensure quality standards are met while reducing the time and effort required to carry out testing. It is also driving the development of additional laser techniques that it hopes will make the fuel cell manufacturing process even more efficient and cost-effective in the future.
Buehrle noted that the market for heavy-duty trucks is not large enough to drive the hydrogen cell technology forward on its own, however.
“There has to be a push into the light delivery truck market as well,” he noted. “The development of energy storage systems must also be pushed forward to make it worthwhile. The storage technology already exists, it simply needs to be produced cheaply enough to gain market share.”
The push to alternate fuels clearly demands more than one solution. The increased efficiency of hydrogen fuel cell development could be a key additional piece to the puzzle.
Editor Robert Colman can be reached at rcolman@canadianfabweld.com.
The TRUMPF Group, www.trumpf.com
subscribe now
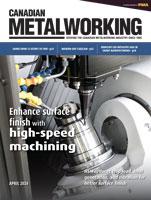
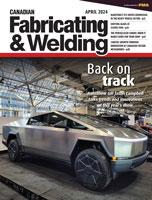
Keep up to date with the latest news, events, and technology for all things metal from our pair of monthly magazines written specifically for Canadian manufacturers!
Start Your Free SubscriptionAbout the Author
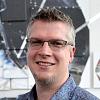
Rob Colman
1154 Warden Avenue
Toronto, M1R 0A1 Canada
905-235-0471
Robert Colman has worked as a writer and editor for more than 25 years, covering the needs of a variety of trades. He has been dedicated to the metalworking industry for the past 13 years, serving as editor for Metalworking Production & Purchasing (MP&P) and, since January 2016, the editor of Canadian Fabricating & Welding. He graduated with a B.A. degree from McGill University and a Master’s degree from UBC.
- Trending Articles
Aluminum MIG welding wire upgraded with a proprietary and patented surface treatment technology
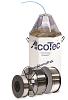
Achieving success with mechanized plasma cutting
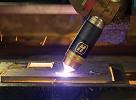
Hypertherm Associates partners with Rapyuta Robotics
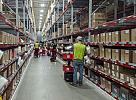
Brushless copper tubing cutter adjusts to ODs up to 2-1/8 in.
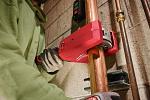
Gema welcomes controller

- Industry Events
MME Winnipeg
- April 30, 2024
- Winnipeg, ON Canada
CTMA Economic Uncertainty: Helping You Navigate Windsor Seminar
- April 30, 2024
- Windsor, ON Canada
CTMA Economic Uncertainty: Helping You Navigate Kitchener Seminar
- May 2, 2024
- Kitchener, ON Canada
Automate 2024
- May 6 - 9, 2024
- Chicago, IL
ANCA Open House
- May 7 - 8, 2024
- Wixom, MI