Chief Technology Officer
- FMA
- The Fabricator
- FABTECH
- Canadian Metalworking
Laser cleaning
A new option for material prep
- By Alex Fraser
- Updated February 3, 2022
- February 4, 2022
- Article
- Welding
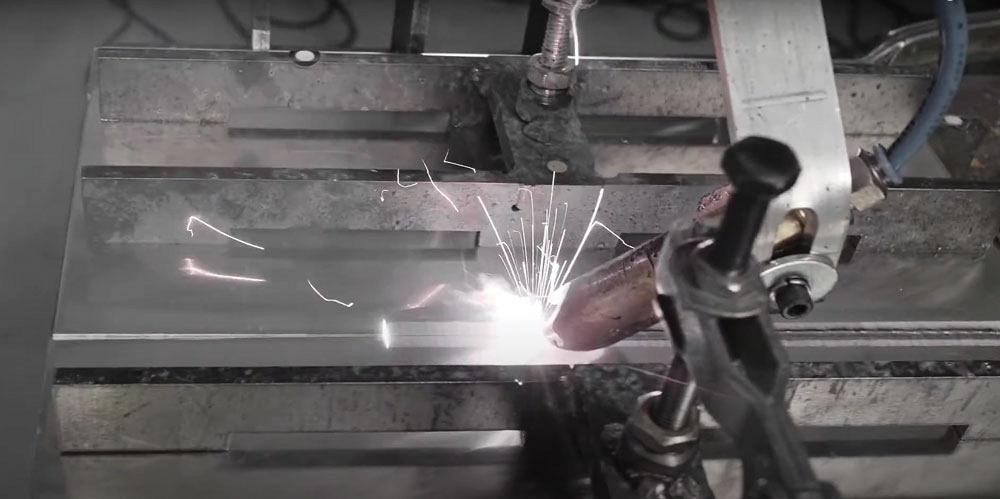
Laser cleaning is the most effective way to ensure components are cleaned all the way to the bare metal without damaging the substrate.
Laser cleaning is a specialized process increasingly adopted by manufacturers as an option for surface preparation. They use laser cleaning to prepare metal surfaces for welding, painting, powder coating, adhesive bonding, and assembly.
As a sustainable method, it can be used in a variety of applications that are not possible with abrasive blasting, grinding, or chemical cleaning.
What Is Laser Cleaning?
Laser cleaning uses laser radiation to remove contaminants from metal surfaces. It focuses nanosecond-length pulses of laser light on surfaces. As it interacts with contaminants that absorb the light, the light intensity causes particles to break free or change into a gaseous state.
These particles are extracted using a fume extraction and filtration system to prevent hazardous substances from being released into the air.
Laser cleaning is the most effective way to ensure components are cleaned all the way to the bare metal without damaging the substrate. It can remove any type of contaminant without etching the base metal. This is especially important in applications such as cleaning parts for the aerospace industry and before welding.
Because laser cleaning can work at different energy levels, it also can be used to etch the surface while removing contaminants. This can improve the processing speed and create a surface texture that improves adhesion before coating applications.
In addition, laser cleaning can be used to enhance products while reducing processing steps. For example, a German aircraft parts supplier is using laser treatment to clean surfaces while creating what it calls “riblets” on surfaces. These riblets are tiny lateral grooves in the uppermost layers of the surface that improve airflow and reduce fuel use.
Localized Cleaning Creates Possibilities
One of the strengths of laser cleaning is that it can be programmed to clean very specific areas — and only those areas. This creates new possibilities not viable with other methods, including the following:
Removing part masking: Part masking prevents certain areas of a part from being processed to maintain the its integrity and function.
For example, many automotive manufacturers use masking to prevent coatings from sticking to specific areas. Before welding, coatings might contaminate the weld and lead to defects. Areas also need to be coating-free to ensure a cohesive assembly.
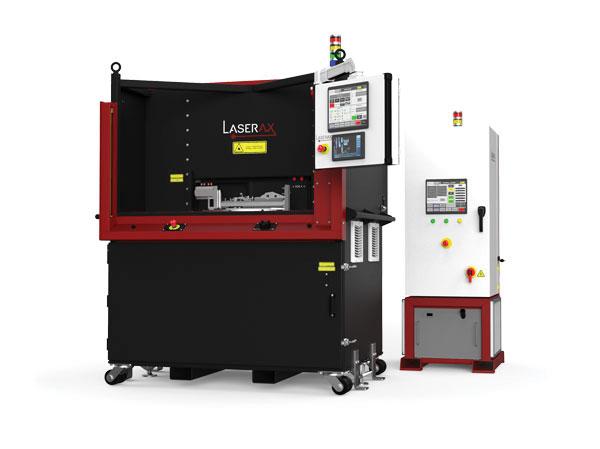
A laser enclosure equipped with a rotary table can either be manually loaded or fed by a robot. The laser cleaning operation is performed in the enclosure.
