- FMA
- The Fabricator
- FABTECH
- Canadian Metalworking
Tube Tales
Lasers cut tubes accurately and efficiently.
- By Nestor Gula
- Updated February 13, 2023
- October 7, 2015
- Article
- Fabricating
If all you’re doing is cutting a pipe or tube to length then a saw will do. But if you want to put holes—round or square—into a pipe and make other cuts or profiles, then the prospect of having one machine that can do this makes sense, and today lasers are the answer.
“The whole advantage of lasers is about consolidating operations,” says Jeff Arendas, laser tube product manager at BLM group.
If you were to manually perform tube cutting and preparation, the first step is usually to cut the pipe or tube to length. Then, depending on what the job requires, you would have to start putting the features in. You would do this by drilling, machining, punching or cutting. “The more features you add to the pipe the greater the justification of a laser. Because done manually that would be an incredible amount of setup and tooling involved—saw, probe, mitre, punch, drill, mill, grind, all those operations get consolidated into one automated process. And that is the real payback of the laser. It is being able to load the tube, press the button and get all those operations done fast,” says Arendas.
Selecting laser cutting for tube and pipe is proving to represent more than simply being the most cost effective method of cutting tube and pipe, it’s expanding opportunities for fabricators.
“Companies that have invested in automated tube cutting have discovered new markets: equipment frame and structural supports, construction tubing and I-beam, automotive and truck assemblies, agricultural equipment, recreational vehicles, exercise equipment, trailer industry, metal furniture and accessories, etc.” says Bob Kloczkowski, regional sales manager for ROFIN-SINAR, Inc.
“By having a one-stop manufacturing process, a laser tube cutter will speed up production and increase the accuracy of the work. Cutting of tube and pipe with a laser cutting system is in most cases faster than a conventional machining operation,” says Frank Arteaga, head of product marketing for Bystronic. “Special hard milling tools would be necessary to create the shapes in the pipe. A laser cutter is capable of cutting any shape that has been programmed because of the small diameter of the focused beam (.004- to .008-inch).”
As designs of furniture and other daily objects become more elaborate and compact, manufacturing complexity is increasing. “Many designers consider conventional methods of tube processing when designing a product. With a tube laser you can surpass conventional tube cutting methods. A designer can incorporate difficult end cuts, use slots and tab-type assemblies to make a better product and reduce the amount of fixturing needed in the welding process,” says Mark Mercurio, applications manager with Mazak Optonics.
“This makes for a stronger product that is easier to assemble. And the process is often faster than conventional methods. Conventionally tube processing is a batch process. The user has to process all tubing of the same shape at the same time so they are not constantly changing fixturing and tools required to make a certain shape.”
Modern tube and pipe cutting laser systems allow for new opportunities for designers. Smaller batch runs can be easily accommodated because there is no need for specific tooling and fixturing. “On a tube laser, each tube shape can be different than the previous one,” Mercurio says. “Since the tube laser uses no hard tooling, change over in shapes is much easier. Production can then be scheduled on an “as needed” part basis and not by what tube shape is currently being machined. This leads to less inventory on the shop floor. Also, many of the benefits of the laser tube cutting are in the assembly of the parts after process. Assembly is faster because the parts are more accurate and fit together more accurately.”
A tube cutting laser system can also save floor space by incorporating a storage system in the machine. “You can store a full bundle of material in the bundle loading system, saving space,” says David Dobson, sales engineer of TruLaser for TRUMPF Inc. “The laser serves as the cut off saw, the drill press, and the milling machine and eliminates those machines as well as the material handling between operations. With many materials, there is also no burr when the part is processed with a laser. This eliminates the need for de-burring operations as well. The material will not be handled until it comes off the machine as a finished product. Furthermore, there is only one machine to program and only one operator required. The end result is a finished part that has a much lower cost of manufacturing.”
When choosing a tube cutting laser system one can go for a dedicated automatic system or a flat-bed combination system that will laser cut sheets and perform laser cuts on pipe as well. “Many flatbed lasers already offer an additional rotary axis that is capable of tube processing. These types of flatbed machines have some limitations to the amount of production that can be completed,” says Mercurio, “Flatbed machines with a rotary axis do not have the ability to hold the tube properly during processing. They are fixture intensive and then require set up changes that tube lasers do not require when changing tube shape.
“Also many flatbed lasers do not offer 3D processing that enables the laser to cut the tube on angles. Mazak has a 3D laser offering the rotary chuck that can process tubes at angles that are required. They can also process tubes that require them to be bent before the cutting process.”
Smaller shops that cannot justify the costs of a dedicated automatic laser tube cutting system may opt for the flat-bed with rotary option, but they need to be aware of the system’s limitations. “Flat sheet machines with the rotor attachment are sold more for the sizzle and not the steak. It is a wonderful idea, but it has been lacking in execution. Historically those machines have been around for at least 20 years but no one has really done a really good job,” opines Arendas. “The part that they are missing on all those machines is the ability to compensate for twisted or bowed tubing. Tubing is never straight. That is the most difficult thing in laser cutting tubing. The fact that tubes have twists or bows to them. If you are holding the tube at both ends and it is a banana, as you rotate it the laser is going to go to where the math data says it should go, and your hole is going to be out of whack because the tube is out of whack. That’s just the nature of tubing.
“The automatic machines that are on the market, the TRUMPF, the Mazak and the BLM, all have the ability to compensate for the tube being out of position with a twist or bow, and that is huge when it comes to making accurate parts. The flat table guys will have to struggle for accuracy.”
What the flat-bed systems have is a fast turnaround time to switch from sheet cutting to tube cutting. “It is about a two minute change over time,” says Dru Schwartz, LTC assistant manager for Amada America, Inc.
Flat bed machines also might have limitations on the size of tubes they can work with. “Our FOM2 RI has a size limitation of 8.66-inch round, 6-inch square, 8.66-inch diagonal on a rectangular tube, 3.5-inch angle iron and 6-inch c-channel,” he says. “There are also weight limitations as well. The FOM2 RI has a weight limit of 441 pounds. The machine can also hold a 20-foot stick of material.”
There is no magic number that will let you determine whether you need a laser tube cutting system or if you should get a dedicated system or a combination flatbed system. “If a job should require 200 pieces of square tubing to be processed with 10 holes, five slots and irregular end cuts, the job would probably require drilling, machining and sawing, explains Kloczkowski. “Processing time would include sawing parts to size, setup and fixture for drilling, and finally, programming and processing in machine center; three machines, three handlings, and three labour components to make the parts would probably exceed eight hours total. A laser work station could perform all functions in one handling and one setup; two hours total. Estimated time savings for 200 parts would be six hours as well as man hours for handling and setup.”
Mercurio adds that another advantage is labour, there is less handling of the tubes. The automated tube cutting laser systems can do low and high volumes jobs. But you need the volume.
“In an automated machine the average runtime is—and this is a broad statement—most parts will run between 15 and 60 seconds apiece,” explains Arendas. “That’s kind of your average production on an automated tube cutting machine. So if you are going to spit out, 30 seconds per part, that’s two parts per minute, 120 parts per hour, a thousand parts per shift, then you have enough work to keep the machine busy.”
About the Author
subscribe now
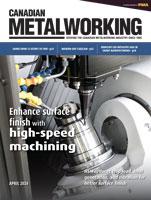
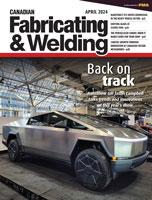
Keep up to date with the latest news, events, and technology for all things metal from our pair of monthly magazines written specifically for Canadian manufacturers!
Start Your Free Subscription- Trending Articles
Aluminum MIG welding wire upgraded with a proprietary and patented surface treatment technology
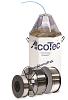
CWB Group launches full-cycle assessment and training program
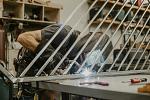
Achieving success with mechanized plasma cutting
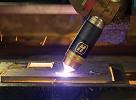
Hypertherm Associates partners with Rapyuta Robotics
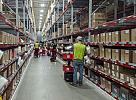
Brushless copper tubing cutter adjusts to ODs up to 2-1/8 in.
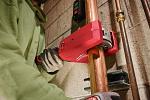
- Industry Events
MME Winnipeg
- April 30, 2024
- Winnipeg, ON Canada
CTMA Economic Uncertainty: Helping You Navigate Windsor Seminar
- April 30, 2024
- Windsor, ON Canada
CTMA Economic Uncertainty: Helping You Navigate Kitchener Seminar
- May 2, 2024
- Kitchener, ON Canada
Automate 2024
- May 6 - 9, 2024
- Chicago, IL
ANCA Open House
- May 7 - 8, 2024
- Wixom, MI