Part masking is labour-intensive. It’s also prone to human error, which in turn increases costs, scrap, and rework. It can slow down the entire coating process and requires the use of additional consumables.
Laser cleaning allows manufacturers to coat an entire part and then clean localized areas with precision.
Cleaning areas used for assembly: Areas used for assembly may be covered in a phosphate coating. This is often the case with drivetrain components such as pinions and ring gears. When the coating from assembly areas is removed, the assembly’s strength can be improved.
Since laser cleaning can strip coatings from localized areas with extreme precision, it is possible to remove iron phosphate coatings, manganese phosphate coatings, and zinc phosphate coatings from isolated areas. The high temperature of the laser beam ablates the coating without damaging the metal.
Cleaning for weld prep more efficiently: Metals with any kind of rust, dirt, or other impurities can make welding more difficult. Contaminants lead to weaker welds because of porosity, so surfaces must be thoroughly cleaned to prevent contaminants from penetrating welds.
Laser cleaning allows for a prompt, high-quality cleaning of surfaces, which helps in creating durable welds.
Strategies to Integrate Laser Cleaning
Different strategies can be used to integrate laser cleaning in a metalworking process, as shown in the pictured examples. In all cases, laser safety is achieved using an enclosure that follows Class-1 laser safety standards.
Handheld devices are seldom used in production lines. They are better suited for refurbishing, reworking, and maintenance purposes. Unlike laser safety enclosures, handheld devices require training and PPE to be operated safely.
A laser enclosure equipped with a rotary table can either be manually loaded or fed by a robot. The laser cleaning operation is performed in the enclosure.
An enclosure can be installed on a conveyor so that laser cleaning can be performed on the fly.
A laser cleaning system mounted on a robot arm can provide flexibility when integrating the cleaning operation in a production line.
Sustainable Cleaning Technology
The number of electric vehicles (EVs) on the road continues to grow. While EVs create a lower carbon footprint over their lifetime than vehicles using traditional internal combustion engines, the industry is often criticized for generating more emissions during manufacturing than gas-powered engines. Estimates are that EV battery production, for example, can result in an increase of emissions by as much as 30 to 40 per cent.
Any opportunity for more sustainable production should be encouraged. But traditional cleaning methods are far from sustainable; they generate waste through consumables, chemicals, wastewater, and replaceable machine parts.
Laser cleaning can significantly reduce consumable use during cleaning. Technological advances in fibre lasers also mean that the lifespan of the laser itself should be longer than might have been possible even five years ago.
Laser cleaning offers new possibilities not viable with other technologies like abrasive blasting, grinding, and chemical cleaning. With the growing concern from governments, manufacturers, and consumers about sustainability and environmentally friendly manufacturing processes, the use of laser cleaning in fabricating and metalworking will continue to grow as well.
Alex Fraser, is chief technology officer at Laserax, 2811 Avenue Watt, Québec, Que. G1X 4S8, 844-471-0144, afraser@laserax.com, www.laserax.com.
About the Author
subscribe now
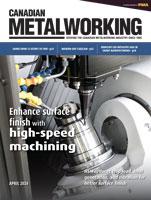
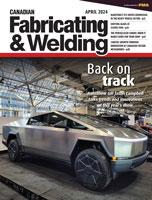
Keep up to date with the latest news, events, and technology for all things metal from our pair of monthly magazines written specifically for Canadian manufacturers!
Start Your Free Subscription- Trending Articles
Aluminum MIG welding wire upgraded with a proprietary and patented surface treatment technology
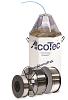
Achieving success with mechanized plasma cutting
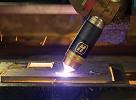
Hypertherm Associates partners with Rapyuta Robotics
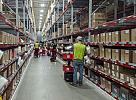
Gema welcomes controller

Brushless copper tubing cutter adjusts to ODs up to 2-1/8 in.
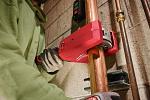
- Industry Events
MME Winnipeg
- April 30, 2024
- Winnipeg, ON Canada
CTMA Economic Uncertainty: Helping You Navigate Windsor Seminar
- April 30, 2024
- Windsor, ON Canada
CTMA Economic Uncertainty: Helping You Navigate Kitchener Seminar
- May 2, 2024
- Kitchener, ON Canada
Automate 2024
- May 6 - 9, 2024
- Chicago, IL
ANCA Open House
- May 7 - 8, 2024
- Wixom, MI